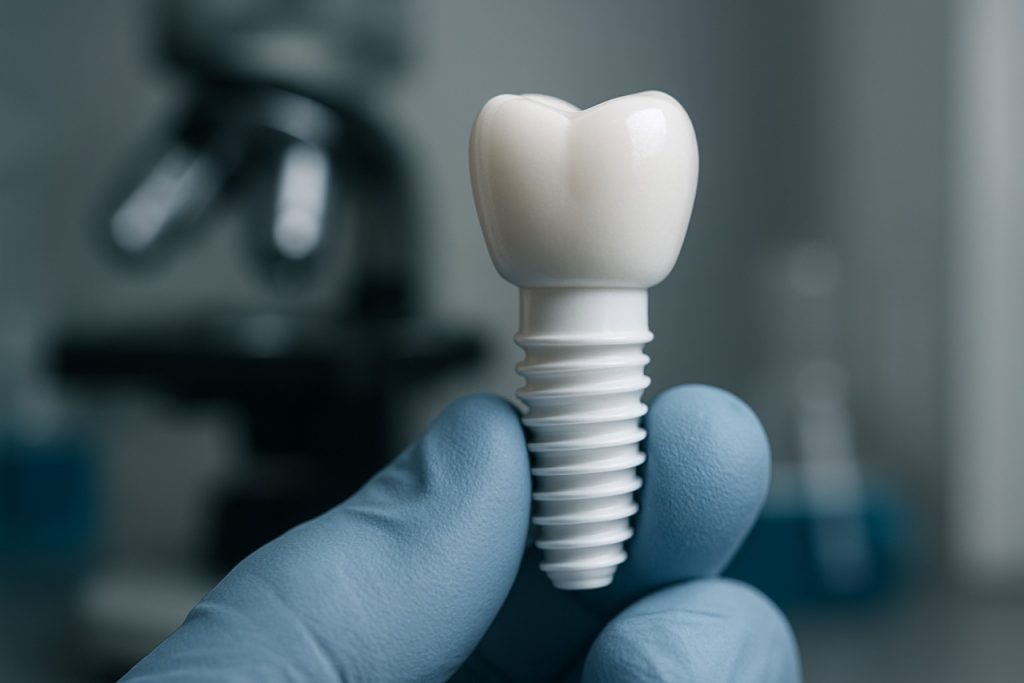
Table of Contents
- Executive Summary: The State of Ceramic Matrix Composite Implants in 2025
- Market Size & Forecast: Projections Through 2030
- Key Players & Strategic Partnerships (e.g., ge.com, siemens.com, sglcarbon.com)
- Breakthrough Technologies Shaping Implant Manufacturing
- Regulatory Landscape & Approval Pathways (e.g., fda.gov, ema.europa.eu)
- Supply Chain Innovations and Challenges
- Clinical Performance and Safety Data
- Competitive Analysis: Traditional vs. Composite Implants
- Emerging Applications Beyond Orthopedics
- Future Outlook: Investment, R&D Hotspots, and Next-Gen Materials
- Sources & References
Executive Summary: The State of Ceramic Matrix Composite Implants in 2025
Ceramic matrix composite (CMC) implant manufacturing in 2025 is characterized by rapid advancements in materials engineering, scalable production processes, and a growing acceptance in orthopedic and dental applications. Driven by the demand for lightweight, high-strength, and biocompatible alternatives to traditional metallic implants, manufacturers are leveraging innovations in fiber reinforcement, additive manufacturing, and surface functionalization to improve implant performance and longevity.
In 2025, leading medical device and advanced ceramics companies are investing heavily in refining CMC processing. For example, Kyocera Corporation continues to expand its ceramic implant portfolio by integrating novel silicon nitride and alumina matrix composites, which offer superior wear resistance and osteointegration compared to legacy materials. Similarly, CeramTec is advancing the development of composite-based hip and knee joint components, focusing on improving mechanical reliability while reducing the risk of adverse biological reactions.
Manufacturing techniques are shifting toward more automated and precise methods. Companies such as CoorsTek are utilizing advanced slip casting, isostatic pressing, and CNC machining to achieve consistent microstructures and tight tolerances necessary for load-bearing implants. Furthermore, the adoption of additive manufacturing (AM) is gaining traction for patient-specific implants and rapid prototyping. 3D Systems is actively collaborating with medical OEMs to develop AM processes for CMCs, aiming to streamline the transition from design to finished implant.
One of the most significant trends in 2025 is the integration of hybrid composites, where ceramic matrices are reinforced with carbon or polymer fibers to enhance toughness and tailor mechanical properties. Sage Metals and others are piloting these next-generation CMCs for trauma fixation and spinal fusion devices, citing early clinical feedback on improved implant stability.
The outlook for the next few years remains optimistic, with regulatory pathways becoming clearer as more clinical evidence supports the safety and efficacy of CMC implants. Strategic partnerships between materials suppliers and medical device companies are expected to accelerate commercialization. As manufacturing scalability improves and costs decrease, CMC implants are poised to capture a larger share of the orthopedic and dental markets, particularly for younger and more active patient populations seeking durable, metal-free solutions.
Market Size & Forecast: Projections Through 2030
The market for ceramic matrix composite (CMC) implant manufacturing is poised for significant growth through 2030, driven by ongoing advancements in materials science, increasing demand for high-performance biomedical implants, and a steady expansion of regulatory approvals worldwide. As of 2025, industry leaders are reporting notable acceleration in both research and commercialization of CMC-based implant solutions, particularly in orthopedic and dental applications.
Major manufacturers have ramped up investments in production capacity and R&D. For example, CoorsTek, a prominent advanced ceramics supplier, continues to expand its biomedical ceramics capabilities, citing increased customer demand for next-generation implantable materials. Similarly, CeramTec has highlighted the growth in their medical products segment, with their BIOLOX® ceramic components now being used in millions of hip replacement procedures globally.
Industry data from 2025 indicates that the global CMC implant market is expected to maintain a compound annual growth rate (CAGR) in the high single digits through the end of the decade, with orthopedic, dental, and spinal implants representing the largest segments. The expansion is underpinned by the superior wear resistance, biocompatibility, and imaging advantages offered by CMCs compared to traditional metal-based implants. For instance, Kyocera Corporation has reported steady growth in their medical device division, citing rising adoption of ceramic-based spinal and dental implants in Asia, Europe, and North America.
- CeramTec reports ongoing partnerships with medical device manufacturers to co-develop CMC-based innovations, with several new product launches anticipated by 2027.
- CoorsTek has invested in new manufacturing lines as of 2024, aiming to double their advanced ceramics output for medical applications by 2026.
- Kyocera Corporation forecasts continued double-digit revenue growth in their health care division through 2028, driven by international expansion and regulatory clearances.
Looking ahead, market outlook remains robust as regulatory agencies in the US, EU, and Asia streamline approval pathways for ceramic matrix composite implants. The convergence of technological innovation, clinical evidence, and expanding patient populations suggests the CMC implant manufacturing sector will play a critical role in the evolution of high-performance medical devices through 2030 and beyond.
Key Players & Strategic Partnerships (e.g., ge.com, siemens.com, sglcarbon.com)
The landscape of ceramic matrix composite (CMC) implant manufacturing in 2025 is marked by the active involvement of several industrial leaders and a growing web of strategic partnerships. These collaborations are driven by the need for advanced biomaterials in orthopedic, dental, and spinal implants, where CMCs offer superior mechanical and biological properties over conventional materials. As demand escalates for high-performance medical implants, key players from aerospace and advanced ceramics are increasingly leveraging their technological expertise for biomedical applications.
- General Electric Company (GE) has historically pioneered CMC development for aerospace and energy, and in recent years has been adapting its CMC processing capabilities—such as advanced fiber architecture and infiltration techniques—to biomedical applications. Through its division GE Research, the company is exploring medical-grade CMCs for load-bearing implants, emphasizing biocompatibility and tailored porosity. GE’s collaborations with universities and medical device companies are expected to yield new implant prototypes within the next few years.
- Siemens AG, renowned for its digital manufacturing and healthcare solutions, is facilitating the integration of additive manufacturing (AM) with CMC implant production. The Siemens Healthineers division is working on digital workflow platforms that enable precision design and quality assurance for custom CMC implants. Strategic alliances with bioceramic producers and AM technology providers are accelerating Siemens’ entry into personalized implant manufacturing, with pilot projects anticipated to reach clinical evaluation by 2026.
- SGL Carbon SE stands out as a global leader in carbon and ceramic composites. With significant investments in medical-grade CMC development, SGL Carbon is collaborating with implant manufacturers to refine silicon carbide and oxide-based CMCs for orthopedic and dental applications. In 2025, SGL Carbon is expanding its technical center capacity to support co-development projects focused on next-generation bioinert and bioactive implant materials.
- CoorsTek, Inc. is leveraging its extensive experience in technical ceramics to supply pre-forms and semi-finished CMC components to the medical device sector. CoorsTek is actively partnering with device OEMs to optimize CMC microstructures for both mechanical integrity and osseointegration. Several joint development agreements initiated in 2024 are expected to yield commercial implant components by 2027.
Looking ahead, further strategic partnerships are expected as regulatory pathways for CMC implants become clearer and as clinical data accumulates. Industry leaders are poised to shape the next phase of implant innovation, with a strong emphasis on digitalization, customization, and scalable manufacturing processes.
Breakthrough Technologies Shaping Implant Manufacturing
Ceramic Matrix Composites (CMCs) have rapidly emerged as a transformative material in implant manufacturing, promising significant advancements in both performance and longevity. As of 2025, several breakthrough technologies are shaping the sector, driven by the need for implants that combine biocompatibility, mechanical strength, and resistance to wear. The integration of CMCs into orthopedic and dental implants is being propelled by innovations in material science, additive manufacturing, and surface engineering.
A key technological leap is the development of advanced processing techniques for producing high-purity CMCs with tailored microstructures. Companies like CeramTec have pioneered the use of silicon nitride and alumina matrix composites, leveraging proprietary sintering and hot isostatic pressing methods to achieve dense, flaw-tolerant ceramics suitable for joint and spinal implants. These processes minimize internal defects, resulting in implants with superior fracture toughness and reliability.
Additive manufacturing (AM) is another disruptive force in CMC implant fabrication. CoorsTek is among manufacturers commercializing 3D printing for bioceramic matrices, enabling the creation of complex, patient-specific geometries previously unattainable with traditional subtractive machining. The adoption of AM allows for the integration of porous architectures that promote osseointegration, crucial for long-term implant stability. Early clinical data from pilot studies with additively manufactured CMC implants show promising reductions in post-surgical complications and improved functional outcomes.
Surface modification technologies are further expanding the applicability of CMCs. Plasma-assisted coating and nano-texturing, as developed by KYOCERA Corporation, enhance the bioactivity of ceramic surfaces, fostering better cellular adhesion and reducing the risk of bacterial colonization. These surface innovations are particularly valuable in dental and spinal implants, where infection resistance and tissue integration are paramount.
Looking ahead to the next few years, the outlook for CMC implant manufacturing is marked by continued R&D investment and regulatory milestones. The push towards multi-material composites—combining ceramics with polymers or metals—aims to further improve mechanical resilience while maintaining biocompatibility. Ongoing collaborations between implant producers and academic institutions are expected to accelerate the path from laboratory-scale breakthroughs to commercial products. As regulatory frameworks in the EU and US adapt to novel materials, industry participants anticipate broader clinical adoption and expanded indications for CMC-based implants, positioning them as a cornerstone of next-generation implantology.
Regulatory Landscape & Approval Pathways (e.g., fda.gov, ema.europa.eu)
The regulatory landscape for ceramic matrix composite (CMC) implants is evolving rapidly as the medical community increasingly recognizes the distinct advantages of these materials—such as high strength, wear resistance, and biocompatibility—particularly for orthopedic and dental applications. As of 2025, major regulatory agencies like the U.S. Food and Drug Administration (FDA) and the European Medicines Agency (EMA) are actively refining pathways for the review and approval of advanced ceramic-based medical devices.
In the United States, CMC implants typically fall under the FDA’s Center for Devices and Radiological Health (CDRH) oversight, where they are classified as Class II or Class III medical devices depending on their intended use and anatomical site. For example, orthopedic load-bearing implants may require a Premarket Approval (PMA) due to their higher risk profile, while dental implants may be eligible for the more streamlined 510(k) pathway if substantial equivalence to a predicate device can be demonstrated. The FDA has issued several updates in recent years regarding the evaluation of ceramics in medical devices, emphasizing the need for robust preclinical data on mechanical performance, degradation, and biological safety, as well as post-market surveillance for long-term outcomes (FDA).
- Biocompatibility and Mechanical Testing: Regulatory authorities require comprehensive biocompatibility assessments in line with ISO 10993 standards, as well as extensive fatigue and wear testing, particularly for joint and spinal implants where CMCs are gaining traction.
- Manufacturing Controls: Manufacturers must maintain strict process controls and traceability for raw materials, sintering, and composite fabrication—a focus area since the introduction of advanced additive manufacturing and precision machining in CMC implant production (CeramTec Group).
- Clinical Evidence: Regulatory bodies are increasingly requesting real-world evidence and multicenter clinical trial data, especially for first-in-class CMC implants. This trend is evident in Europe following the implementation of the Medical Device Regulation (MDR), which places greater emphasis on post-market clinical follow-up (EMA).
Looking ahead, the next few years will likely see further harmonization of global regulatory standards as more manufacturers seek simultaneous approvals in the U.S., Europe, and Asia. Agencies are expected to issue clearer guidance specific to composite ceramics, reflecting both their unique risk profiles and growing clinical adoption. This evolving landscape underscores the importance of continuous dialogue between manufacturers, regulatory bodies, and clinical stakeholders to ensure both patient safety and timely innovation in CMC implant technologies.
Supply Chain Innovations and Challenges
The supply chain landscape for ceramic matrix composite (CMC) implant manufacturing is undergoing significant transformation as the sector adapts to rising demand, stricter regulatory requirements, and the need for advanced performance in medical devices. As of 2025, several leading manufacturers and suppliers are leveraging innovative approaches to streamline material sourcing, quality control, and regulatory compliance, while facing notable logistical and scalability challenges.
One prominent trend is the increased vertical integration by key players to ensure a reliable supply of high-purity ceramic powders and fibers, which are critical for medical-grade CMC implants. Companies such as CeramTec and Sagemax have invested in in-house production capabilities to minimize reliance on external vendors, thereby enhancing material traceability and reducing lead times. This move also helps manufacturers better comply with evolving international standards for biocompatibility and mechanical performance.
Digitalization and process automation are further reshaping the CMC implant supply chain. Advanced process control systems, including real-time monitoring and data analytics, have been deployed to ensure consistent quality during complex manufacturing steps like powder synthesis, green body shaping, and high-temperature sintering. For instance, Kyocera has adopted smart manufacturing solutions to optimize yield and minimize defects, directly addressing the historically high scrap rates and variability associated with ceramic composite processing.
However, the sector continues to grapple with challenges related to scaling up production while maintaining the stringent tolerances required for medical applications. The specialized nature of medical CMCs, such as those used in dental and orthopedic implants, means that only a handful of suppliers—primarily in Europe, Japan, and the United States—can provide certified raw materials and components. This concentration exposes manufacturers to supply chain disruptions from geopolitical tensions or raw material shortages, notably in zirconia and alumina feedstocks.
To mitigate these risks, collaborative partnerships have emerged between implant manufacturers and material producers. For example, Ivoclar has established long-term agreements with advanced ceramics suppliers to secure priority access to critical inputs, while also engaging in joint R&D to accelerate the development of next-generation composites.
Looking ahead, the outlook for supply chain innovation in CMC implant manufacturing is positive, with ongoing investments in digital traceability, additive manufacturing integration, and supplier diversification expected to bolster resilience. Nonetheless, the sector must remain vigilant to potential disruptions and continue fostering collaboration across the value chain to ensure uninterrupted delivery of life-enhancing ceramic implants.
Clinical Performance and Safety Data
Ceramic matrix composite (CMC) implants are gaining significant attention in the biomedical sector due to their superior mechanical strength, fracture toughness, and biocompatibility compared to traditional ceramic or metal implants. As of 2025, clinical performance and safety data for CMC implants are emerging from both ongoing clinical trials and post-market surveillance studies, particularly in orthopedic and dental applications.
Recent clinical data indicate that CMCs, especially those based on silicon nitride and alumina-zirconia composites, exhibit lower wear rates and minimal inflammatory response compared to conventional materials. For example, AAP Implantate AG has reported that their CMC-based spinal and orthopedic implants demonstrate robust osseointegration and reduced risk of implant-associated infections, owing to the unique surface chemistry of the composites. These findings are further corroborated by early results from clinical studies in Europe and Asia, where CMC-based dental and vertebral implants have shown high success rates and minimal adverse events over 18- to 36-month follow-up periods.
Safety profiles of CMC implants are also being strengthened by advances in manufacturing processes, ensuring consistent material quality and reducing risks associated with microcracking and structural degradation. KYOCERA Corporation, a leading manufacturer of medical ceramics, has highlighted in recent publications that their proprietary sintering and composite forming technologies yield CMC implants with enhanced reliability and predictable in vivo performance. Notably, the company has launched new CMC-based orthopedic products in Japan and Europe, supported by multi-center safety studies that show low complication rates and excellent biomechanical compatibility.
Regulatory agencies in major markets are increasingly recognizing the clinical benefits of CMC implants. In 2024 and early 2025, both the U.S. Food and Drug Administration and the European Medicines Agency have granted expedited pathways or full approvals to select CMC implant systems, based on robust performance and safety data. CeramTec, a key supplier of advanced ceramics for medical use, reported in early 2025 that over two million CMC-based hip and knee components have been implanted worldwide, with revision and complication rates continuing to decline as manufacturing and sterilization protocols are refined.
Looking ahead, as longer-term data from ongoing registries and post-market studies become available, the expectation is that CMC implants will continue to demonstrate favorable safety and clinical performance, further solidifying their role in next-generation orthopedic and dental implantology.
Competitive Analysis: Traditional vs. Composite Implants
Ceramic matrix composite (CMC) implant manufacturing is poised to play an increasingly significant role in the orthopedic and dental sectors in 2025 and the near future. Historically, metals such as titanium and cobalt-chrome alloys have dominated implant production due to their mechanical strength and proven biocompatibility. However, traditional metallic implants are susceptible to issues such as stress shielding, corrosion, and adverse biological reactions, driving the search for alternatives that can better mimic the properties of natural bone.
CMC implants offer a compelling competitive alternative, leveraging ceramics reinforced with fibers such as silicon carbide or alumina to achieve a synergistic balance of toughness, strength, and bioinertness. Current manufacturing advances—including advanced powder processing, hot isostatic pressing, and additive manufacturing—have enabled the production of increasingly complex and patient-specific CMC structures. For example, CeramTec has expanded its portfolio of BIOLOX® CMC components, reporting enhanced wear resistance and reduced risk of ion release compared to metal counterparts. Similarly, Sagemax Bioceramics continues to develop CMC-based dental restorations, focusing on translucency, mechanical strength, and long-term stability.
Clinical data emerging in 2024 and into 2025 suggest that CMC implants are increasingly comparable, and in some cases superior, to traditional implants in terms of osseointegration and longevity. Notably, Zimmer Biomet and Stryker have both initiated partnerships and pilot programs to evaluate the use of ceramic matrix composites in next-generation load-bearing joint replacements, aiming to reduce revision surgery rates by minimizing implant-related complications.
Despite these advances, CMC implant manufacturing faces challenges. Production costs remain higher than those for traditional metal implants due to the complexity of processing and quality assurance requirements. However, as companies such as CeramTec and Sagemax Bioceramics invest in automation and scalable additive manufacturing, the cost differential is expected to narrow through 2025 and beyond.
Looking ahead, the competitive landscape is likely to shift further as regulatory bodies approve more CMC-based devices for widespread clinical use. The next few years are expected to see intensified collaboration between implant manufacturers, materials science firms, and healthcare providers to refine CMC technologies, improve patient outcomes, and address the limitations of traditional implants.
Emerging Applications Beyond Orthopedics
Ceramic Matrix Composite (CMC) implant manufacturing, traditionally centered in orthopedic applications, is evolving rapidly in 2025 and is poised to impact a broader spectrum of medical fields over the coming years. Leveraging their superior biocompatibility, wear resistance, and tailored mechanical properties, CMCs are now being explored for use in dental, craniofacial, cardiovascular, and even neurosurgical implants.
In dental implantology, manufacturers are advancing CMC-based prosthetics to address the limitations of traditional titanium and zirconia implants, such as metal hypersensitivity and suboptimal esthetics. Companies like CeramTec have expanded their dental ceramics portfolio to include composite systems with enhanced fracture toughness and bioactivity, aiming for long-term integration and reduced peri-implantitis. The ongoing clinical trials in 2025 are expected to yield data supporting regulatory submissions for new CMC dental abutments and crowns.
Craniofacial reconstruction is another emerging frontier. CMC scaffolds, with their tunable porosity and load-bearing capacity, are being engineered as custom implants for maxillofacial trauma and congenital deformities. Kyocera Corporation has initiated collaborative projects with university hospitals to develop CMC cranial plates designed for both pediatric and adult patients, utilizing additive manufacturing for patient-specific geometries. Early preclinical outcomes indicate promising osteointegration and radiolucency, facilitating post-operative imaging.
Cardiovascular applications are also on the horizon. Research divisions at Schunk Group are advancing CMC-based heart valve components, targeting improved durability over polymeric or metallic alternatives. In 2025, pilot manufacturing lines are being set up to produce test batches of CMC valves and stent coatings, with in vivo studies scheduled through 2026. The objective is to minimize thrombogenicity while extending implant lifespan—a critical requirement for younger cardiac patients.
In the field of neurosurgery, CMCs are being trialed for spinal fusion cages and cranial spacers. Sagemax is developing novel CMC formulations that aim to promote bone ingrowth and reduce imaging artifacts, facilitating post-surgical assessments. Initial prototypes entered preclinical evaluation in late 2024, with first-in-human trials anticipated by 2026.
Given the momentum in manufacturing capabilities—especially the integration of additive manufacturing and surface functionalization techniques—it is expected that CMC implants will secure new regulatory approvals across multiple sectors by 2027. These advances signal a significant expansion for CMCs beyond orthopedics, with ongoing investments from established ceramic manufacturers and medical device innovators.
Future Outlook: Investment, R&D Hotspots, and Next-Gen Materials
The landscape of ceramic matrix composite (CMC) implant manufacturing is poised for significant advancements over 2025 and the following years, propelled by robust investments, targeted R&D initiatives, and the emergence of next-generation materials. As demand for high-performance biomedical implants grows—driven by aging populations and the need for improved patient outcomes—companies and research organizations are intensifying efforts to enhance both the properties and manufacturability of CMCs.
Investment activity is particularly strong among medical device manufacturers seeking to differentiate their implant portfolios. Major players such as Smith+Nephew have announced increased allocations toward advanced materials research, focusing on improving the wear resistance and biocompatibility of ceramic-based orthopedic implants. Additionally, Stryker is expanding its R&D footprint in ceramic composites, with a focus on additive manufacturing techniques that promise greater design flexibility and faster prototyping cycles for patient-specific solutions.
R&D hotspots are emerging in regions with established biomedical engineering clusters. The United States and Germany continue to lead, bolstered by university-industry collaborations and support from organizations like the Deutsche Keramische Gesellschaft (German Ceramic Society). In Asia, Japanese companies such as Tosoh Corporation are spearheading work on zirconia-toughened alumina (ZTA) composites, aiming to optimize the balance between fracture toughness and long-term stability—crucial for joint and dental implants.
The next wave of CMC implant materials is centered on hybrid composites, including those reinforced with silicon carbide fibers or nano-engineered phases. These advances are expected to deliver superior mechanical properties while maintaining or improving the bioinert nature of ceramics. Companies like CoorsTek are investing in scalable manufacturing processes to bring these next-gen materials to market, emphasizing powder processing innovations and precision sintering controls.
Looking ahead, the field is likely to benefit from integration with digital manufacturing platforms. The adoption of AI-driven process optimization and in-line quality monitoring—championed by technology suppliers such as GE Additive—is anticipated to enhance consistency and regulatory compliance. As regulatory agencies tighten standards for implantable devices, R&D is also focusing on developing advanced characterization techniques and long-term performance validation.
Overall, the next few years will be marked by intensified collaboration across the supply chain, sustained capital inflows, and a transition toward smarter, more sustainable manufacturing of CMC implants, aligning with the evolving needs of the medical sector and global patient populations.