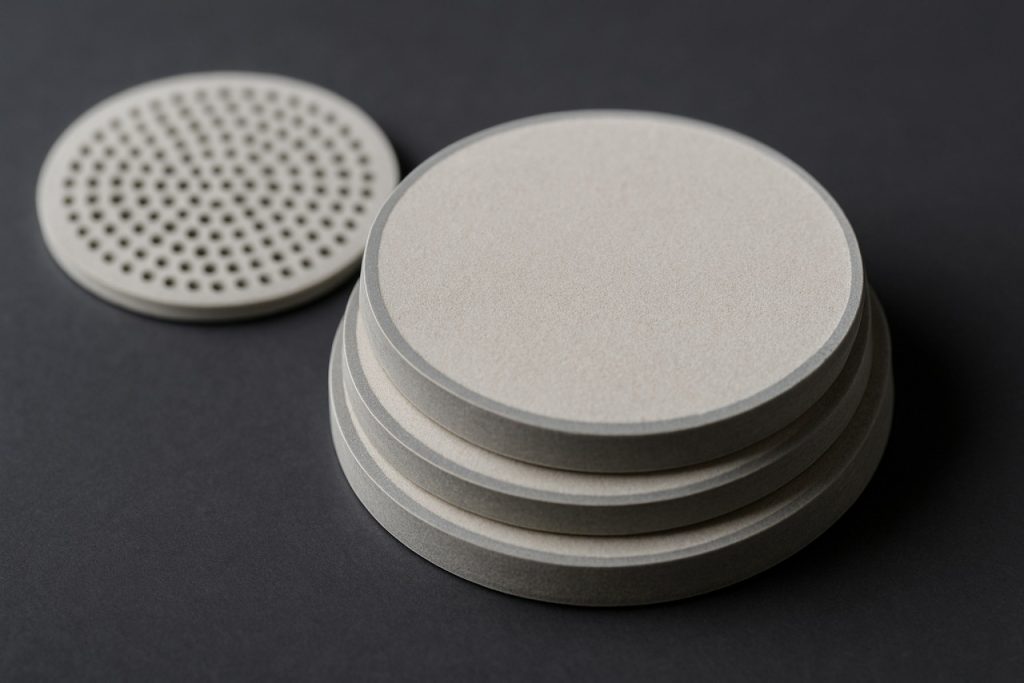
Table of Contents
- Executive Summary: Key Insights for 2025 and Beyond
- Electroceramic Membrane Technology: Current State and Recent Breakthroughs
- Emerging Fabrication Techniques: From Additive Manufacturing to Nanoengineering
- Market Size and Growth Forecasts Through 2029
- Major Players and New Entrants: Profiles and Strategic Moves
- Applications in Energy, Water Treatment, and Industrial Sectors
- Supply Chain and Raw Materials: Critical Developments and Risks
- Sustainability and Regulatory Landscape
- Intellectual Property & Patent Trends
- Future Outlook: Innovations, Opportunities, and Challenges
- Sources & References
Executive Summary: Key Insights for 2025 and Beyond
Electroceramic membrane fabrication continues to be a focal point in advanced materials engineering, especially as industries seek robust solutions for energy, environmental, and chemical processing applications. As of 2025, key developments are being driven by the dual imperatives of sustainability and operational efficiency, with a strong emphasis on scalable manufacturing and integration with emerging energy technologies.
Leading manufacturers are actively refining fabrication techniques to address the challenges of cost, durability, and functional performance. For instance, 3M has accelerated research into scalable tape casting and isostatic pressing, enabling the production of high-density ceramic membranes for gas separation and ionic transport. These methods are being adopted to enhance reproducibility and reduce defects, vital for large-scale deployment in hydrogen and oxygen generation systems.
Advancements in additive manufacturing are also reshaping the landscape. CoorsTek reports increased adoption of 3D printing and automated layering technologies to produce complex geometries and graded structures, which improve membrane selectivity and mechanical integrity. This transition is expected to support rapid prototyping and customization, responding directly to application-specific demands in sectors such as water purification and fuel cells.
Material innovation remains a priority, with companies like Saint-Gobain focusing on advanced zirconia, alumina, and perovskite compositions. These materials are tailored for enhanced ionic conductivity, chemical stability, and resistance to thermal cycling, addressing key operational barriers in electrochemical reactors and solid oxide systems.
Industry collaborations are increasingly common, aiming to accelerate commercialization and standardization. For example, Sasol is working with membrane and catalyst suppliers to integrate electroceramic membranes into next-generation syngas and hydrogen production units. Such partnerships are expediting the translation of lab-scale innovations into real-world industrial applications.
Looking ahead, the outlook for electroceramic membrane fabrication is highly promising. Ongoing investments in digital process monitoring, intelligent quality control, and advanced materials discovery are set to improve yield and lower costs. Companies anticipate that by 2027, these combined advancements will enable broader adoption across energy, water, and chemical industries, supporting decarbonization and circular economy objectives globally.
Electroceramic Membrane Technology: Current State and Recent Breakthroughs
Electroceramic membrane fabrication continues to advance rapidly, with significant progress seen in both scalable manufacturing techniques and materials engineering. In 2025, industrial and research organizations are converging on strategies that combine cost-effective production with improved membrane selectivity, ionic conductivity, and durability. The fabrication landscape is increasingly shaped by demand from environmental, energy, and chemical sectors, where robust and high-performance membranes are crucial.
A key trend is the refinement of tape casting and extrusion processes to produce dense and defect-free ceramic layers, vital for fuel cell and gas separation applications. Companies such as KERAFOL Keramische Folien GmbH have optimized tape casting formulations, enabling thinner membranes with enhanced mechanical stability and reproducibility. Simultaneously, the adoption of advanced sintering techniques—including spark plasma sintering and microwave sintering—has allowed for reduced processing temperatures and grain boundary engineering, as reflected in updates from CoorsTek on their ceramic membrane product lines.
Material innovation is another driving force in 2025. The integration of mixed ionic-electronic conducting (MIEC) oxides, such as perovskites and fluorites, is expanding the operational window of electroceramic membranes. Nippon Chemical Industrial Co., Ltd. reports ongoing development of perovskite-based powders tailored for membrane applications, supporting both high oxygen permeability and chemical stability. At the same time, manufacturers like Elcowa are scaling up the production of multi-layer and composite membranes, combining different ceramic phases to optimize performance for specific industrial processes.
Automation and digitalization of fabrication workflows are also gaining momentum. Process control systems, real-time monitoring, and data-driven optimization are reducing batch-to-batch variability and improving yields, as highlighted by advancements in production lines at Membranes International Inc.. Digital twins and simulation tools are increasingly being deployed to accelerate product development cycles and troubleshoot process bottlenecks.
Looking ahead, industry observers anticipate that by 2027–2028, further breakthroughs in additive manufacturing—such as inkjet and 3D printing of electroceramic structures—will enable more complex architectures and rapid prototyping. These innovations, combined with sustainable raw material sourcing and recycling strategies, are poised to expand the application scope and economic viability of electroceramic membranes across sectors.
Emerging Fabrication Techniques: From Additive Manufacturing to Nanoengineering
The landscape of electroceramic membrane fabrication is rapidly evolving in 2025, driven by the integration of advanced manufacturing processes and nanoengineering strategies. Traditional fabrication routes, such as tape casting, extrusion, and uniaxial pressing, have provided the industry with robust membranes for applications in gas separation, solid oxide fuel cells, and water treatment. However, recent years have seen a pronounced shift toward more versatile and precise techniques, notably additive manufacturing (AM) and nanoengineering, to address the growing demand for customizable, high-performance membranes.
Additive manufacturing, particularly 3D printing, has emerged as a transformative approach to electroceramic membrane production. Companies and research groups are leveraging AM’s ability to create complex geometries and tailored pore architectures that are difficult to achieve with conventional methods. For example, Tethon 3D specializes in ceramic 3D printing, offering materials and technologies compatible with electroceramic compositions. Their work enables rapid prototyping and the manufacture of membranes with precisely controlled features, which can enhance ionic conductivity and selectivity for specific applications.
Nanoengineering is another key trend, with organizations employing nanoscale additives, coatings, and structural modifications to improve membrane performance. Saint-Gobain has developed advanced ceramic materials for membranes, incorporating nano-sized grains and engineered interfaces to boost durability and functional efficiency. The integration of nanostructures not only refines the selective transport properties of the membranes but also addresses challenges related to mechanical stability and long-term operation, especially under harsh chemical or thermal conditions.
Hybrid fabrication approaches are gaining momentum as well. For instance, the combination of additive manufacturing with post-processing techniques, such as laser sintering or atomic layer deposition, allows for the creation of multi-layered or gradient-structured electroceramic membranes. Companies like 3D Systems are expanding their portfolio to support ceramic and electroceramic part production, indicating a broader industry shift toward digital manufacturing for functional ceramics.
Looking ahead, the outlook for electroceramic membrane fabrication is marked by the convergence of digital design, materials innovation, and process automation. As equipment and material portfolios continue to expand, more suppliers are expected to enter the field, driving down costs and enabling broader adoption in sectors such as clean energy and industrial gas processing. Ongoing R&D by industry leaders promises further optimization of membrane architecture and functionalization, setting the stage for next-generation electroceramic membranes with unprecedented performance and adaptability through 2025 and beyond.
Market Size and Growth Forecasts Through 2029
The global market for electroceramic membrane fabrication is poised for significant expansion through 2029, driven by increasing demand for advanced filtration technologies in sectors such as water treatment, energy, and electronics. As of 2025, growth is underpinned by heightened adoption of ceramic membranes for their superior chemical and thermal stability compared to polymeric alternatives. Companies such as Koninklijke DSM N.V. (via its Norit Membrane Technology) and Pall Corporation are actively developing and commercializing robust electroceramic membranes for diverse industrial applications.
Recent advancements in fabrication techniques—including tape casting, extrusion, and additive manufacturing—are enabling the production of membranes with tailored pore structures and enhanced ionic conductivity. NGK Insulators, Ltd. has reported ongoing scaling of its ceramic membrane production, citing increased demand from the chemical and environmental sectors. Meanwhile, LiqTech International, Inc. continues to invest in automated manufacturing lines to meet growing orders for silicon carbide (SiC) and alumina-based membrane modules.
The market outlook through 2029 indicates a compound annual growth rate (CAGR) in the high single digits, with Asia-Pacific and Europe leading in both production capacity and end-market consumption. Expansion in China is particularly notable, where manufacturers such as Nano Science & Technology Co., Ltd. are ramping up capacity to address stringent water reuse regulations and industrial wastewater treatment requirements. In Europe, KERAFOL Keramische Folien GmbH & Co. KG is enhancing its offerings with membranes tailored for high-purity and energy-efficient processes.
Electroceramic membranes are also gaining momentum in hydrogen production, solid oxide fuel cells, and gas separation, further diversifying market growth drivers. For example, Ionics, Incorporated is collaborating with energy sector stakeholders to deploy ceramic membranes in green hydrogen projects. Additionally, government-backed initiatives and public-private partnerships in the EU and Asia are expected to boost R&D funding and infrastructure investment, fostering further innovation in fabrication processes and scaling.
In summary, current data from leading manufacturers and industry bodies suggest robust expansion of the electroceramic membrane fabrication market through 2029, supported by technological innovation, regulatory drivers, and the growing need for sustainable industrial solutions.
Major Players and New Entrants: Profiles and Strategic Moves
The electroceramic membrane fabrication sector is witnessing significant activity in 2025, with established players consolidating their positions and a wave of innovative entrants broadening the competitive landscape. This dynamism is driven by rising demand for high-performance membranes in energy, environmental, and industrial applications, particularly hydrogen separation, gas purification, and solid oxide fuel cells.
Established Players
- KERAFOL Keramische Folien GmbH, headquartered in Germany, remains a leading manufacturer of ceramic membranes, specializing in both flat-sheet and tubular formats. Their ongoing R&D has resulted in the commercialization of robust, high-temperature stable membranes for gas separation and filtration, with recent investments in upscaling production lines to meet growing European and Asian demand.
- NGK Insulators, Ltd. of Japan continues to be a global leader, leveraging their expertise in fine ceramics. In 2025, they have expanded their product portfolio to include next-generation tubular oxygen permeable membranes, targeting industrial decarbonization projects and pilot-scale hydrogen production facilities. NGK’s strategic collaborations with utility companies and chemical manufacturers are expected to yield commercial-scale demonstration plants in the near term.
- Ionics, Incorporated, based in the United States, has expanded its focus beyond water treatment to advanced gas-separation ceramic membranes. Their recent joint ventures with process engineering firms aim to scale up membrane module manufacturing for carbon capture and blue hydrogen applications.
New Entrants and Strategic Moves
- HyGear (Netherlands), previously focused on gas generation, entered the electroceramic membrane market by launching “HyPERM” in late 2024. This proprietary membrane technology targets decentralized hydrogen production and purification, and the company has announced pilot installations with European industrial gas suppliers in 2025.
- Fraunhofer Society (Germany) is advancing scalable fabrication processes through its collaborative industrial platforms. Their focus on additive manufacturing for ceramic membranes is attracting spin-offs and partnerships, with demonstration projects scheduled for 2025–2026.
- CoorsTek, Inc. (USA) has announced plans to establish a dedicated electroceramic membrane division in 2025, leveraging its established ceramics expertise to develop new materials for harsh operating environments. Their collaboration with chemical process industries signals a commitment to rapid technology transfer and commercialization.
Looking forward, ongoing investments and strategic alliances suggest continued growth and technical evolution in electroceramic membrane fabrication. As major players ramp up capacity and new entrants introduce disruptive technologies, the sector is poised for accelerated deployment across critical clean energy and industrial decarbonization markets.
Applications in Energy, Water Treatment, and Industrial Sectors
Electroceramic membrane fabrication has seen significant advancements entering 2025, driven by the urgent need for robust solutions in energy, water treatment, and industrial applications. These membranes, typically composed of materials such as perovskite-type oxides, yttria-stabilized zirconia, and doped ceria, are prized for their stability, selectivity, and ionic conductivity. The fabrication process—encompassing powder synthesis, tape casting, screen printing, and sintering—has shifted towards greater automation, process control, and sustainable materials sourcing.
In the energy sector, electroceramic membranes are increasingly central to the development of solid oxide fuel cells (SOFCs) and oxygen separation units. Companies like Norcatec and Hexis AG have refined fabrication techniques to produce dense, thin ceramic electrolytes that enhance SOFC durability and efficiency. Recent data indicate that multi-layer co-sintering—where membrane and electrode layers are fabricated simultaneously—has reduced production time while improving interface quality, a crucial factor for commercial-scale deployment.
For water treatment, the demand for membranes capable of selective ion transport and resistance to fouling has promoted research into defect engineering and composite structures. NGK Insulators has reported progress in the manufacture of ceramic membranes with finely tuned pore structures for desalination and industrial wastewater reuse, leveraging proprietary extrusion and sintering processes that enable scale-up without compromising membrane performance.
In industrial gas separation and chemical processing, electroceramic membranes are being adopted for high-temperature hydrogen production, ammonia synthesis, and carbon dioxide separation. Fraunhofer Society and SINTEF are collaborating with manufacturing partners to move from laboratory-scale fabrication to pilot lines, employing advanced methods such as spark plasma sintering and additive manufacturing. These approaches allow for precise control over microstructure, density, and membrane thickness, directly influencing selectivity and permeation rates.
Looking ahead, the outlook for electroceramic membrane fabrication is marked by integration of digital manufacturing and in-line quality control systems. Industry leaders anticipate further cost reductions through automation and material optimization, with membranes tailored for harsh environments and longer lifespans. As production scales up to meet the growing needs of decarbonized energy and circular water systems, partnerships between industrial companies and R&D institutes are expected to accelerate commercialization and deployment of next-generation electroceramic membranes.
Supply Chain and Raw Materials: Critical Developments and Risks
The fabrication of electroceramic membranes, a cornerstone technology for applications such as solid oxide fuel cells (SOFCs), gas separation, and electrochemical reactors, is undergoing rapid evolution in its supply chain and raw materials sourcing as of 2025. Electroceramic membranes typically utilize advanced oxide materials—most notably perovskite-type oxides such as lanthanum strontium cobalt ferrite (LSCF) and yttria-stabilized zirconia (YSZ). The continuous expansion of clean energy initiatives and hydrogen economies is driving robust demand for these specialized ceramics, increasing pressure on supply chains for high-purity rare earths and transition metals.
Key players in the materials market, such as Tosoh Corporation and Saint-Gobain, have reported rising orders for zirconia powders and rare-earth stabilized oxides. FUJIFILM Corporation has also expanded its ceramic materials portfolio in response to this demand. The supply chain remains highly sensitive to geopolitical shifts, particularly concerning raw materials like yttrium, lanthanum, and cobalt, which are predominantly mined and processed in a handful of countries, including China and the Democratic Republic of the Congo. These dependencies have prompted companies to explore alternative sourcing strategies and recycling initiatives.
To address supply risks, manufacturers have begun investing in localized and diversified sourcing. For example, Solvay has announced efforts to recycle rare earths from electronic waste, aiming to supplement primary mining activities. Concurrently, 3M is optimizing its ceramic manufacturing processes to reduce raw material intensity and waste, contributing to greater supply chain resilience.
Nevertheless, persistent challenges remain. Global logistics disruptions—exacerbated by shipping bottlenecks and ongoing trade tensions—continue to impact the steady supply of high-purity oxides. Price volatility for critical oxides has been noted throughout 2024 into 2025, leading to increased production costs for electroceramic membranes. In response, industry leaders such as KYOCERA Corporation are actively investing in R&D for alternative ceramic compositions that rely less on supply-constrained elements.
Looking ahead, the sector is expected to see a gradual shift toward circular economy models and vertical integration to mitigate supply chain risks over the next few years. Partnerships among raw material suppliers, membrane manufacturers, and end-users are likely to intensify, with sustainability and supply security as primary drivers.
Sustainability and Regulatory Landscape
In 2025, the sustainability and regulatory landscape for electroceramic membrane fabrication is undergoing rapid evolution, shaped by stricter environmental mandates and increasing industry commitments to circular economy principles. The fabrication of electroceramic membranes—vital in sectors such as water purification, fuel cells, and gas separation—entails high-temperature processes and the use of rare or energy-intensive materials such as zirconia, alumina, and perovskite oxides. As decarbonization targets intensify globally, manufacturers are innovating to reduce the environmental footprint of both raw material sourcing and manufacturing operations.
One notable trend is the transition to greener synthesis routes. Companies like Saint-Gobain and KYOCERA Corporation are investing in low-emission kilns and alternative sintering techniques that decrease energy consumption and curb greenhouse gas emissions. There is also a growing emphasis on recycling ceramic waste and integrating industrial byproducts into membrane formulations, thus aligning with circularity goals and minimizing landfill contributions.
On the regulatory side, the European Union’s tightening of the Industrial Emissions Directive and implementation of the new Ecodesign for Sustainable Products Regulation are expected to directly impact ceramic membrane producers operating or selling in Europe. These policies demand enhanced lifecycle assessments, stricter limits on hazardous substances, and extended producer responsibility, prompting companies to adopt greener chemistries and transparent supply chain practices. Cerame-Unie, the European ceramics industry body, is working closely with policymakers to ensure that new standards for energy use, emissions, and recycling are both ambitious and feasible for advanced ceramics manufacturers.
In parallel, the U.S. Environmental Protection Agency is rolling out updates to the National Emission Standards for Hazardous Air Pollutants (NESHAP) for ceramics manufacturing, mandating tighter control of particulate and volatile emissions. Leading U.S.-based producers such as CoorsTek are already piloting closed-loop water systems and renewable energy integration in their plants to pre-emptively comply with anticipated regulations and to meet the sustainability criteria set by key customers, especially in the electronics and clean energy sectors.
Looking forward, the next few years will see a convergence of regulatory compliance and market demand for sustainable solutions. Industry leaders are expected to accelerate research into lead-free and rare earth-free compositions, as well as digital tools for real-time process monitoring to optimize resource efficiency. The evolution of the regulatory landscape will continue to act as both a driver and a benchmark for innovation in electroceramic membrane fabrication, ensuring that sustainability remains at the core of sectoral advancement.
Intellectual Property & Patent Trends
The landscape of intellectual property (IP) and patent activity in the field of electroceramic membrane fabrication continues to evolve rapidly as the sector matures and new commercial applications emerge. Over the past year and looking ahead into 2025 and the subsequent few years, innovation in materials composition, processing methodologies, and device integration is driving a significant uptick in both patent filings and granted patents worldwide.
A notable trend is the increasing focus on scalable fabrication methods tailored to industrial requirements. For instance, companies such as Noritake Co., Limited and CoorsTek, Inc. have been actively patenting techniques for producing dense, defect-free ceramic membranes via advanced sintering and tape casting methods. These patents often encompass not just the composition of the electroceramic material—such as perovskite oxides and mixed ionic-electronic conductors—but also innovative approaches for layer structuring, interfacial engineering, and integration with metallic supports for enhanced mechanical stability.
In 2024, the European Patent Office and the United States Patent and Trademark Office registered a steady increase in applications relating to asymmetric membrane architectures and hybrid multilayer assemblies. These filings reflect concerted R&D efforts by both established manufacturers and academic-industry partnerships aiming to overcome longstanding challenges in flux, selectivity, and long-term durability.
Emerging players, such as Ionotec Ltd., are also contributing to the patent landscape by securing IP for novel lithium and sodium ion-conducting glass ceramics, targeting next-generation energy and gas separation markets. Similarly, Elcogen has expanded its patent portfolio around planar ceramic membrane cells for solid oxide fuel cell and electrolysis applications, emphasizing proprietary fabrication steps that enhance electrochemical performance and manufacturability.
Looking forward, the next few years are expected to see a continued acceleration of patent activity, especially regarding high-throughput and additive manufacturing techniques. There is also anticipation of increased cross-licensing and strategic collaborations, as leading players seek to balance protection of core fabrication know-how with the need for interoperability and supply chain robustness. Overall, the competitive IP landscape underscores the central role of innovation and process optimization in scaling up electroceramic membrane production for broad industrial deployment.
Future Outlook: Innovations, Opportunities, and Challenges
As the global demand for advanced separation technologies accelerates, the fabrication of electroceramic membranes is poised for significant innovation and expansion in 2025 and the years immediately following. The sector is witnessing increased investment in scalable manufacturing processes, with a focus on enhancing membrane performance, durability, and cost-effectiveness for industrial applications such as hydrogen production, carbon capture, and water treatment.
One major trend is the adoption of additive manufacturing and advanced sintering techniques to produce membranes with precise microstructures. Companies such as CeramTec are exploring automated processing routes and digital quality controls to reduce defects and ensure reproducibility at scale. Similarly, Noritake Co., Limited has announced initiatives to refine tape casting and extrusion methods, facilitating the fabrication of complex geometries and multilayer architectures necessary for next-generation electroceramic devices.
Materials innovation remains central. The deployment of new perovskite and mixed ionic-electronic conducting (MIEC) compositions offers improved ionic conductivity and chemical stability, addressing longstanding challenges in aggressive operating environments. For instance, Fiaxell Sàrl is advancing scalable processes for manufacturing membranes based on novel oxide ceramics for solid oxide electrolyzers and fuel cells. Meanwhile, Elcocat s.r.l. is focusing on cost reduction by optimizing raw material supply chains and adopting lower-temperature fabrication routes.
Despite these technological advances, several challenges persist. Achieving consistent large-area membrane fabrication with minimal performance variation is a key hurdle, particularly for applications requiring high purity and long operational lifetimes. Furthermore, the integration of electroceramic membranes into existing industrial systems demands rigorous standardization and long-term field validation. Organizations such as European Power Membranes Association are working with industry partners to develop performance benchmarking protocols and accelerate regulatory acceptance.
Looking ahead, the outlook for 2025 and beyond is one of cautious optimism. The rising demand for green hydrogen and decarbonization technologies is expected to drive further innovation in electroceramic membrane fabrication. Strategic partnerships between material suppliers, technology developers, and end-users are likely to play a pivotal role in scaling up production, reducing costs, and unlocking new markets. The convergence of digital manufacturing, advanced materials science, and market pull from clean energy sectors positions electroceramic membranes as a cornerstone of future sustainable technologies.
Sources & References
- Sasol
- KERAFOL Keramische Folien GmbH
- Nippon Chemical Industrial Co., Ltd.
- Elcowa
- Membranes International Inc.
- Tethon 3D
- 3D Systems
- Pall Corporation
- NGK Insulators, Ltd.
- LiqTech International, Inc.
- Fraunhofer Society
- Hexis AG
- SINTEF
- FUJIFILM Corporation
- KYOCERA Corporation
- Noritake Co., Limited
- Elcogen
- CeramTec
- Fiaxell Sàrl