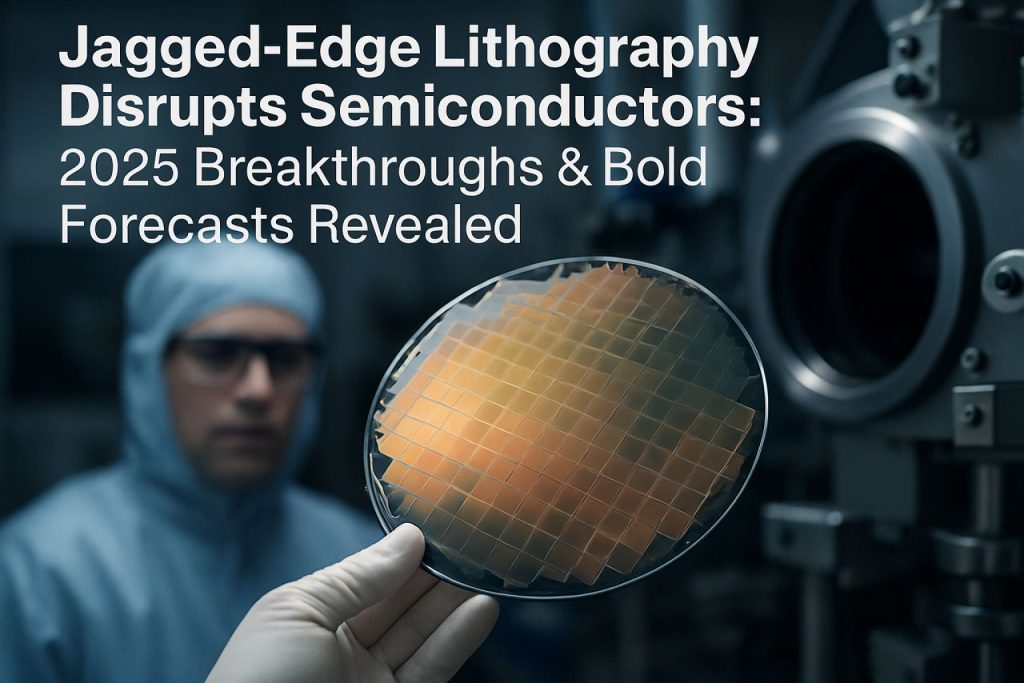
Inhaltsverzeichnis
- Zusammenfassung: 2025 an der Wegscheide der Zahnradhardware-Lithografie
- Technologieüberblick: Wie Zahnradhardware-Lithografie funktioniert
- Wichtige Akteure und Innovatoren: Führende Unternehmen & Branchenallianzen
- Marktgröße und Wachstumsprognosen bis 2030
- Adoptionsfaktoren: Leistung, Effizienz und Miniaturisierung
- Technische Herausforderungen und Einschränkungen im Jahr 2025
- Wettbewerbsumfeld: Vergleich zwischen traditionellen und Zahnradhardware-Ansätzen
- Neue Anwendungen in KI, IoT und Rechenzentren
- Regulierungsstandards und Branchenrichtlinien
- Zukunftsausblick: Fahrplan, disruptives Potenzial und strategische Empfehlungen
- Quellen & Hinweise
Zusammenfassung: 2025 an der Wegscheide der Zahnradhardware-Lithografie
Im Jahr 2025 steht die Zahnradhardware-Lithographie für Halbleiter an einem entscheidenden Wendepunkt, der sowohl das Versprechen als auch die Herausforderungen verdeutlicht, die mit der Herstellung von Geräten der nächsten Generation verbunden sind. Der unermüdliche Antrieb der Branche zum Erreichen von Sub-2-nm-Nodes und fortschrittlicher Verpackung hat die Grenzen der konventionellen Fotolithographie aufgezeigt, was führende Hersteller veranlasst hat, Zahnradhardware- oder „gezackte Linien“-Musterungstechniken zu erforschen, um Probleme mit der Kantenrauheit (LER) und der Variabilität zu überwinden. Große Akteure wie ASML und die Intel Corporation haben öffentlich ihre Verpflichtung zur Verfeinerung der Lithographie mit extrem ultraviolettem Licht (EUV) und komplementären Musterungsverfahren bekräftigt, wobei Strategien der Zahnradhardware zunehmend entscheidend für die Erreichung der erforderlichen Auflösung und Ausbeute werden.
Jüngste Fortschritte in der Maskentechnologie und in Resistmaterialien haben eine präzisere Kontrolle über die Kantenbeschreibung ermöglicht, wobei TSMC und Samsung Electronics berichteten, dass die Geräteuniformität verbessert und die Kantenrauheit in Pilotproduktionsläufen, die auf die 1,4-nm- und 2-nm-Nodes abzielen, reduziert wurde. Diese Entwicklungen sind direkt mit laufenden Investitionen in neuartige Resistchemien und hoch-NA (numerische Apertur) EUV-Scanner verbunden, wie in den technischen Briefings von 2024 hervorgehoben, die von ASML durchgeführt wurden, die aktiv mit Geräteherstellern zusammenarbeiten, um die Kontrolle über die Zahnradhardware-Musterung sowohl für Logik- als auch für Speicheranwendungen zu optimieren.
Trotz dieser technischen Fortschritte bleibt der Ausblick für die Zahnradhardware-Lithographie auf kurze Sicht differenziert. Kosten- und Komplexitätsbedenken sind ausgeprägt, wobei GlobalFoundries und Infineon Technologies AG die Verengung des Prozessfensters und das Management der Defektanzahl als fortwährende Hindernisse für die hochvolumige Einführung identifizieren. Branchenkonsortien, einschließlich SEMI, fördern die Zusammenarbeit in der Forschung, um die Standardisierung in Bezug auf die Metrologie von Zahnradhardware-Prozessen und die Integration in bestehende EUV- und DUV (tiefe ultraviolette) Infrastrukturen zu beschleunigen.
In den kommenden Jahren werden iterative Verbesserungen in der Maskentreue, Resistempfindlichkeit und Prozesskontrollsoftware definiert sein. Bei steigender Chip-Nachfrage für KI, Hochleistungsrechnen und Automobilanwendungen wird die Fähigkeit, Zahnradhardware-Muster konsistent und in großem Maßstab zu reproduzieren, ein entscheidender Faktor für die Marktführerschaft sein. Bis 2027 erwartet die Industrie, dass die Zahnradhardware-Lithographie von einer spezialisierten Technik zu einem Mainstream-Ermöglicher für fortschrittliche Nodes übergeht, vorausgesetzt, dass technische und wirtschaftliche Barrieren durch laufende Zusammenarbeit zwischen Geräteanbietern, Foundries und Materialinnovatoren ausreichend angegangen werden.
Technologieüberblick: Wie Zahnradhardware-Lithografie funktioniert
Die Zahnradhardware-Lithographie für Halbleiter stellt eine strategische Evolution in fortschrittlichen Musterungsverfahren dar, die sich auf das beabsichtigte Design und die Kontrolle der Kantenrauheit im Nanomaßstab konzentriert. Im Gegensatz zur konventionellen Lithographie, die darauf abzielt, die glättesten möglichen Kanten für Transistoren und Verbindungen zu erzeugen, nutzt die Zahnradhardware-Lithographie kontrollierte Unregelmäßigkeiten entlang der Kanten der Muster, um neuartige Gerätearchitekturen zu ermöglichen und möglicherweise die Geräteleistung zu verbessern.
Der zentrale Workflow der Zahnradhardware-Lithographie im Jahr 2025 beruht nach wie vor auf tiefem ultraviolettem Licht (DUV) und zunehmend extrem ultraviolettem Licht (EUV) Fotolithographiewerkzeugen, wobei wichtige Industriezulieferer wie ASML und Canon Inc. die fortschrittlichen Belichtungssysteme bereitstellen, die für die Strukturierung von Mustern unter 10 nm erforderlich sind. Der Unterschied liegt jedoch im Design von Maske und Resist sowie in ausgeklügelten Prozesskontrollalgorithmen, die absichtlich das Belichtungsmuster modulieren, um gezackte und nicht perfekt gerade Linienkanten zu erzeugen. Dies wird durch rechnergestützte Lithographietechniken erzielt, die die optimale Maskenform berechnen, wobei die gewünschte Kantenrauheit und die stochastische Natur der Photon- und Elektronenwechselwirkungen an der Waferoberfläche berücksichtigt werden.
Materialinnovationen sind ebenfalls entscheidend. Unternehmen wie TOK (Tokyo Ohka Kogyo) und JSR Corporation entwickeln neue lichtempfindliche Chemien, die absichtlich erzeugte Kantenmerkmale zuverlässig reproduzieren und die Musterunregelmäßigkeit unter den Bedingungen der hochenergetischen EUV-Belichtung aufrechterhalten können. Der Prozessablauf kann Techniken zur geleiteten Selbstmontage (DSA) beinhalten, bei denen Blockcopolymere durch vorgegebene gezackte Vorlagen geleitet werden, um die Kantenunregelmäßigkeiten auf kontrollierte Weise weiter zu verstärken – eine Methode, die von kollaborativen Konsortien wie imec erkundet wird.
Für die inline-Metrologie und Inspektion haben führende Anbieter von Halbleiteranlagen wie KLA Corporation ihre Messsysteme weiterentwickelt, um Kantenrauheit (LER) und Linienbreitenrauhigkeit (LWR) auf atomarer Ebene zu quantifizieren und sicherzustellen, dass die Zacken innerhalb der Zielvorgaben liegen. Die Prozesskontrolle wird zusätzlich durch fortschrittliche rechnergestützte Modelle und Algorithmen des maschinellen Lernens unterstützt, um Kantenattribute in Echtzeit während der Herstellung vorherzusagen, zu überwachen und zu optimieren.
In der Zukunft wird ein zunehmender Einsatz der Zahnradhardware-Lithographie in der Herstellung von Logik- und Speichergeräten der nächsten Generation erwartet, wobei die Pilotproduktion bereits an ausgewählten Foundries mit EUV-Doppelmustern und Maskenoptimierung im Gange ist. Die Fähigkeit, Kantenrauheit zu manipulieren, eröffnet neue Möglichkeiten in der Geräteentwicklung, einschließlich der Kontrolle von Quantentunneln und Variabilitätsengineering, die aktiv von führenden Forschungs- und Produktionsorganisationen erkundet werden.
Wichtige Akteure und Innovatoren: Führende Unternehmen & Branchenallianzen
Die Entwicklung und Kommerzialisierung der Zahnradhardware-Lithographie für Halbleiter – eine Technik, die darauf abzielt, die Auflösungsgrenzen traditioneller Methoden durch kontrollierte Kantenrauheit zu überwinden – hat sich zu einem Wettbewerbsfokus unter führenden Herstellern von Halbleiterausrüstung und kooperativen Branchenallianzen entwickelt. Im Jahr 2025 treiben mehrere Schlüsselakteure aktiv diese Technologie voran, integrieren sie in die Herstellung von Nodes der nächsten Generation und erkunden ihr Potenzial für Logik- und Speichergeräte.
ASML, der dominante Anbieter von lithographischen Systemen mit extrem ultraviolettem Licht (EUV), bleibt zentral für die Entwicklung von Zahnradhardwarestrategien. Die jüngsten Updates der EUV-Plattform des Unternehmens haben Module zur Korrektur von Kantenplatzierungsfehlern (EPE) und fortschrittliche Musterungskontrollen integriert, die eine engere Überlagerung und die Rauheitskontrolle ermöglichen, die für die Zahnradhardware-Musterung bei sub-2-nm-Nodes erforderlich sind. Im Jahr 2024 hat ASML mit großen Foundries zusammengearbeitet, um die Produktionsfähigkeit von gezackten Funktionen zu validieren, wobei Pilotläufe an ausgewählten Kundensites ASML begonnen haben.
Tokyo Electron (TEL) hat sich als führend im Bereich Ätzen und Abscheideausrüstung etabliert, die für die atomgenaue Übertragung von Zahnradhardware-Muster in Silizium entscheidend ist. Die neuesten Trockenätzplattformen von TEL, die 2024 eingeführt wurden, bieten Echtzeitüberwachung und adaptive Kontrolle der Kantenrauheit, was die Massenanwendung der Zahnradhardware-Lithographie für SRAM- und fortschrittliche DRAM-Produktion erleichtert Tokyo Electron.
Applied Materials nutzt sein Fachwissen in der Prozesskontrolle und Metrologie zur Unterstützung der Zahnradhardware-Lithographie. Die neuesten Inspektionswerkzeuge des Unternehmens, die mit Algorithmen des maschinellen Lernens ausgestattet sind, bieten nun eine subnatürliche Auflösung bei der Messung von Kantenrauheit, was die Rückkopplungsschleifen ermöglicht, die für die Verbesserung der Ausbeute unerlässlich sind, da dieser Musterungsansatz in die Hochvolumenproduktion eintritt Applied Materials.
Branchenallianzen wie imec und SEMI sind ebenfalls entscheidend, indem sie als neutrale Plattformen für vorkonkurrierende Forschung und unternehmensübergreifende Zusammenarbeit fungieren. Die Forschungsprogramme von imec aus dem Jahr 2024 haben die ersten integrierten Schaltkreise unter Verwendung der Zahnradhardware-Lithographie am 1,4-nm-Node demonstriert, wobei eng mit Werkzeugherstellern und Materialanbietern zusammengearbeitet wurde. SEMI hingegen fördert die Standardisierungsbemühungen rund um die Metriken der Kantenrauheit und die Interoperabilität zwischen Lithographie- und Metologiesystemen.
In den nächsten Jahren wird erwartet, dass diese Unternehmen und Allianzen die Einführung der Zahnradhardware-Lithographie beschleunigen, insbesondere wenn die Branche sich mit den Skalierungsgrenzen traditioneller Musterungstechniken auseinandersetzt. Mit Pilotlinien, die in die Erstproduktion übergehen, und mehr Fabs, die fortschrittliche Kontrollsysteme integrieren, sind Zahnradhardwarestrategien leicht in der Lage, eine zentrale Rolle beim Erreichen von Sub-2-nm-Technologie-Nodes und darüber hinaus zu spielen.
Marktgröße und Wachstumsprognosen bis 2030
Die Zahnradhardware-Lithographie für Halbleiter, eine fortschrittliche Musterungstechnologie, die darauf abzielt, die Grenzen der konventionellen Fotolithographie bei fortschrittlichen Nodes zu überwinden, steht bis 2030 vor einem signifikanten Wachstum. Diese Technik ist besonders relevant, da die Halbleiterindustrie auf Sub-3-nm-Prozessknoten zusteuert, wo Kantenrauheit, Musterunregelmäßigkeit und Gerätereproduzierbarkeit kritische Faktoren werden. Im Jahr 2025 ist die Einführung der Zahnradhardware-Lithographie hauptsächlich bei fortschrittlichen Foundries und integrierten Geräteherstellern (IDMs) zu beobachten, die in Logik- und Speichergeräte der nächsten Generation investieren.
Aktuelle Schätzungen von Branchenführern deuten darauf hin, dass der globale Markt für Halbleiter-Lithographieausrüstung im Jahr 2025 auf etwa 25 Milliarden US-Dollar geschätzt wird, wobei die Werkzeuge zur Zahnradhardware-Lithographie einen kleinen, aber schnell wachsenden Anteil daran ausmachen. Pioniere wie ASML und Canon Inc. entwickeln und vermarkten aktiv Lithographieplattformen, die in der Lage sind, die Zahnradhardware-Musterung zu unterstützen, oft unter Verwendung von hochgradigen EUV (extrem ultraviolettes Licht) und mehrfachen Musterungsverfahren, um diese Merkmale zu ermöglichen. TSMC und die Intel Corporation haben solche Innovationen in ihre fortschrittlichen Fertigungsfahrpläne integriert und betonen ihre Bedeutung für Leistung und Skalierung bei den fortschrittlichsten Nodes.
Von 2025 bis 2030 wird prognostiziert, dass das Segment der Zahnradhardware-Lithographie mit einer jährlichen Wachstumsrate (CAGR) von über 20 % wachsen wird und damit das breitere Wachstum des Lithographiemarktes übertreffen wird. Diese Beschleunigung wird durch die steigende Nachfrage nach Hochleistungsrechnen, KI-Beschleunigern und 5G-Anwendungen angeheizt, die alle dichtere, präzisere Gerätearchitekturen erfordern. Wenn führende Chiphersteller wie Samsung Electronics und Micron Technology die Produktion von DRAM-, NAND- und Logikchips an fortschrittlichen Nodes ausweiten, wird ein Anstieg der Nachfrage nach Ausrüstung und Prozesslösungen für Zahnradhardware-Lithographie erwartet.
- Bis 2027 wird erwartet, dass die branchenweite Einführung auf eine breitere Gruppe von Foundries und IDMs, insbesondere in Asien und Nordamerika, ausgeweitet wird, da sich die Kostenstrukturen verbessern und die Prozessreife zunimmt.
- Bis 2030 könnte die Zahnradhardware-Lithographie bis zu 15 % des gesamten Verkaufs von fortschrittlichen Lithografieanlagen ausmachen, so die Prognosen von führenden Ausrüstungsanbietern.
Der Ausblick für die Zahnradhardware-Lithographie ist eng mit laufenden F&E-Investitionen, der Bereitschaft der Lieferkette und der Zusammenarbeit zwischen Geräteherstellern und Halbleiterproduzenten verbunden. Da technische Herausforderungen angegangen und Kosteneffizienzen realisiert werden, wird erwartet, dass die Zahnradhardware-Lithographie eine zentrale Rolle in der Evolution der fortschrittlichen Halbleiterherstellung im Laufe des Jahrzehnts spielt.
Adoptionsfaktoren: Leistung, Effizienz und Miniaturisierung
Die Einführung der Zahnradhardware-Lithographie für Halbleiter wird von mehreren zusammenlaufenden Faktoren vorangetrieben, insbesondere dem unaufhörlichen Drang nach höherer Leistung, verbesserter Energieeffizienz und weiterer Miniaturisierung in der Chip-Produktion. Wenn die Halbleiterindustrie sich den physikalischen Grenzen der traditionellen Fotolithographie nähert, insbesondere bei Nodes unter 2 nm, wird die Notwendigkeit für innovative Musterungstechniken dringend. Die Zahnradhardware-Lithographie, die kontrollierte Unregelmäßigkeiten im Nanomaßstab einführt, zeigt sich als vielversprechende Lösung für diese Herausforderungen und ermöglicht verbesserte Geräteeigenschaften, während der Energieverbrauch gleich bleibt oder sogar reduziert wird.
Einer der Hauptanreize besteht darin, Leistungssteigerungen durch präzisere Kontrolle der Kanalgeometrie in Transistoren zu erzielen. Durch den Einsatz der Zahnradhardware-Lithographie können Hersteller die Kanten von Transistoren feinabstimmen, um die Elektronenmobilität zu optimieren und die Variabilität im Geräteverhalten zu verringern. ASML Holding, ein führender Anbieter von Lithographie-Ausrüstung, hat die Notwendigkeit solcher fortschrittlichen Musterungsverfahren hervorgehoben, um die lithographische Technologie mit extrem ultraviolettem Licht (EUV) zu ergänzen, wenn die Branche sich auf 1,4 nm und darüber hinaus zubewegt. Der Zahnradhardwearansatz kann die benötigte Auflösungsverbesserung für diese ultra-feinen Nodes bieten und die Entwicklung schnellerer und zuverlässigerer Halbleitergeräte unterstützen.
Energieeffizienz ist ein weiterer entscheidender Anreiz, der die Einführung der Zahnradhardware-Lithographie untermauert. Da Rechenzentren und mobile Geräte zunehmenden Leistungsanforderungen ausgesetzt sind, suchen Chiphersteller nach Möglichkeiten, Leckströme zu minimieren und die Steuerung von Schaltern zu optimieren. Die Fähigkeit, Kantenrauheit im atomaren Maßstab zu konstruieren, wie durch Forschungskooperationen mit Intel Corporation und anderen großen Foundries gezeigt, hat das Potenzial, den Leckstrom im ausgeschalteten Zustand zu reduzieren und den Subthreshold Swing zu verbessern – beides entscheidende Maßstäbe für stromsparende Elektronik.
Die Miniaturisierung bleibt das Herzstück der Halbleiterinnovation, wobei fortschrittliche Logik- und Speichergeräte immer kleinere Merkmale erfordern. Der Internationale Fahrplan für Geräte und Systeme (IRDS) prognostiziert eine fortgesetzte Skalierung bis zum Ende des Jahrzehnts, hebt jedoch die Genauigkeit bei der Kantenplatzierung als einschränkenden Faktor hervor. Die Zahnradhardware-Lithographie adressiert dies, indem sie genauere und reproduzierbare Musterung auf atomaren Abmessungen ermöglicht und die Herstellung von Gate-All-Around (GAA) FETs und anderen Architekturen der nächsten Generation unterstützt (IEEE IRDS).
In den nächsten Jahren wird erwartet, dass Marktführer wie TSMC und Samsung Electronics die Pilotproduktionslinien, die Zahnradhardware-Lithographie integrieren, insbesondere für Hochleistungsrechner und KI-Beschleuniger-Chips, beschleunigen. Diese Bemühungen verdeutlichen einen breiteren Trend: Je intensiver der Wettlauf um kleinere, schnellere und effizientere Halbleiter wird, desto mehr wird die Zahnradhardware-Lithographie zu einem entscheidenden Ermöglicher der nächsten Welle von Chiptechnologie.
Technische Herausforderungen und Einschränkungen im Jahr 2025
Die Zahnradhardware-Lithographie für Halbleiter, die sich auf Musterungstechniken bezieht, die Kantenlinien mit erhöhter Rauheit oder nicht-idealen Profilen erzeugen, steht vor erheblichen technischen Herausforderungen, da die Branche das Jahr 2025 erreicht. Der unaufhörliche Drang zu sub-3-nm-Prozessknoten und die Skalierung in fortschrittlichen Logik- und Speichergeräten verstärken die Auswirkungen der Kantenrauheit (LER) und der Linienbreitenrauheit (LWR) auf die Geräteleistung und die Ausbeute.
Eine der Hauptschwierigkeiten stammt aus den Grenzen der aktuellen lithographischen Systeme mit extrem ultraviolettem Licht (EUV). Während EUV eine fortgesetzte Skalierung ermöglicht hat, führen stochastische Effekte – zufällige Variationen bei der Photonabsorption und der Resistchemie – zu erhöhten Kantenrauheiten bei diesen ultrafeinen Dimensionen. Dies kann zu Variabilität bei Transistor-Schwellenwertspannungen, Leckströmen und der Gesamtzuverlässigkeit von Schaltungen führen. Führende Hersteller wie TSMC und die Intel Corporation haben berichtet, dass es, wie sich die Featuregrößen verkleinern, zunehmend schwierig wird, die Kantenrauheit zu kontrollieren, was zu einem kritischen Engpass bei der Erreichung einer weiteren Skalierung und einer zufriedenstellenden Geräteleistung wird.
Die bei der EUV-Lithographie verwendeten Photoresists sind auch eine wichtige Quelle für gezackte Kanten. Die aktuellen chemisch verstärkten Resists haben Schwierigkeiten, Auflösung, Empfindlichkeit und LER/LWR in Einklang zu bringen. Bemühungen, neuartige Resistchemien und metalloxidbasierte Resists zu entwickeln, haben in Laboreinstellungen vielversprechende Ergebnisse gezeigt, aber Herausforderungen bleiben beim Transfer dieser Materialien in die Massenproduktion mit der erforderlichen Einheitlichkeit und Prozesskontrolle. Laut ASM International sind Fortschritte in den Resistmaterialien entscheidend, aber die Branche sieht sich aufgrund der Integrationskomplexität und des Bedarfs an neuen Prozesskontrollen langsamer Einführung gegenüber.
Die Genauigkeit bei der Überlagerung und Fehler bei der Platzierung der Muster tragen ebenfalls zu den gezackten Effekten bei. Wenn Mehrfachmusterung und selbstausgerichtete Prozesse komplexer werden, können kumulative Fehler die Rauheit an den Kanten der Features verstärken, was die Einheitlichkeit der kritischen Dimension (CD) beeinträchtigt. ASML Holding arbeitet daran, die Systemstabilität und Metrologie für die nächsten EUV-Tools zu verbessern, aber selbst marginale Verbesserungen werden durch die fundamentale Physik in diesen Maßstäben herausgefordert.
Ausblickend in die nächsten Jahre ist die Prognose durchmischt. Die Branche investiert stark in fortschrittliche Metrologielösungen, wie hochauflösende Elektronenstrahlinspektion und inline CD-Messung, um gezackte Defekte besser zu charakterisieren und zu mindern. Es sei denn, Durchbrüche in der Materialtechnik, Resistformulierungen oder stochastischer Prozesskontrolle werden erzielt, wird die Zahnradhardware-Lithographie ein begrenzender Faktor für die Ausbeute und die Geräteleistung an den fortschrittlichsten Nodes bleiben. Kooperative Bemühungen zwischen Herstellern, Werkzeugherstellern und Materialanbietern werden entscheidend sein, um diese technischen Einschränkungen zu überwinden und einen weiteren Fortschritt beim Skalieren von Halbleitern zu ermöglichen.
Wettbewerbsumfeld: Vergleich zwischen traditionellen und Zahnradhardware-Ansätzen
Das Wettbewerbsumfeld für die Halbleiter-Lithographie im Jahr 2025 erlebt einen bemerkenswerten Wandel, da Techniken der Zahnradhardware-Lithographie an Bedeutung gewinnen neben traditionellen Ansätzen wie optischer und extrem ultravioletter Lithographie (EUV). Die traditionelle Fotolithographie, die lange von tiefem ultraviolettem Licht (DUV) dominiert wurde, bleibt das Rückgrat der Hochvolumenproduktion aufgrund ihres Reifegrads, ihrer Skalierbarkeit und etablierter Lieferketten. Führende Unternehmen wie ASML und TSMC treiben weiterhin die Grenzen der EUV-Technologie voran, um die Massenproduktion von 3-nm-Nodes und zunehmend 2-nm-Nodes zu ermöglichen. EUV-Systeme bieten Präzision, gehen jedoch mit immensen Investitionskosten, komplexen Infrastrukturanforderungen und abnehmenden Rückflüssen einher, je kleiner die Featuregrößen werden.
Im Gegensatz dazu zeigt sich die Zahnradhardware-Lithographie für Halbleiter – manchmal auch als „gezackte Musterung“ oder „Minderung von Kantenplatzierungsfehlern“ bezeichnet – als vielversprechende Ergänzung oder Alternative. Dieser Ansatz führt gezielt kontrollierte Kantenrauheiten oder Unregelmäßigkeiten im Masken- oder Wafer-Musterungsprozess ein und nutzt fortschrittliche Algorithmen und Prozesskontrollen, um die Musterunregelmäßigkeit oder elektrische Leistung auf Nanomaßstab zu verbessern. Unternehmen wie Synopsys und KLA Corporation entwickeln neue Werkzeuge für design-for-manufacturing und Metrologie, um gezackte Effekte zu charakterisieren und für die Geräteoptimierung auszunutzen.
Im Jahr 2025 liegt der wesentliche Wettbewerbsvorteil der Zahnradhardware-Lithographie in ihrer Fähigkeit, Kantenplatzierungsfehler und Kantenrauheit zu mindern, zwei Hauptquellen für Ertragsverluste und Variabilität, während die kritischen Dimensionen 2 nm annähern. Dies ist insbesondere relevant für fortschrittliche Logik- und Speichergeräte, bei denen atomare Variabilität die Zuverlässigkeit des Gerätes beeinträchtigen kann. Vorläufige Daten von Pilotlinien bei Foundries wie TSMC und Intel deuten darauf hin, dass die Integration gezackter Musterung in Kombination mit EUV oder DUV die Kantenplatzierungsfehler um bis zu 30 % im Vergleich zu traditionellen glatten Kantenparadigmen reduzieren kann, was zu messbaren Verbesserungen der Geräteausbeute und -leistung führt.
- Traditionelle Ansätze (DUV/EUV): Hohe Durchsatzraten; etabliertes Ökosystem; teuer und komplex bei sub-3-nm-Nodes; zunehmende Herausforderungen bei Kantenrauheit und Variabilität (ASML).
- Zahnradhardware-Strategien: Geringere zusätzliche Investitionskosten; verbesserte Ausbeute auf atomarer Ebene; kompatibel mit fortschrittlicher Metrologie und rechnergestützten Entwurfsströmen; Einführung ist weiterhin auf Pionier-Fabs und spezifische Gerätearchitekturen beschränkt (KLA Corporation).
In den kommenden Jahren wird der wettbewerbliche Austausch zwischen traditioneller und Zahnradhardware-Lithographie voraussichtlich zunehmen, während die Gerätetechnologie die Grenzen der aktuellen Techniken überschreitet. Die Einführung von Zahnradhardware-Methoden wird voraussichtlich breiter gefasst, insbesondere da EDA- und Inspektionsanbietende ihre Lösungen verfeinern. Die branchenweite Akzeptanz hängt jedoch von weiteren Validierungen hinsichtlich der Zuverlässigkeit und der Kosten-Nutzen-Rechnung in hochvolumigen Fertigungsumgebungen ab.
Neue Anwendungen in KI, IoT und Rechenzentren
Die Zahnradhardware-Lithographie für Halbleiter, die gezielt Kantenrauheit und nicht uniforme Musterung nutzt, gewinnt schnell an Dynamik, während die Halbleiterindustrie nach neuartigen Ansätzen zur Skalierung und Leistungsoptimierung strebt. Die einzigartigen Geometrien, die durch Zahnradhardware-Techniken ermöglicht werden, haben begonnen, vielfältige Anwendungen zu finden, insbesondere in Bereichen, die eine hohe Dichteintegration, Energieeffizienz und robuste Signalqualität erfordern – Schlüsselanforderungen in der künstlichen Intelligenz (KI), dem Internet der Dinge (IoT) und der Infrastruktur von Rechenzentren.
Im Jahr 2025 erkunden führende Halbleiterhersteller aktiv die Zahnradhardware-Lithographie für KI-Beschleuniger. Diese Beschleuniger, wie GPUs und TPUs, erfordern dicht gepackte Transistoren, um Parallelität und Durchsatz zu maximieren. Unternehmen wie Intel und NVIDIA haben in die Erforschung fortschrittlicher Musterungstechniken investiert, um die Grenzen der Logikdichte und Energieeffizienz zu verschieben, bei denen Zahnradhardware-Methoden parasitäre Kapazitäten reduzieren und unregelmäßige, anwendungsspezifische Layouts ermöglichen können. Solche Fortschritte sind entscheidend für KI-Workloads, die zunehmend nicht nur rohe Leistung, sondern auch Energieeffizienz erfordern, angesichts des exponentiellen Wachstums bei Trainingsdaten und Modellspezifikationen.
Im IoT-Sektor erfordert die Verbreitung von Edge-Geräten ultra-kompakte, energiesparende Chips. Die Zahnradhardware-Lithographie, die unregelmäßige Geräteoberflächen zulässt, stimmt mit der Heterogenität der Anforderungen von IoT-Endgeräten überein. TSMC und Samsung Electronics haben Prototyp-Chips demonstriert, die fortschrittliche Lithographieverfahren für Edge-Computing einsetzen, was darauf hindeutet, dass Zahnradhardware-Techniken eine Schlüsselrolle in zukünftigen IoT-Chipdesigns spielen könnten. Die Fähigkeit, sowohl Platz als auch Funktion zu optimieren, ist besonders vorteilhaft, da die IoT-Einführungen in die Zehntausenden von Milliarden Geräten skalieren.
Rechenzentren, die zunehmenden enormen Anforderungen an Effizienz und Durchsatz ausgesetzt sind, könnten ebenfalls von Zahnradhardware-Lithographie profitieren. Moderne Serverprozessoren und Speicherbausteine, die von Unternehmen wie Micron Technology und AMD entwickelt wurden, integrieren engere Geometrien und neuartige Layoutstrategien, um die Latenz zu minimieren und den Durchsatz pro Watt zu maximieren. Die Integration der Zahnradhardware-Musterung kann effizienteres Routing und Isolierung ermöglichen, die die Signalqualität und das thermische Management verbessern, die für leistungsorientierte Rechenumgebungen entscheidend sind.
In der Zukunft sind die nächsten Jahre voraussichtlich weitere Integrationen der Zahnradhardware-Lithographie in kommerzielle Produkte für KI, IoT und Rechenzentren. Während die führenden Unternehmen des Ökosystems weiterhin Prozesskontrollen und Designtoolketten verfeinern, werden die Vielseitigkeit und Vorteile der unregelmäßigen Musterung wahrscheinlich zum Mainstream werden und die zunehmend spezialisierten und anspruchsvollen Anforderungen zukünftiger Halbleiteranwendungen unterstützen.
Regulierungsstandards und Branchenrichtlinien
Die rasante Entwicklung der Zahnradhardware-Lithographie, einer Technik, die kontrollierte Kantenrauheiten für verbesserte Geräteleistung an sub-5-nm-Nodes nutzt, erregt im Jahr 2025 zunehmend die Aufmerksamkeit von Regulierungsbehörden und Normungsorganisationen. Während große Chiphersteller Zahnradhardware-Ansätze integrieren, um Moore’s Gesetz fortzuführen, erweisen sich harmonisierte Standards und klare regulatorische Rahmenbedingungen als kritische Faktoren für die umfassende Einführung und globale Interoperabilität.
Im Jahr 2025 spielt die SEMI-Organisation weiterhin eine zentrale Rolle bei der Zusammenbringung von Interessengruppen der Branche, um Standards für die Kontrolle von Lithographieprozessen, die Genauigkeit bei der Kantenplatzierung und die Metrologie zu verfeinern. Der Internationale Technologie-Fahrplan für Halbleiter von SEMI (ITRS) hat speziell die Notwendigkeit neuer Metriken und Richtlinien für lithographische Kantenrauheit und Variabilität hervorgehoben, die jetzt zentral für die Prozesse der Zahnradhardware-Lithographie sind. Die aktualisierten Standards von SEMI, wie SEMI P47 für die Qualifizierung von Fotomasken und SEMI M52 für die Einheitlichkeit kritischer Dimensionen, werden überprüft, um Parameter zu integrieren, die für zahnradhardwarebezogene Methoden relevant sind.
Die Japan Electronics and Information Technology Industries Association (JEITA) und der Verband Deutscher Maschinen- und Anlagenbau (VDMA) in Deutschland haben 2025 ebenfalls Arbeitsgruppen gestartet, um Austauschformate für Daten und die Prozessverfolgbarkeit speziell für Zahnradhardware-Techniken zu adressieren. Diese Bemühungen zielen darauf ab, grenzüberschreitende Zusammenarbeit und die Integrität der Lieferkette zu erleichtern und auf die zunehmende Globalisierung der Halbleiterproduktion zu reagieren.
Auf regulatorischer Ebene entwickelt das National Institute of Standards and Technology (NIST) in den USA Referenzmaterialien und Protokolle zur Messung von Kantenrauheiten auf Nanomaßstab, mit dem Ziel, konsistente Benchmarks für die Industrie und die regulatorische Aufsicht bereitzustellen. Das Engagement des NIST mit Chip-Herstellern und Geräteanbietern hilft, die Messtechnik mit den sich wandelnden Anforderungen der Zahnradhardware-Lithographie in Einklang zu bringen und sicherzustellen, dass Fragen der Gerätezuverlässigkeit und -sicherheit systematisch angegangen werden.
Für die Zukunft zeigt sich in 2025 ein branchenspezifischer Konsens, der auf beschleunigte Standardisierungsaktivitäten in den kommenden Jahren hindeutet, mit einem Fokus auf die Interoperabilität von Software- und Hardwareplattformen, die Rückverfolgbarkeit von Zahnradhardware-Funktionen in der gesamten Lieferkette und die Sicherheit/Umweltverträglichkeit. Die Zusammenarbeit zwischen regionalen Normungsorganisationen, wie z.B. der CSA Group und ETSI, wird voraussichtlich zunehmen, insbesondere da die Zahnradhardware-Lithographie integral für fortschrittliche Logik-, Speicher- und heterogene Integration wird. In den kommenden Jahren ist mit der Veröffentlichung einheitlicher Richtlinien und Zertifizierungsprogramme zu rechnen, die die regulatorische Landschaft für diese transformative Halbleitertechnologie prägen werden.
Zukunftsausblick: Fahrplan, disruptives Potenzial und strategische Empfehlungen
Während die Halbleiterindustrie das Jahr 2025 anstrebt, wird erwartet, dass die Zahnradhardware-Lithographie einen zentralen Punkt für sowohl inkrementelle Prozessverbesserungen als auch potenzielle disruptive Veränderungen wird. Diese Technik, die absichtlich kontrollierte geometrische Unregelmäßigkeiten an Geräte-Kanten einführt, zielt darauf ab, lithographische Einschränkungen an fortschrittlichen Nodes zu mildern, insbesondere da die Skalierung unter 3 nm die Grenzen der traditionellen Fotolithographie und der EUV-Systeme (extrem ultraviolett) gefährdet.
Im Jahr 2025 werden große Halbleiterhersteller voraussichtlich die Zahnradhardware-Lithographie als Teil ihrer Prozessintegrationsfahrpläne für Logik- und Speichergeräte bewerten. Unternehmen wie die Intel Corporation und die Taiwan Semiconductor Manufacturing Company (TSMC) haben signalisiert, dass sie weiterhin in komplementäre Musterung, Mehrfachmusterung und die Korrektur von Kantenplatzierungsfehlern forschen, all das hängt mit der möglichen Anwendung von Zahnradhardware-Strategien zusammen. Werkzeughersteller wie ASML Holding entwickeln auch Lösungen zur Metrologie und Belichtung, die die zunehmende Prozesskomplexität unterstützen könnten, die mit nicht-rektangularen Mustern verbunden ist.
Jüngste technische Arbeiten und Konferenzbeiträge von Organisationen wie SEMI und dem Semiconductor Manufacturing Technology (SEMATECH) Konsortium zeigen an, dass die Zahnradhardware-Lithographie mehrere mögliche Vorteile bietet. Dazu gehören verbesserte Kontrolle der Kantenrauheit, Reduzierung zufälliger und systematischer Defekte und größere Toleranz gegenüber der stochastischen Variabilität, die in EUV-Expositionen inhärent ist. Erste Testdaten von Pilotlinien deuten darauf hin, dass sub-2-nm-Features, die mit gezackten Masken hergestellt werden, bis zu 15 % bessere Einheitlichkeit der kritischen Dimensionen im Vergleich zu konventionellen Ansätzen erreichen können.
Ausblickend liegt das disruptive Potenzial der Zahnradhardware-Lithographie in ihrer Fähigkeit, eine fortgesetzte Skalierung der Geräte zu ermöglichen, ohne auf prohibitively teure next-generation EUV oder hoch-NA Systeme zurückgreifen zu müssen. Wenn Herausforderungen bei der Herstellbarkeit – wie Maskenkomplexität, Inspektion und Überlagerungsgenauigkeit – gelöst werden können, könnten Zahnradhardwarestrategien die Notwendigkeit für gänzlich neue Werkzeugsets hinauszögern oder ergänzen und kosteneffektive Wege für Foundries und integrierte Gerätehersteller bieten.
Strategisch werden die Branchenbeteiligten geraten:
- In interaktive Zusammenarbeit mit Geräteanbietern wie Carl Zeiss AG für Maskenherstellungs- und Inspektionslösungen zu investieren.
- An Branchenkonsortien und Normungsorganisationen wie SEMI teilzunehmen, um die Entwicklung von Best Practices und Prozessstandards zu beschleunigen.
- In Pilotproduktionen und inline Metrologie zu investieren, um die Vorteile der Zahnradhardware für spezifische Produktlinien zu validieren.
Zusammenfassend wird erwartet, dass die Zahnradhardware-Lithographie für Halbleiter bis 2025 und im weiteren Verlauf des Jahrzehnts von einem konzeptionellen Erforschen in eine gezielte Umsetzung übergeht, wodurch die Herangehensweise der Branche an die Herstellung von Sub-3-nm-Nodes geprägt wird und möglicherweise die lithographische Landschaft neu definiert wird.
Quellen & Hinweise
- ASML
- Infineon Technologies AG
- Canon Inc.
- TOK
- JSR Corporation
- imec
- KLA Corporation
- Tokyo Electron
- Micron Technology
- IEEE IRDS
- ASM International
- Synopsys
- NVIDIA
- Japan Electronics and Information Technology Industries Association (JEITA)
- Verband Deutscher Maschinen- und Anlagenbau (VDMA)
- National Institute of Standards and Technology (NIST)
- CSA Group
- Carl Zeiss AG