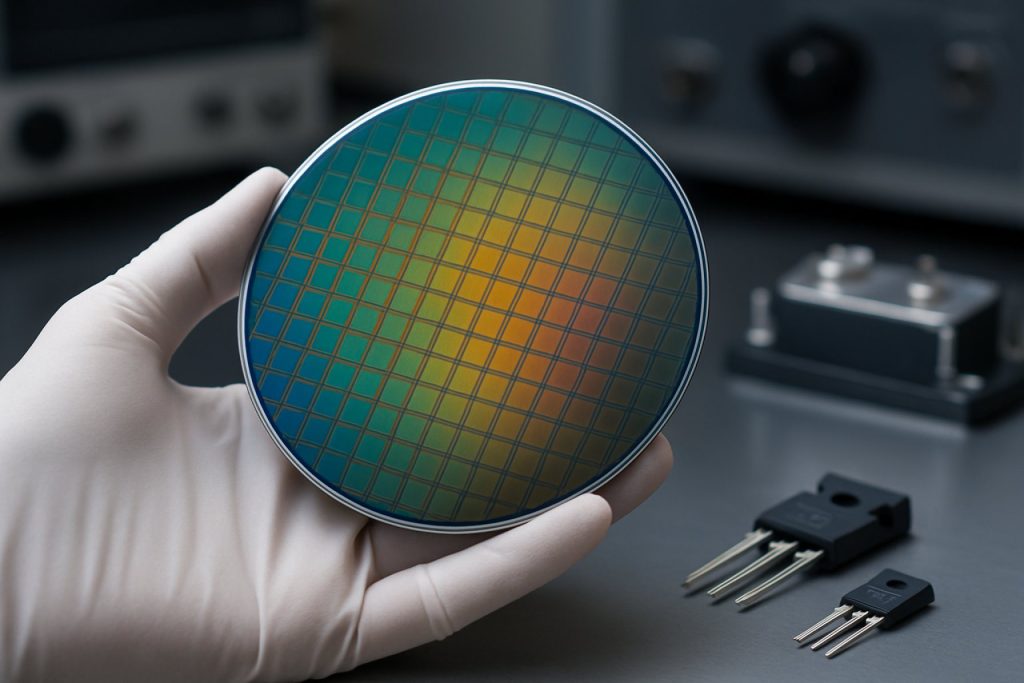
Table of Contents
- Executive Summary: 2025 and Beyond
- Market Size and Forecast to 2030
- Key Application Segments: Power, RF, and Optoelectronics
- Major Players and Strategic Partnerships (2025 Update)
- Technology Advances in GaN Epitaxial Growth Processes
- Supply Chain Dynamics and Raw Material Sourcing
- Cost Drivers and Competitive Pricing Trends
- Regulatory and Industry Standards (IEEE, JEDEC, etc.)
- Emerging Opportunities: Automotive, 5G, and Quantum Devices
- Future Outlook: Disruptive Trends and Strategic Recommendations
- Sources & References
Executive Summary: 2025 and Beyond
Gallium Nitride (GaN) epitaxial layer fabrication stands at a pivotal juncture in 2025, driven by rapid advancements in semiconductor manufacturing and surging demand for high-performance power and RF electronics. The global transition from silicon-based to wide bandgap materials has intensified, as GaN epitaxial layers enable devices with higher efficiency, faster switching speeds, and superior thermal stability. Major industry players continue to expand production capacities and diversify substrate options, reflecting the sector’s growth trajectory and evolving technical requirements.
In 2025, leading manufacturers have ramped up the deployment of advanced Metal-Organic Chemical Vapor Deposition (MOCVD) systems, the dominant technology for GaN epitaxial growth. ams OSRAM and Nitride Semiconductors have both announced new facilities and process optimizations targeting high-brightness LED and power device markets. Substrate innovation is also notable, with Kyocera and SiC-on-GaN developing larger diameter wafers (up to 200 mm), aiming to reduce costs and improve throughput for mass-market adoption.
A key trend in 2025 is the broader adoption of GaN-on-Si substrates, driven by their compatibility with established silicon fabs and cost efficiencies. STMicroelectronics and Infineon Technologies have both unveiled commercial GaN-on-Si power devices, underpinned by proprietary epitaxial growth techniques that enhance layer uniformity and defect control. Meanwhile, EpiGaN (a division of Soitec) has introduced advanced in-situ monitoring solutions to ensure tighter process control during epitaxial fabrication, a crucial factor as device geometries shrink and performance specifications tighten.
Research and pilot production for next-generation GaN epitaxy—such as vertical device architectures and novel heterostructures—are accelerating, with pSemi (a Murata company) and Samsung Electronics investing in R&D for RF and mobile applications. Collaborative initiatives, including public-private partnerships in Japan and Europe, are expected to yield further breakthroughs in layer quality, defect mitigation, and integration with CMOS platforms.
Looking beyond 2025, the outlook for GaN epitaxial layer fabrication is robust. Continued investments in automation, larger substrates, and integration technologies will drive down costs and expand market reach across automotive, industrial, telecom, and consumer sectors. The coming years are likely to see GaN epitaxy become increasingly central to the global semiconductor ecosystem, underpinning the next wave of power and RF device innovation.
Market Size and Forecast to 2030
The global market for gallium nitride (GaN) epitaxial layer fabrication is poised for significant expansion through 2030, driven by surging demand in sectors such as power electronics, radiofrequency (RF) devices, and optoelectronics. In 2025, major semiconductor manufacturers are ramping up investments in advanced metal-organic chemical vapor deposition (MOCVD) and hydride vapor phase epitaxy (HVPE) systems to scale up production and meet the quality requirements of next-generation devices.
Key industry players such as ams OSRAM, Nitride Semiconductors Co., Ltd., and KYOCERA Corporation are expanding their GaN epitaxy capabilities to address the growing adoption of GaN power devices in electric vehicles, 5G infrastructure, and fast-charging applications. According to Infineon Technologies AG, the transition to GaN for power conversion is accelerating due to its superior energy efficiency and compactness, which are vital for consumer electronics and renewable energy systems.
Production capacity expansion is evident in recent announcements. ams OSRAM has initiated new GaN-on-silicon epitaxial wafer projects targeting high-brightness LEDs and microLED displays, with volume ramp-up expected in 2025 and 2026. Likewise, Nitride Semiconductors Co., Ltd. continues to invest in UV LED epitaxial technology, with a focus on 6-inch and 8-inch wafer formats to improve throughput and reduce costs.
Forecasts indicate that GaN epitaxial wafer demand will outpace that of traditional silicon and silicon carbide (SiC) substrates by 2027, especially as automotive OEMs and telecom equipment manufacturers adopt GaN-based solutions. ROHM Co., Ltd. and Panasonic Corporation are both scaling their GaN wafer production lines, aiming to supply discrete devices and power modules for fast-growing automotive and industrial markets.
Looking forward, the GaN epitaxial fabrication sector is likely to see compound annual growth rates (CAGR) in the double digits, supported by ongoing process innovations and the migration to larger wafer diameters, which drive down manufacturing costs per device. Strategic partnerships among substrate suppliers, MOCVD tool makers, and device manufacturers are anticipated to further streamline the supply chain and accelerate time-to-market for advanced GaN components through 2030.
Key Application Segments: Power, RF, and Optoelectronics
Gallium Nitride (GaN) epitaxial layer fabrication is central to the advancement of critical application segments—namely power electronics, radio frequency (RF) devices, and optoelectronics. As of 2025, industry momentum is being driven by the need for higher performance, efficiency, and scalability, with leading manufacturers investing in next-generation epitaxial growth technologies.
- Power Electronics: The demand for efficient, high-voltage power devices is sustaining rapid innovation in GaN epitaxial wafer production. Companies such as Infineon Technologies AG are scaling metal-organic chemical vapor deposition (MOCVD) processes for high-quality GaN-on-silicon and GaN-on-SiC structures, targeting applications from electric vehicles to data centers. TECAN and Nitride Semiconductors Co., Ltd. are similarly investing in process control and uniformity to support mass production, with 200 mm GaN-on-Si wafers entering pilot lines and early commercial adoption.
- RF Devices: The proliferation of 5G networks and satellite communications is accelerating the development of high-electron-mobility transistors (HEMTs) and RF power amplifiers based on GaN epitaxial layers. Wolfspeed, Inc. is expanding its epitaxy capacity for GaN-on-SiC wafers, supporting device architectures that enable higher frequency and power density. ROHM Semiconductor is also advancing its GaN-on-SiC and GaN-on-silicon epitaxial technologies for RF front-end modules, focusing on low defect densities and high reliability.
- Optoelectronics: The adoption of GaN epitaxial layers in LEDs, laser diodes, and micro-LED displays remains strong. OSRAM and Sanan Optoelectronics Co., Ltd. are implementing advanced MOCVD reactors and in-situ process monitoring for improved wavelength uniformity and defect reduction. Recent developments include high-brightness blue and green micro-LED arrays, with epitaxial process refinements critical for pixel size reduction and mass transfer yields.
Looking ahead, the next few years are expected to see greater integration of artificial intelligence and machine learning for epitaxial process optimization, increased adoption of larger wafer diameters, and the emergence of novel substrate materials. These trends will be pivotal in meeting the growing demand across power, RF, and optoelectronic sectors, with leading suppliers investing in both capacity and process innovation to maintain competitive advantage.
Major Players and Strategic Partnerships (2025 Update)
The gallium nitride (GaN) epitaxial layer fabrication sector in 2025 is increasingly defined by the activities of leading manufacturers and strategic collaborations aimed at scaling production capacity, improving material quality, and accelerating device commercialization. Major players such as IQE plc, ams OSRAM, SÜNNOTECH, and EpiGaN (a SOITEC company) are at the forefront of these advancements.
- IQE plc has expanded its GaN epitaxy production capabilities in both the UK and US, following recent investments in new metal-organic chemical vapor deposition (MOCVD) reactors and automation technologies. The company continues to foster partnerships with leading foundries and device manufacturers to support the growing demand for GaN-on-Si and GaN-on-SiC wafers used in RF, power, and microLED applications (IQE plc).
- ams OSRAM has strengthened its position in GaN epitaxy for optoelectronic components, with strategic alliances focused on microLED and high-brightness LED markets. In 2025, the company announced further collaborations with display and automotive OEMs to co-develop next-generation GaN-based solutions (ams OSRAM).
- SÜNNOTECH and EpiGaN (SOITEC) have both ramped up their epitaxial layer production, leveraging proprietary processes to achieve improved uniformity and defect reduction. SÜNNOTECH, in particular, has announced new partnerships with Asian device manufacturers for high-frequency and power electronics, while EpiGaN continues its integration with SOITEC’s engineered substrate technologies (SÜNNOTECH; EpiGaN (a SOITEC company)).
- Strategic Partnerships have proliferated, with leading substrate suppliers like KYOCERA Corporation and SICC Co., Ltd. collaborating with epitaxy specialists to develop advanced templates for GaN growth on silicon carbide and sapphire, aiming to optimize yield and performance for next-generation devices.
Looking ahead, the sector is expected to see further consolidation and cross-border partnerships, particularly as the automotive, telecommunications, and consumer electronics industries drive higher production volumes and push for improved cost-performance ratios. The increasing alignment between material suppliers, epitaxy houses, and device manufacturers underscores the growing maturity and strategic importance of the GaN epitaxial layer fabrication ecosystem in 2025 and beyond.
Technology Advances in GaN Epitaxial Growth Processes
Gallium Nitride (GaN) epitaxial layer fabrication has experienced significant technological advancements as of 2025, driven by surging demand in power electronics, RF devices, and optoelectronics. The industry’s focus has been on improving material quality, throughput, and wafer size to meet requirements for high-performance devices. Metal-Organic Chemical Vapor Deposition (MOCVD) remains the dominant growth technique, but innovations in process control and reactor design are pushing the boundaries of scalability and uniformity.
One of the notable trends is the transition to larger wafer diameters, particularly the move from 4-inch to 6-inch and 8-inch substrates. This shift enhances productivity and reduces cost per device. For instance, ams OSRAM has ramped up production of GaN-on-Si epitaxial wafers at 8-inch scale to supply the automotive and consumer electronics sectors. Similarly, Nichia Corporation has invested in new MOCVD lines optimized for uniform GaN growth on large-area sapphire substrates, targeting both LED and power device markets.
Material quality improvements are evident through reduced dislocation densities and enhanced wafer uniformity. Techniques such as advanced in-situ monitoring, including reflectometry and real-time spectroscopic ellipsometry, are now standard in leading MOCVD platforms. Veeco Instruments and AIXTRON SE have reported reactor upgrades that enable precise control of layer thickness and doping, while minimizing defects and enabling repeatability at scale.
Alternative substrates are gaining traction. GaN-on-SiC remains crucial for high-frequency RF and power devices due to superior thermal conductivity, with Wolfspeed (formerly Cree) expanding its SiC substrate and GaN epitaxy capacity. GaN-on-Si is gaining ground for lower-cost, high-volume applications, with STMicroelectronics integrating GaN epitaxy processes in its mass production lines for power transistors.
Looking forward to the next few years, further integration of AI-driven process control and digital twins for epitaxy reactors is anticipated, aiming to enhance yield and accelerate development cycles. Collaborations between equipment makers and device manufacturers are set to strengthen, enabling rapid prototyping and faster commercialization of advanced GaN devices. As the technology matures, the focus will increasingly shift toward sustainability—reducing precursor consumption and energy usage within epitaxial growth processes.
Supply Chain Dynamics and Raw Material Sourcing
The supply chain for gallium nitride (GaN) epitaxial layer fabrication in 2025 is characterized by evolving dynamics in both raw material sourcing and wafer processing. The core raw materials—high-purity gallium, ammonia, and precursors for metal-organic chemical vapor deposition (MOCVD)—are sourced globally, but with increasing emphasis on regional security and vertical integration. Leading wafer manufacturers, such as ams OSRAM and Coherent Corp., have ramped up investments in backward integration to stabilize supply and ensure the purity required for high-performance GaN devices.
Amid geopolitical uncertainties and tightening export controls on strategic metals, concerns persist over the availability of gallium. After China’s 2023 export restrictions on gallium, the industry in 2025 has seen companies in North America, Japan, and Europe establish alternative refining routes and recycling programs. For example, Furukawa Electric has expanded its capacity for high-purity gallium recovery from industrial scrap, while Umicore leverages its expertise in specialty metals recycling to address potential bottlenecks.
On the epitaxy front, supply chain resilience is further bolstered by localizing MOCVD tool production and consumables supply. Veeco Instruments and Advanced Ion Beam Technology (AIBT) are examples of equipment manufacturers supporting regional supply chains, reducing dependency on long-haul imports of critical reactors and replacement components. These efforts are complemented by the expansion of specialty gas suppliers, such as Linde, who are building new distribution hubs for ammonia and carrier gases in proximity to major GaN fabrication clusters.
Looking ahead, the GaN epitaxial layer sector in 2025 and the coming years will continue to prioritize dual sourcing strategies, recycling, and domestic production. This is being accelerated by the push from governments to secure semiconductor supply chains, with incentives for local sourcing of critical materials and the construction of new purification and recycling facilities. The outlook suggests a gradual decoupling from single-region dependencies, resulting in a more resilient, responsive, and sustainable supply chain for GaN epitaxial layer fabrication.
Cost Drivers and Competitive Pricing Trends
The cost dynamics of Gallium Nitride (GaN) epitaxial layer fabrication in 2025 are shaped by advances in substrate technology, wafer size scaling, process optimization, and the competitive landscape among global suppliers. GaN epitaxy—typically performed via Metal-Organic Chemical Vapor Deposition (MOCVD)—remains a significant cost component in producing power electronics and RF devices, but industry trends are exerting downward pressure on prices while expanding capacity.
- Substrate and Wafer Size Evolution: The transition from 2-inch and 4-inch to 6-inch and 8-inch GaN-on-Si or GaN-on-SiC wafers is a primary cost driver. Larger wafers enable economies of scale, reducing per-device epitaxy costs. Leading suppliers like IQE plc and Episil Technologies Inc. have expanded their 6-inch and initiated 8-inch GaN epiwafer lines for both RF and power applications, responding to customer demand for lower cost-per-chip and higher throughput.
- Process Optimization and Throughput: MOCVD reactor efficiency, precursor utilization, and automation are crucial for cost competitiveness. Companies such as American Superconductor Corporation and Ammono S.A. are investing in process control and advanced reactor designs to improve uniformity and minimize wastage, further reducing the cost per wafer.
- Raw Material and Supply Chain Factors: The cost of high-purity precursors (e.g., trimethylgallium, ammonia) and substrate materials (Si, SiC, sapphire) remains sensitive to global supply-demand dynamics. Sumitomo Electric Industries, Ltd. and Mitsubishi Electric Corporation have increased vertical integration to stabilize material costs and supply reliability, helping buffer against market volatility.
- Pricing Trends and Competitive Landscape: With capacity additions in Asia, Europe, and North America, competitive pricing for GaN epitaxial wafers has intensified. Market leaders are offering tiered pricing based on wafer diameter, layer complexity, and volume orders. For example, ON Semiconductor and Cree, Inc. (now Wolfspeed) have announced new contracts and price adjustments in response to increased customer volume, signaling an ongoing shift toward commoditization for standard GaN epitaxial products.
Looking ahead to 2025 and the subsequent years, as demand from automotive, data center, and 5G sectors accelerates, further cost reductions are anticipated through continued wafer size scaling, improved reactor productivity, and tighter supplier-customer collaboration. These factors are expected to cement GaN’s position as a cost-effective platform for next-generation power and RF electronics.
Regulatory and Industry Standards (IEEE, JEDEC, etc.)
The regulatory and industry standards landscape for Gallium Nitride (GaN) epitaxial layer fabrication is evolving rapidly as the technology achieves wider adoption in power electronics, RF, and optoelectronic applications. In 2025, the industry focus is on ensuring device reliability, manufacturing consistency, and interoperability, which are critical as GaN moves into mainstream and safety-critical sectors such as automotive and telecom infrastructure.
Leading standardization bodies, including the IEEE and JEDEC, are at the forefront of establishing comprehensive guidelines for GaN-based materials and devices. IEEE has published documents such as IEEE 1653.6, which addresses testing and reliability assessment for wide bandgap semiconductors, including GaN, with ongoing workgroups updating protocols to reflect new epitaxial growth methods and device geometries expected in the next few years.
JEDEC, as of 2025, is actively refining its JC-70 committee standards, which focus on wide bandgap (WBG) power electronic conversion semiconductors. The JC-70.2 subgroup specifically addresses GaN and SiC reliability and test methods. Recent updates include enhanced guidelines for epitaxial wafer quality, surface defect density, and electrical parameter uniformity—parameters critical to high-yield mass production of GaN layers for discrete and integrated devices.
Beyond international standards bodies, industrial alliances and consortia are also shaping future directions. For instance, the Semiconductor Industry Association (SIA) and the SEMI Foundation are collaborating with manufacturers on best practices for epitaxial growth, metrology, and supply chain traceability. These efforts are particularly relevant as manufacturers such as Infineon Technologies and NXP Semiconductors scale up GaN wafer production, necessitating harmonized quality and test benchmarks across international fabs.
Looking ahead, the next few years are expected to bring further harmonization of standards for epitaxial defect density, wafer bow/warp, and contamination controls. This is in response to increasing device voltage ratings and the move to 200mm GaN-on-silicon substrates, which demand tighter process controls and standardized qualification methodologies. Cross-industry initiatives, such as the SIA’s EHS policy efforts, are also driving the development of environmental, health, and safety guidelines specific to GaN epitaxial processing.
As GaN epitaxial layer fabrication matures, the interplay between regulatory standards and industry-driven specifications will be critical to enabling reliable, scalable, and globally competitive manufacturing ecosystems by the late 2020s.
Emerging Opportunities: Automotive, 5G, and Quantum Devices
The fabrication of Gallium Nitride (GaN) epitaxial layers is positioned for significant technological and commercial advancements in 2025, primarily driven by emerging opportunities in automotive electronics, 5G communications, and quantum devices. The transition to electric vehicles and the proliferation of advanced driver-assistance systems (ADAS) are creating robust demand for high-efficiency, high-power GaN devices. Leading manufacturers such as Infineon Technologies AG and ROHM Co., Ltd. are expanding GaN epitaxy capacity and refining metal-organic chemical vapor deposition (MOCVD) processes to achieve lower defect densities and higher uniformity, critical for automotive-grade reliability.
In the telecommunications sector, the global rollout of 5G continues to accelerate the adoption of GaN-on-SiC and GaN-on-Si epitaxial wafers owing to their superior power density and frequency performance. Companies such as Wolfspeed, Inc. have announced plans to increase production of 150 mm and 200 mm GaN epitaxial wafers, which are tailored for next-generation 5G base stations and phased-array antennas. In 2025, the focus is on scaling up wafer diameters and improving yield, with several industry players investing in advanced in-situ monitoring and automation technologies to enhance throughput and reproducibility.
Quantum device development presents a frontier for GaN epitaxial layer innovation. As researchers seek materials with exceptional electron mobility and low noise characteristics, companies like imec are collaborating with semiconductor suppliers to develop ultra-high-purity, low-defect GaN layers for quantum computing and precision sensor applications. The integration of GaN with silicon and emerging substrates is under active investigation, with pilot production lines expected to ramp in the next few years to support prototype quantum hardware.
Looking ahead, the convergence of automotive electrification, 5G infrastructure expansion, and quantum technology research is expected to drive further investments in GaN epitaxial fabrication. Industry consortia such as Semiconductor Industry Association are advocating for supply chain resilience and public-private partnerships to secure access to high-quality GaN epitaxial wafers. As capital expenditures increase and process technologies mature, the period from 2025 onward is likely to witness both capacity expansions and breakthroughs in performance metrics, cementing GaN epitaxy’s role across these high-growth sectors.
Future Outlook: Disruptive Trends and Strategic Recommendations
The landscape for gallium nitride (GaN) epitaxial layer fabrication is poised for transformative growth and disruption in 2025 and the subsequent few years, driven by escalating demand in power electronics, RF devices, and next-generation optoelectronics. A notable trend is the widespread shift toward larger-diameter substrates—transitioning from 150 mm to 200 mm wafers—to enhance throughput and lower per-unit costs. Companies such as ams OSRAM and Ferrotec are at the forefront, investing in scaling up metal-organic chemical vapor deposition (MOCVD) and hydride vapor phase epitaxy (HVPE) technologies to meet these new technical demands.
In parallel, there is a marked acceleration in the development of native GaN substrates, which promise to reduce defect densities and enhance device performance compared to conventional sapphire or silicon carbide bases. IQE plc and Soitec are investing in proprietary fabrication routes—such as engineered substrates and quasi-bulk growth processes—to facilitate commercialization at scale. This evolution is expected to unlock new efficiencies for high-frequency, high-power, and automotive applications.
Strategically, a crucial recommendation for stakeholders is to increase R&D alliances with equipment providers. For instance, Veeco Instruments Inc. is collaborating closely with leading foundries to optimize MOCVD reactor designs specifically for thick GaN layers and defect mitigation. Similarly, suppliers like Akercheminc are advancing precursor chemistries to improve material quality and process reproducibility.
From an ecosystem perspective, the push toward sustainability and energy-efficient processing is intensifying. Manufacturers are investing in closed-loop gas recycling and advanced in-situ monitoring, as seen in initiatives by Oxford Instruments. This is increasingly relevant given growing regulatory scrutiny and the need for greener semiconductor supply chains.
In summary, the coming years will be defined by scaling to larger wafers, advances in native substrate technology, strategic collaborations across the supply chain, and a stronger focus on sustainability. Stakeholders who proactively engage with these disruptive trends—by investing in innovation and strategic partnerships—will be best positioned to capitalize on the expanding GaN epitaxial layer market.
Sources & References
- ams OSRAM
- STMicroelectronics
- Infineon Technologies
- EpiGaN
- Soitec
- pSemi
- Samsung Electronics
- Nitride Semiconductors Co., Ltd.
- ROHM Co., Ltd.
- Wolfspeed, Inc.
- OSRAM
- IQE plc
- Nichia Corporation
- Veeco Instruments
- AIXTRON SE
- Furukawa Electric
- Umicore
- Linde
- American Superconductor Corporation
- Sumitomo Electric Industries, Ltd.
- Mitsubishi Electric Corporation
- IEEE
- JEDEC
- Semiconductor Industry Association (SIA)
- NXP Semiconductors
- Wolfspeed, Inc.
- imec
- Ferrotec
- Oxford Instruments