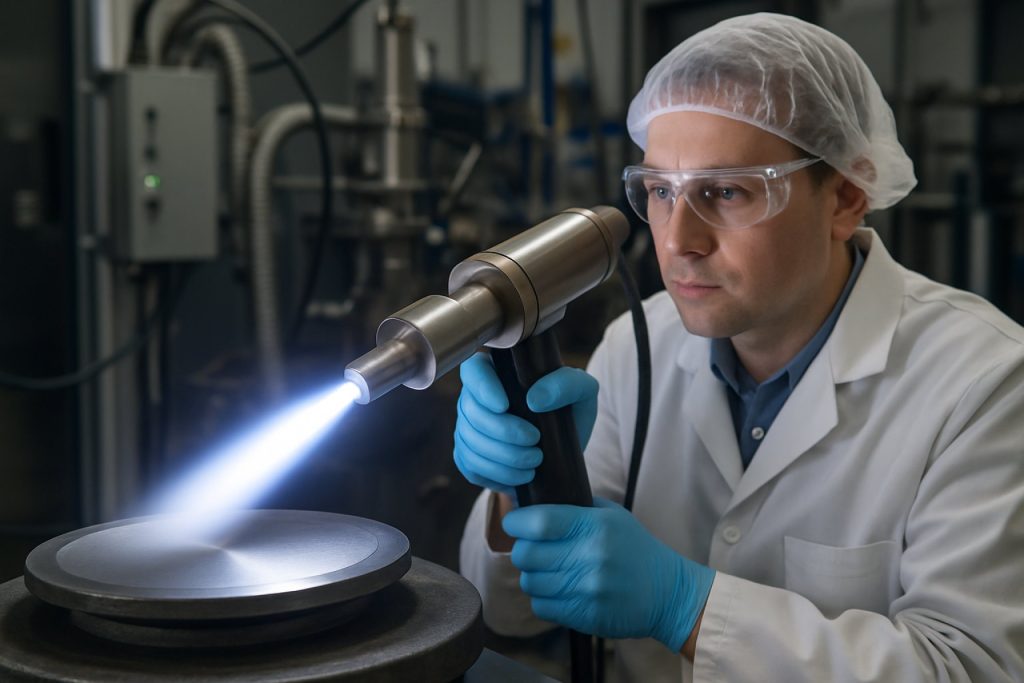
Table of Contents
- Executive Summary: Market Shifts and Key Drivers Through 2030
- Plasma Deposition Coating Technologies Explained: Fundamentals and Methods
- 2025 Market Size & Growth Forecast: Global and Regional Insights
- Emerging Innovations: Next-Gen Materials and Processes
- Competitive Landscape: Leading Companies & Strategic Initiatives
- Industry Applications: Electronics, Aerospace, Automotive, and Beyond
- Sustainability and Environmental Impact: Regulatory Trends and Green Solutions
- Investment Outlook: Funding, M&A, and Partnership Activities
- Challenges and Barriers: Technical, Supply Chain, and Adoption Hurdles
- Future Outlook: Expert Predictions for Plasma Deposition Coatings to 2030
- Sources & References
Executive Summary: Market Shifts and Key Drivers Through 2030
Plasma deposition coating technologies are experiencing accelerated adoption across a spectrum of industries as manufacturers seek advanced solutions for surface modification, wear resistance, and functional coatings. In 2025, the sector is witnessing a distinct shift driven by intensified demand from the automotive, aerospace, electronics, and medical device industries, each prioritizing enhanced material performance and sustainability. Leading companies are scaling up investments in plasma-enhanced chemical vapor deposition (PECVD), plasma-assisted physical vapor deposition (PVD), and atmospheric plasma spray techniques to meet evolving application needs.
Major automotive OEMs and component suppliers are leveraging plasma processes to deposit hard, low-friction, and corrosion-resistant coatings on engine parts, gears, and e-mobility components. For example, Dr. Hönle AG and Oerlikon are expanding their plasma technology portfolios to address demands for both functional and decorative coatings, with a focus on reducing environmental impact compared to traditional electroplating.
Aerospace manufacturers are increasingly integrating plasma coatings for turbine blades, landing gear, and critical airframe structures, citing their ability to withstand extreme temperatures and erosive environments. Howmet Aerospace and Bodycote are advancing plasma-based technologies to support next-generation aircraft and propulsion systems. Meanwhile, the electronics industry is accelerating the deployment of plasma deposition for thin-film transistors, display panels, and semiconductor wafers, enabled by enhanced process control and scalability from solution providers like ULVAC.
Medical devices present another robust growth avenue through 2030, with plasma coatings enabling improved biocompatibility, antimicrobial functionality, and controlled drug release. Companies such as Bühler Group (Balzers) are collaborating with implant and instrument manufacturers to deliver advanced plasma surface engineering solutions that meet stringent regulatory and performance standards.
Key drivers underpinning these market shifts include tightening environmental regulations, the push for longer product lifespans, and the need for higher efficiency in manufacturing processes. Plasma deposition’s relatively low waste generation and minimal use of hazardous chemicals position it as a sustainable alternative to legacy coating methods. Over the next few years, ongoing advancements in plasma source design, automation, and in-line process monitoring are expected to further reduce costs, improve coating uniformity, and expand the range of treatable substrates.
Collectively, these trends indicate that plasma deposition coating technologies will play an increasingly central role in materials engineering strategies across multiple industries, with significant commercial and technical momentum anticipated through 2030.
Plasma Deposition Coating Technologies Explained: Fundamentals and Methods
Plasma deposition coating technologies are a set of advanced processes that utilize plasma—a partially ionized gas with unique energetic properties—to deposit thin films and functional coatings onto a wide range of substrates. These methods are fundamental to industries including semiconductor manufacturing, aerospace, automotive, biomedical devices, and renewable energy. The two most prominent categories are Physical Vapor Deposition (PVD) and Chemical Vapor Deposition (CVD), both of which have evolved significantly and remain at the forefront of materials engineering in 2025.
In PVD processes, plasma is generated by applying electrical energy to a gas (often argon) in a vacuum chamber, energizing the gas into a plasma state. The plasma then facilitates the vaporization and subsequent deposition of materials such as metals, nitrides, and oxides onto substrates. Common techniques within PVD include sputtering and evaporation. For example, Oxford Instruments and Advanced Energy Industries are two industry leaders supplying PVD systems and plasma power solutions utilized in both research and high-throughput manufacturing.
CVD techniques, by contrast, use plasma to enhance chemical reactions of vapor-phase precursors, enabling the formation of conformal, high-purity coatings even on complex geometries. Plasma-Enhanced CVD (PECVD) is particularly valued for applications in solar photovoltaics and microelectronics, with companies such as Applied Materials and ULVAC providing state-of-the-art PECVD systems worldwide.
The fundamentals of plasma deposition technologies rest on precise control of plasma parameters (such as energy, pressure, and gas composition), substrate temperature, and deposition rates. This allows for atomic-scale engineering of coating properties—thickness, adhesion, hardness, optical characteristics, and chemical functionality—which is crucial as industries demand ever-improving performance and miniaturization.
- PVD is prized for producing hard, wear-resistant coatings (e.g., TiN, AlTiN) in cutting tools and medical implants.
- PECVD enables the deposition of dielectric films and barrier layers for advanced semiconductor nodes and flexible electronics.
- Atmospheric-pressure plasma processes are emerging for rapid, large-area treatments, notably in packaging and automotive sectors.
Looking into 2025 and beyond, plasma deposition continues to expand through innovations such as high-power impulse magnetron sputtering (HiPIMS), atomic layer deposition (ALD) enhancements, and environmentally friendly precursor chemistries. The sector is also responding to the push for greener, energy-efficient manufacturing processes and integration with Industry 4.0 automation. With leading manufacturers and technology providers actively advancing plasma deposition methods, these technologies are expected to remain essential for next-generation product development and scalable surface engineering solutions (Oxford Instruments, Applied Materials).
2025 Market Size & Growth Forecast: Global and Regional Insights
The plasma deposition coating technologies sector is set for notable expansion in 2025, driven by surging demand from critical industries such as semiconductors, aerospace, automotive, and renewable energy. Plasma-enhanced chemical vapor deposition (PECVD), plasma spray, and physical vapor deposition (PVD) are among the principal methods seeing accelerated adoption due to their capacity to deliver highly uniform, adherent, and durable coatings at scale. This technology suite is increasingly favored for applications requiring enhanced wear resistance, corrosion protection, and advanced functional surfaces.
In 2025, global revenues for plasma deposition coatings are projected to exceed several billion USD, with particularly strong growth in Asia-Pacific, propelled by the region’s robust semiconductor manufacturing and electronics sectors. Major regional players—including ULVAC (Japan), Shincron (Japan), and Otsuka Electronics (Japan)—are increasing investments in new plasma processing equipment, highlighting the sector’s momentum. The European market remains active, with companies like Oerlikon advancing plasma-based surface solutions for automotive and aerospace OEMs.
North America continues to play a pivotal role, buoyed by ongoing investments in advanced manufacturing and the rapid expansion of electric vehicle (EV) and battery production, where plasma coatings are critical for improving component reliability. Leading suppliers in the region, such as Entegris and Advanced Coating, are scaling up to meet demand for high-performance plasma deposition systems and consumables.
Technological innovation remains robust, with companies prioritizing higher throughput, greater process control, and sustainability. Plasma deposition processes are being optimized for lower energy consumption and reduced emissions, aligning with global decarbonization efforts. For instance, Oerlikon is piloting new plasma-based coating lines that significantly decrease environmental impact while maintaining performance.
Looking ahead, the market outlook for plasma deposition coating technologies is positive. Continued semiconductor miniaturization, the shift to electric mobility, and the integration of advanced coatings into clean energy infrastructure are set to drive sustained demand. Strategic collaborations between end-users and equipment manufacturers are expected to foster further innovation and capacity growth over the next few years, ensuring plasma deposition remains a cornerstone of advanced manufacturing worldwide.
Emerging Innovations: Next-Gen Materials and Processes
Plasma deposition coating technologies are witnessing significant advancements as industries seek higher performance, sustainability, and versatility in surface engineering. In 2025 and the coming years, the focus is intensifying on next-generation materials and process innovations, driven by demand from automotive, aerospace, electronics, and medical device sectors. These innovations are characterized by the development of advanced plasma-enhanced chemical vapor deposition (PECVD) and physical vapor deposition (PVD) processes, which enable the creation of ultra-thin, conformal, and multifunctional coatings with tailored properties.
A key trend is the integration of nanostructured and multi-layer coatings, enhancing properties such as hardness, corrosion resistance, and biocompatibility. Companies like Oxford Instruments and PLASMA TECHNOLOGY are actively expanding their portfolios to include atomic layer deposition (ALD) and hybrid plasma systems. These systems support the deposition of complex materials, such as transition metal nitrides and oxides, which are critical for next-generation microelectronics, cutting tools, and protective components.
Process innovations are also focusing on improved energy efficiency and reduced environmental impact. For example, advancements in pulsed plasma systems and low-temperature deposition methods are enabling the treatment of heat-sensitive substrates and reducing the carbon footprint of manufacturing. Oerlikon Balzers has introduced new PVD processes that significantly cut hazardous emissions while delivering enhanced coating performance for the automotive and tooling industries.
Emerging applications are driving further customization of plasma coatings. In the biomedical field, plasma-deposited diamond-like carbon (DLC) and antibacterial coatings are gaining traction for implants and surgical instruments, offering improved wear resistance and biocompatibility. Surface Technology and IHI Ionbond are developing proprietary coatings tailored to medical and high-precision applications, leveraging plasma processes for superior surface properties.
Looking ahead, digitalization and process monitoring are expected to play a pivotal role. Real-time plasma diagnostics and AI-driven process control are being integrated to ensure coating uniformity and reproducibility, supporting the scale-up of advanced plasma technologies. With continued investment in R&D and collaboration between equipment manufacturers and end-users, plasma deposition coating technologies are poised to deliver transformative benefits across multiple industries by 2025 and beyond.
Competitive Landscape: Leading Companies & Strategic Initiatives
The competitive landscape for plasma deposition coating technologies is marked by robust activity among leading manufacturers and technology providers as demand intensifies across sectors such as semiconductors, automotive, aerospace, and medical devices. As of 2025, major players are accelerating investments in research, expanding global footprints, and forging strategic partnerships to address evolving customer needs for high-performance coatings.
Key industry leaders include Oxford Instruments, ULVAC, Plassys Bestek, PVD Products, and Oerlikon, each offering advanced plasma-enhanced chemical vapor deposition (PECVD), physical vapor deposition (PVD), and related coating solutions. These firms consistently introduce new reactor designs, source technologies, and process control systems to improve coating uniformity, energy efficiency, and throughput. For example, Oerlikon has been expanding its surface solutions division with next-generation PVD and PACVD (plasma-assisted chemical vapor deposition) technologies for applications ranging from cutting tools to medical implants. Meanwhile, ULVAC continues to invest in scalable PECVD systems for semiconductor and display manufacturing, targeting higher deposition rates and lower cost per wafer.
Strategic collaborations are also shaping the landscape. In recent years, major equipment suppliers have partnered with materials companies and end-users to accelerate the commercialization of application-specific coatings. For example, Oxford Instruments has engaged in joint projects with leading research institutes and industrial customers to optimize atomic layer deposition (ALD) and plasma processes for next-generation electronics and photonics. Furthermore, PVD Products has expanded its custom system offerings, working closely with universities and R&D labs to tailor plasma deposition solutions for advanced materials research.
Mergers, acquisitions, and facility expansions continue to play a pivotal role. Companies such as Oerlikon and ULVAC are investing in new manufacturing centers and service hubs, particularly in Asia Pacific and North America, to capitalize on growing regional demand. This expansion supports faster delivery, localized support, and enhanced customer engagement.
Looking ahead to the next few years, ongoing innovation in plasma source technology, digital process monitoring, and environmentally friendly coating chemistries is expected to intensify competition. As sustainability and miniaturization gain importance, the sector will likely see further partnerships and technology transfers, reinforcing the leadership of established firms while creating opportunities for agile new entrants.
Industry Applications: Electronics, Aerospace, Automotive, and Beyond
Plasma deposition coating technologies have become increasingly pivotal across several high-value industries, notably electronics, aerospace, and automotive, due to their ability to engineer surfaces with tailored properties such as hardness, corrosion resistance, and electrical conductivity. As of 2025, the adoption of plasma-enhanced chemical vapor deposition (PECVD), physical vapor deposition (PVD), and related plasma-based methods continues to accelerate, driven by the pursuit of higher efficiency, reliability, and miniaturization.
In the electronics sector, plasma coatings provide thin, uniform films essential for semiconductor device fabrication, display technology, and advanced packaging. Leading manufacturers such as Applied Materials and Lam Research are investing in next-generation plasma deposition equipment that supports sub-5 nm feature sizes and 3D device architectures, addressing the ongoing demand for increased transistor density and energy efficiency. Additionally, the growing adoption of flexible and wearable electronics is fueling new plasma-based solutions for low-temperature processing on polymer substrates.
The aerospace industry relies on plasma coatings for both performance and durability. Advanced ceramic and metallic plasma-sprayed coatings protect turbines, engine components, and airframes from extreme thermal and oxidative environments. Companies like GE Aerospace and Oerlikon are expanding their use of thermal barrier coatings and erosion-resistant films, leveraging plasma deposition to extend component lifespans and reduce maintenance cycles. The push for next-generation aircraft and space vehicles is expected to further drive innovation in multi-layered and multifunctional plasma coatings through 2025 and beyond.
In automotive manufacturing, plasma deposition is increasingly utilized for hard, low-friction, and decorative coatings on engine parts, gears, and trim. Höganäs and Dürr are among the companies developing plasma-based surface solutions for e-mobility applications, including coatings for battery contacts and fuel cells. The electrification of vehicles and the demand for higher wear resistance are expected to intensify plasma technology adoption in this sector.
Beyond these sectors, plasma deposition is gaining ground in medical devices, optics, and renewable energy. Biocompatible plasma coatings are increasingly employed in implants and surgical tools, while anti-reflective and self-cleaning surfaces are becoming standard in solar panels and architectural glass. The outlook for 2025 and the ensuing years is one of continued expansion, propelled by advances in process control, eco-friendly chemistries, and digital integration, as industry leaders continue to scale up and diversify plasma coating solutions for evolving application demands.
Sustainability and Environmental Impact: Regulatory Trends and Green Solutions
Plasma deposition coating technologies are experiencing a pivotal transformation in 2025, as sustainability and regulatory compliance become central to industry strategies. Traditional coating processes, such as chemical vapor deposition (CVD) and physical vapor deposition (PVD), have historically faced scrutiny for energy intensity, hazardous precursor use, and waste generation. Today, plasma-enhanced variants are increasingly recognized for their potential to minimize environmental impact while maintaining high-performance standards.
A major driver of this shift is the tightening of global environmental regulations. In Europe, the 2024 updates to the REACH regulation and the EU Green Deal continue to push manufacturers toward coatings with minimal volatile organic compounds (VOCs) and reduced hazardous substance usage. The U.S. Environmental Protection Agency (EPA) is also increasing oversight on industrial emissions, specifically targeting solvents and heavy metals used in conventional coating processes. These pressures have led to an accelerated adoption of plasma deposition coatings, which can function at lower temperatures and with reduced chemical inputs, making them inherently cleaner and more energy-efficient.
Recent developments by leading industry players underscore the momentum. IHI Ionbond and Hauzer Techno Coating have unveiled new plasma-assisted PVD and PACVD systems optimized for low-carbon operations and designed to comply with both current and anticipated environmental standards. These systems are engineered to enable water-based cleaning, reduce waste streams, and cut power consumption by up to 30% compared to legacy equipment. Meanwhile, Platit AG is scaling up its deployment of multi-arc and sputtering plasma coaters that eliminate the need for toxic process gases, further supporting the industry’s shift towards green manufacturing.
In parallel, the sector is witnessing a surge in demand from automotive, aerospace, and medical device manufacturers seeking eco-friendly surface engineering solutions. Plasma coatings now offer viable alternatives to hard chrome and other legacy treatments restricted by new regulations. For instance, IHI Ionbond reports a steady increase in requests for tribological and corrosion-resistant coatings that meet both functional and environmental criteria, reflecting broader industry trends.
Looking forward, the market outlook remains robust, with rapid innovation expected in plasma source efficiency, precursor recycling, and renewable energy integration. Industry associations anticipate that, by 2027, plasma deposition technologies will set new benchmarks for sustainable coatings, aided by continued regulatory alignment and collaboration between equipment suppliers and end users. As a result, plasma deposition is poised to become a cornerstone of green manufacturing across advanced sectors.
Investment Outlook: Funding, M&A, and Partnership Activities
The investment landscape for plasma deposition coating technologies in 2025 is poised for robust activity, driven by advancements in semiconductor manufacturing, green energy solutions, and high-performance engineering materials. Capital inflows are being observed both from established sector leaders and emerging players, with notable funds directed at scaling production capabilities, expanding global footprints, and accelerating R&D for next-generation applications.
In recent years leading up to 2025, there has been a discernible uptick in merger and acquisition (M&A) activity aimed at consolidating market positions and integrating complementary technologies. For instance, Oxford Instruments, a major supplier of plasma deposition and etching systems, has been actively expanding its portfolio through targeted acquisitions, seeking to broaden its reach in the semiconductor and advanced materials markets. Similarly, ULVAC, Inc. continues to invest in partnerships and joint ventures to strengthen its plasma technology offerings across Asia and North America.
Strategic partnerships are also playing a pivotal role in shaping the sector’s outlook. For example, Plasma Technology GmbH (a brand of PINK GmbH Thermosysteme) has entered into collaborations with leading automotive and electronics manufacturers to develop tailored plasma deposition solutions that address evolving demands for durability and energy efficiency. These alliances are critical for the rapid prototyping and commercialization of advanced coatings, such as those enabling enhanced battery electrodes and corrosion resistance.
From a funding perspective, government-supported initiatives and private capital are converging to support innovation hubs and pilot production lines. Several industry players, including AIT Austrian Institute of Technology, are beneficiaries of public-private funding schemes across the European Union, designed to accelerate the adoption of plasma-based surface technologies within climate-relevant sectors.
Looking forward into the next few years, the appetite for investment is expected to remain high, particularly as sectors like aerospace, medical devices, and renewable energy amplify their reliance on plasma deposition for performance-critical components. Continued M&A activity is likely, especially as companies seek to secure proprietary technologies and access to specialized talent. The focus on sustainability and the circular economy will further catalyze both funding and partnership endeavors, ensuring plasma deposition coatings remain at the forefront of advanced manufacturing innovation.
Challenges and Barriers: Technical, Supply Chain, and Adoption Hurdles
Plasma deposition coating technologies, encompassing processes such as plasma-enhanced chemical vapor deposition (PECVD) and physical vapor deposition (PVD), are integral to the production of advanced components in industries ranging from semiconductors to automotive and aerospace. However, as demand intensifies in 2025 and the subsequent years, several key challenges and barriers are shaping the sector’s trajectory.
A significant technical hurdle is the ongoing demand for higher coating quality, uniformity, and process reproducibility, especially as device features shrink and substrate complexity increases. Many manufacturers are now required to deposit ultra-thin, defect-free films at scale, which pushes the limits of existing plasma sources and process control technologies. Issues such as target poisoning, arcing, and plasma instabilities can lead to inconsistent coatings or equipment downtime. Leading equipment suppliers like Lam Research and Applied Materials are investing in new plasma source designs and advanced real-time monitoring systems to address these challenges, but industrial-scale deployment remains a work in progress.
Supply chain vulnerabilities also pose a notable barrier. Plasma deposition equipment relies on a global network of suppliers for specialty gases, high-purity target materials, and precision components. Disruptions—from geopolitical tensions affecting rare metal supply to logistical delays in specialty gas shipments—can stall production schedules. For example, the semiconductor sector’s ongoing sensitivity to supply chain shocks was underscored by the COVID-19 pandemic’s aftermath and remains a concern for 2025. Companies such as Oxford Instruments and Entegris are actively working to diversify their supplier base and implement risk management strategies, but the high specificity of inputs limits flexibility.
Adoption hurdles persist, particularly for smaller manufacturers and those in cost-sensitive sectors. Plasma deposition systems require substantial capital investment, rigorous cleanroom environments, and skilled operators. This limits uptake in regions with less developed infrastructure or where return on investment is less immediate. Additionally, integrating new plasma-based coatings into existing product lines can necessitate extensive qualification and regulatory approval, extending time-to-market. Organizations such as Carl Zeiss and Safran continue to pilot collaborative programs aimed at knowledge transfer and workforce training, but broad-based adoption remains gradual.
Looking ahead, while plasma deposition technologies are poised for continued innovation, the interplay of technical, supply chain, and adoption-related barriers suggests a measured pace of expansion through the remainder of the decade. Addressing these challenges will be critical to realizing the full potential of plasma coatings across diverse high-tech applications.
Future Outlook: Expert Predictions for Plasma Deposition Coatings to 2030
Plasma deposition coating technologies are positioned for robust growth and technical evolution through 2030, driven by demand in semiconductor fabrication, automotive, aerospace, and biomedical sectors. In 2025, the continued miniaturization of electronic components is intensifying requirements for ultra-thin, uniform, and defect-free films—demands that plasma-enhanced chemical vapor deposition (PECVD) and physical vapor deposition (PVD) methods are uniquely equipped to address. Industry leaders such as Applied Materials and ULVAC are actively scaling up next-generation plasma platforms for atomic layer deposition (ALD) and high-rate, low-temperature coatings, targeting both silicon and emerging compound semiconductors.
Recent technical milestones include the development of plasma deposition systems capable of handling larger substrates with tighter process control, which is crucial for display manufacturing and advanced packaging. Oxford Instruments has showcased innovations in plasma etch and deposition toolsets designed for rapid process switching and multilayer stack fabrication, catering to the evolving needs of microLED and advanced logic device manufacturers.
Sustainability is emerging as a key theme for the next few years. Plasma processes inherently reduce the use of hazardous chemicals compared to wet-chemical techniques, and companies such as SINGULUS TECHNOLOGIES are promoting plasma-based vacuum coating solutions for solar cells and functional coatings, emphasizing energy efficiency and recyclability. By 2030, it is expected that plasma deposition will further align with green manufacturing initiatives, particularly as governments and end-users demand lower environmental footprints.
The adoption of plasma coatings in automotive and aerospace is also anticipated to accelerate. Enhanced wear resistance, corrosion protection, and thermal barrier properties are critical for electric vehicles and next-generation turbines. OCSiAl and Hauzer Techno Coating are both expanding their portfolios to include plasma-applied nanocoatings and advanced tribological layers, aiming to extend component lifetimes and improve energy efficiency.
Looking ahead to 2030, experts predict that digitalization and AI-driven process control will be increasingly integrated into plasma deposition systems, further improving yield and material utilization. The convergence of plasma deposition with additive manufacturing and advanced materials, such as 2D materials and functional polymers, is also expected to unlock new application domains. As the market grows, collaboration between equipment manufacturers, materials suppliers, and end-users will play a pivotal role in shaping the future landscape of plasma deposition coating technologies.
Sources & References
- Dr. Hönle AG
- Oerlikon
- Howmet Aerospace
- ULVAC
- Oxford Instruments
- Advanced Energy Industries
- Shincron
- Otsuka Electronics
- Entegris
- Advanced Coating
- PLASMA TECHNOLOGY
- Surface Technology
- Plassys Bestek
- PVD Products
- GE Aerospace
- Dürr
- Hauzer Techno Coating
- Platit AG
- Oxford Instruments
- PINK GmbH Thermosysteme
- AIT Austrian Institute of Technology
- Carl Zeiss
- SINGULUS TECHNOLOGIES
- OCSiAl