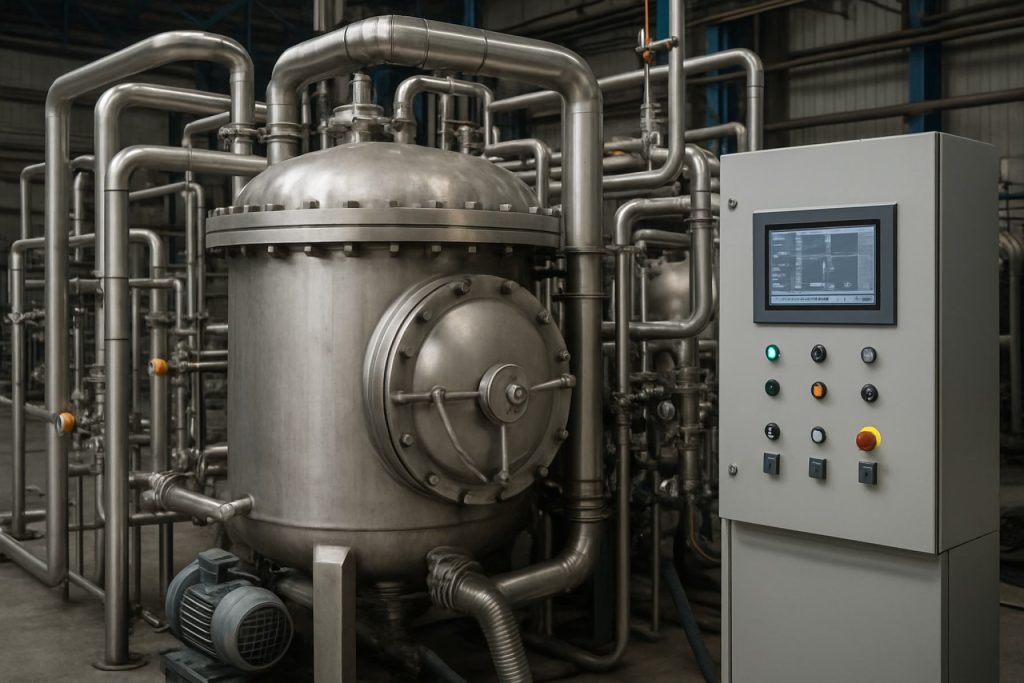
Table of Contents
- Executive Summary: Market Dynamics & Key Takeaways for 2025–2029
- Industry Overview: The Evolution and Fundamentals of Gas Quenching Systems Engineering
- Latest Technological Breakthroughs Shaping the Sector
- Leading Manufacturers and Strategic Partnerships (citing sources like secowarwick.com, ipsenusa.com, and linde.com)
- Market Size, Growth Trajectories, and 5-Year Forecasts
- Application Analysis: Automotive, Aerospace, Tooling, and Beyond
- Sustainability, Energy Efficiency, and Regulatory Developments
- Emerging Smart Controls, Automation, and Digital Monitoring Trends
- Competitive Landscape and Innovation Pipeline: Who’s Driving Change?
- Future Outlook: Opportunities, Risks, and Strategic Recommendations for Stakeholders
- Sources & References
Executive Summary: Market Dynamics & Key Takeaways for 2025–2029
The global gas quenching systems engineering sector is experiencing robust growth as industries seek greater control, efficiency, and sustainability in thermal processing technologies. As of 2025, the demand for advanced gas quenching solutions is being propelled by the automotive, aerospace, and tool manufacturing sectors, which require precise metallurgical properties and minimal distortion in heat-treated components. The transition from traditional oil quenching to gas-based systems—particularly those utilizing nitrogen and helium—reflects both environmental concerns and the need for improved process control.
Key market drivers in 2025 include tightening environmental regulations, the pursuit of carbon-neutral operations, and ongoing advancements in furnace and gas circulation technologies. For example, major manufacturers such as ALD Vacuum Technologies and Bodycote have expanded their portfolios with state-of-the-art vacuum furnaces equipped for high-pressure gas quenching, underpinning both energy efficiency and product quality. These technologies directly address industry challenges like part distortion, surface oxidation, and hazardous waste generation, positioning gas quenching as a preferred alternative in high-specification applications.
The market is also witnessing an uptick in demand for customized, turnkey gas quenching systems that integrate advanced control software, real-time process monitoring, and predictive maintenance features. Companies such as SECO/WARWICK are leading this trend, offering modular platforms that can be adapted to the evolving needs of manufacturers, including those transitioning towards Industry 4.0-compliant production environments. In parallel, suppliers like Air Liquide are investing in efficient gas supply and recycling solutions, reducing operational costs while aligning with sustainability objectives.
Regionally, the Asia-Pacific market continues to expand rapidly due to ongoing industrialization and a shift towards higher-value manufacturing. Meanwhile, North America and Europe remain innovation hubs, driven by strong automotive and aerospace industries and a focus on decarbonization. Leading OEMs are increasingly specifying gas quenching in their supply chains, accelerating adoption and spurring further R&D investment by system manufacturers.
- Gas quenching systems will see a compound annual growth rate (CAGR) in the mid- to high-single digits through 2029, supported by regulatory, technical, and economic factors.
- Next-generation systems will emphasize digital integration, energy efficiency, and flexible configurability to meet diverse industrial needs.
- Strategic collaborations among furnace builders, gas suppliers, and automation specialists are expected to drive innovation and secure competitive advantages.
In conclusion, the 2025–2029 outlook for gas quenching systems engineering is defined by technological progress, sustainability imperatives, and expanding end-user requirements, positioning the sector for continued growth and transformation.
Industry Overview: The Evolution and Fundamentals of Gas Quenching Systems Engineering
Gas quenching systems engineering has undergone significant transformation, reflecting both technological advances and intensified industrial demand for precise, energy-efficient thermal processing. Gas quenching, which utilizes high-pressure inert or active gases—such as nitrogen, hydrogen, or helium—to rapidly cool heat-treated metals, has become central to modern metallurgy, aerospace, and automotive manufacturing. Historically, oil quenching dominated the field, but the shift to gas-based systems over the past decade has been propelled by stricter environmental regulations, safety imperatives, and the quest for enhanced process control and component quality.
As of 2025, leading industry players are leveraging advanced gas circulation, pressure control, and heat exchanger technologies to optimize quenching uniformity and minimize distortion in critical components. For example, ALD Vacuum Technologies and Bodycote have engineered systems capable of high-pressure gas quenching (HPGQ) up to 20 bar, providing superior cooling rates for complex alloys while maintaining surface integrity. Such systems are increasingly integrated with automation and digital monitoring platforms, enabling real-time adjustment of gas flow, pressure, and temperature for improved repeatability and traceability.
Industry data from current installations highlight a pronounced trend toward larger, more flexible quenching chambers designed for variable batch sizes and part geometries. Companies like Ipsen have introduced modular furnace designs that allow for scalability and backward compatibility with existing processing lines. Furthermore, energy consumption remains a primary engineering focus: by utilizing heat recovery and optimized fan designs, manufacturers are reducing operational costs and environmental footprint.
In terms of gas selection, hydrogen is gaining ground due to its superior thermal conductivity, despite challenges with safety and infrastructure. Tenova has reported successful deployments of hydrogen-based quenching in aerospace-grade alloy processing, signaling a potential shift in preferred quench media over the next few years. Meanwhile, nitrogen remains prevalent for general-purpose applications, and helium is reserved for specialty alloys where ultra-fast quenching is critical.
Looking ahead, the outlook for gas quenching systems engineering is shaped by the convergence of Industry 4.0 concepts and sustainability mandates. The next three to five years will likely see continued adoption of predictive analytics, remote diagnostics, and closed-loop process controls. Major OEMs and heat treatment service providers are expected to further invest in greener, more adaptive systems—aligning with both customer quality requirements and tightening regulatory standards. As the sector evolves, collaborative research between equipment manufacturers and end-users will be vital for meeting the challenges of increasingly sophisticated material specifications and operational efficiency goals.
Latest Technological Breakthroughs Shaping the Sector
Gas quenching systems engineering is experiencing significant advancements in 2025, driven by the imperative for energy efficiency, process control, and sustainability within the heat treatment sector. A primary breakthrough is the integration of advanced sensor technologies and real-time process monitoring, enabling unprecedented control over quenching gas flow, temperature, and pressure. Companies such as ALINEA have introduced intelligent control systems that utilize machine learning algorithms to optimize gas usage and cooling rates, reducing energy consumption and improving part consistency.
Another major development is the widespread adoption of high-performance quenching gases, such as helium and nitrogen mixtures, which offer improved heat transfer characteristics compared to traditional pure nitrogen or oil-based systems. Linde has commercialized modular gas supply solutions that allow seamless switching between gas types and tailor quenching performance to specific alloy requirements, supporting the automotive and aerospace industries in achieving stringent metallurgical standards.
Vacuum furnace manufacturers are also pushing the envelope. SECO/WARWICK has recently launched new vacuum gas quenching systems featuring direct convection heating and multi-directional gas flow, significantly reducing cycle times while maintaining uniform quenching. These systems are increasingly equipped with Industry 4.0 connectivity, enabling predictive maintenance and remote diagnostics, which minimize downtime and improve operational reliability.
The sector is witnessing the integration of additive manufacturing (AM) with gas quenching, particularly for complex components requiring customized thermal profiles. Bodycote, a leading provider of heat treatment services, is expanding its capacity for precision gas quenching tailored to AM parts, ensuring targeted microstructural properties and distortion control.
Looking ahead, the outlook for gas quenching systems engineering is defined by further automation and digitalization. With ongoing investments in smart factories, embedded analytics, and eco-friendly gas recycling loops, the sector is poised for continued improvements in efficiency and environmental impact. As regulatory pressures on emissions and workplace safety intensify worldwide, manufacturers are expected to accelerate the adoption of closed-loop systems and low-global-warming-potential gas blends, positioning the industry for a transformative era through 2025 and beyond.
Leading Manufacturers and Strategic Partnerships (citing sources like secowarwick.com, ipsenusa.com, and linde.com)
The global landscape of gas quenching systems engineering in 2025 is shaped by the activities and collaborations of several leading manufacturers, whose innovations and strategic alliances are directly influencing technology adoption and industry standards. Key players such as SECO/WARWICK, Ipsen, and Linde are at the forefront, each leveraging their expertise to address evolving demands in automotive, aerospace, and toolmaking sectors.
SECO/WARWICK has continued to expand its market presence in 2025, with a strong emphasis on modular gas quenching systems tailored for flexible and efficient heat treatment processes. The company’s strategic focus includes enhancing their proprietary high-pressure gas quenching (HPGQ) furnaces, integrating intelligent control systems for energy optimization and process repeatability. Recent partnership announcements underscore SECO/WARWICK’s approach to collaborative innovation, such as joint development projects with automotive OEMs and research institutions to address rising requirements for part quality and throughput (SECO/WARWICK).
Ipsen remains a pivotal player in 2025, particularly in advanced vacuum furnace technology combined with high-pressure gas quenching. Ipsen’s ongoing investments in digitalization—via their PdMetrics® predictive maintenance platform and automation-ready systems—demonstrate their commitment to Industry 4.0 integration. Strategic alliances with global manufacturers, including multi-site supply agreements and technology transfers in Asia and Europe, have broadened Ipsen’s reach and strengthened its service network. Furthermore, Ipsen’s focus on environmentally sustainable solutions, such as nitrogen-based cooling, aligns with tightening emissions regulations and customer sustainability goals (Ipsen).
Linde, a world leader in industrial gases, continues to influence gas quenching systems engineering through its supply of high-purity process gases and its collaborations on process optimization. In 2025, Linde is advancing its work with leading furnace manufacturers to develop next-generation gas mixing and delivery technologies that improve uniformity and efficiency in quenching cycles. Linde’s strategic partnerships often involve joint R&D initiatives aimed at reducing cycle times and enhancing metallurgical outcomes, particularly for demanding applications in aerospace and automotive manufacturing (Linde).
Looking ahead, the next several years are expected to see further consolidation among equipment suppliers, deeper integration of digital technologies, and expanded cross-industry alliances. These trends are likely to accelerate the adoption of flexible, sustainable, and highly automated gas quenching solutions, cementing the leadership roles of SECO/WARWICK, Ipsen, and Linde within the sector.
Market Size, Growth Trajectories, and 5-Year Forecasts
The global market for gas quenching systems engineering is poised for sustained growth through 2025 and into the latter half of the decade, driven by increasing demand for advanced heat treatment solutions in automotive, aerospace, and high-performance manufacturing sectors. Gas quenching, a process wherein inert gases (commonly nitrogen, argon, or helium) are used to rapidly cool metals, is favored for its ability to achieve precise metallurgical properties and minimize distortion compared to traditional oil quenching. As manufacturing processes become more sophisticated and environmental regulations tighten, the adoption of gas quenching systems is projected to accelerate.
In 2025, leading manufacturers such as ALDO UNION, Bodycote, and Ipsen are reporting increased deployment of gas quenching furnaces—both as standalone systems and as integrated modules within automated heat treatment lines. For instance, Ipsen notes a significant uptick in orders for vacuum furnaces equipped with high-pressure gas quenching (HPGQ) capabilities, particularly among Tier 1 automotive suppliers seeking to meet stringent part quality and throughput requirements.
The market expansion is further supported by ongoing investments in R&D and the adoption of digital controls to optimize gas usage, energy efficiency, and process repeatability. Bodycote highlights the trend toward larger batch sizes and hybrid system configurations, which allow for the processing of diverse materials with minimal cross-contamination and maximized furnace utilization.
From a regional perspective, Asia-Pacific is anticipated to represent the fastest-growing segment, spurred by automotive production hubs in China, India, and Southeast Asia, while Europe and North America continue to modernize legacy heat treatment infrastructure. Tenova has recently announced new installations of large-scale gas quenching systems in both Germany and the United States, demonstrating the cross-regional momentum in system upgrades.
- By 2025, the global installed base of industrial gas quenching systems is projected to increase by 7–9% year-over-year, with revenues from new equipment, retrofits, and service contracts surpassing pre-pandemic levels.
- Over the next five years, digitalization (e.g., IoT-enabled controls, predictive maintenance) is expected to become standard in new system deliveries, enhancing uptime and productivity for end users (Ipsen).
- Environmental considerations—especially the reduction of quench oils and VOC emissions—will further accelerate the transition to gas-based quenching in regulated industries.
Looking ahead, the market outlook for gas quenching systems engineering remains robust, with innovation centering on energy savings, process automation, and the capability to handle increasingly complex component geometries. Strategic collaborations between furnace manufacturers, industrial gas suppliers, and end users are likely to shape the competitive landscape through 2030.
Application Analysis: Automotive, Aerospace, Tooling, and Beyond
Gas quenching systems engineering continues to play a pivotal role in enhancing component performance and efficiency across key industries such as automotive, aerospace, and tooling, with applications rapidly expanding into new sectors as of 2025. The adoption of advanced gas quenching technologies is driven by the need for precise thermal processing, improved product quality, and compliance with stringent environmental and safety standards.
In the automotive sector, the shift toward electric vehicles and lightweight components has spurred demand for high-strength, distortion-free parts. Gas quenching, particularly using nitrogen and helium, is increasingly preferred over traditional oil quenching for its ability to minimize part distortion and contamination. Leading furnace manufacturers such as ALDO UNION S.p.A. and Bodycote highlight the deployment of vacuum furnaces with high-pressure gas quenching to treat gears, shafts, and critical drivetrain components. This technology supports the production of precision parts for electric drivetrains and transmission systems, a trend expected to intensify with ongoing electrification initiatives through 2027.
Aerospace manufacturers are equally reliant on gas quenching systems to meet strict specifications for turbine blades, landing gear, and structural parts. The sector’s requirement for superior fatigue resistance and dimensional stability has led to widespread use of high-pressure gas quenching. Companies such as SECO/WARWICK and Ipsen offer high-pressure vacuum furnaces tailored for aerospace alloys, with ongoing innovations in multi-chamber and hybrid systems to boost throughput and flexibility. The outlook for 2025-2028 indicates accelerated adoption, especially as new aircraft designs demand tighter tolerances and lightweight, high-performance materials.
In the tooling industry, where precision and wear resistance are paramount, gas quenching enables the hardening of complex dies, molds, and cutting tools with minimal risk of cracking or dimensional change. Park Thermal International and EcoFurnace provide systems optimized for rapid quenching cycles and uniform cooling, supporting manufacturers in meeting just-in-time delivery demands.
Beyond these established industries, gas quenching systems are now being integrated into sectors like additive manufacturing, medical device production, and precision electronics. As component miniaturization and performance requirements intensify, system integrators are offering modular, automation-ready solutions that enable scalable and repeatable heat treatment processes.
Looking ahead, the convergence of Industry 4.0 technologies—including real-time process monitoring and data analytics—will further enhance process control and energy efficiency in gas quenching systems. By 2028, broader adoption is expected across both traditional and emerging applications, underpinned by continuous innovation from industry leaders and the evolving needs of high-precision manufacturing.
Sustainability, Energy Efficiency, and Regulatory Developments
Engineering of gas quenching systems is undergoing significant transformation in 2025, driven by heightened sustainability demands, energy efficiency imperatives, and evolving regulatory frameworks. The metal heat treatment sector, historically reliant on energy-intensive processes and hazardous quenching media, is shifting towards engineered gas quenching solutions—primarily utilizing gases such as nitrogen, helium, and argon—to achieve both technical and environmental goals.
A primary sustainability driver is the reduction of greenhouse gas emissions and hazardous waste. Gas quenching systems eliminate the need for oil and polymer quenchants, reducing fire risks and toxic byproducts, and facilitating cleaner operations. Recent system designs by companies such as ALD Vacuum Technologies and Bodycote emphasize closed-loop gas recirculation, heat recovery, and integration with renewable energy sources. These systems are increasingly equipped with real-time analytics and advanced controls to optimize gas flow, minimize consumption, and reduce overall carbon footprint.
Energy efficiency is another focal point. Gas quenching typically requires higher initial energy input to achieve sufficient cooling rates, especially with high-pressure applications, but modern systems offset this through high-efficiency compressors, regenerative heat exchangers, and variable-speed drives. For example, Ipsen has introduced gas quenching furnaces with adaptive cooling and power management, leading to reported energy savings of up to 20% compared to legacy systems. Likewise, Tenova has developed modular, energy-efficient gas quenching lines aimed at reducing power consumption per treated ton.
Regulatory developments are also shaping engineering priorities. The European Union’s Industrial Emissions Directive and the U.S. Environmental Protection Agency’s Clean Air Act are increasingly targeting emissions from industrial furnaces, including those used in heat treating and quenching processes. Compliance now requires not only emission controls, but also robust reporting and traceability. Companies such as SECO/WARWICK have responded by integrating emission monitoring and digital compliance tools into their gas quenching systems, anticipating stricter standards expected in the EU and North America by 2027.
Looking ahead, further improvements are anticipated in gas recycling efficiency, real-time emissions monitoring, and AI-driven process optimization. Industry collaborations, such as those between furnace manufacturers and gas suppliers like Air Liquide and Linde, are accelerating the development of sustainable gas blends and circular solutions for quenching gases. As regulations tighten and end-users demand greener supply chains, the next few years will likely see accelerated adoption of advanced, energy-efficient, and compliant gas quenching systems in global heat treatment operations.
Emerging Smart Controls, Automation, and Digital Monitoring Trends
The landscape of gas quenching systems engineering is experiencing rapid transformation, driven by the integration of smart controls, advanced automation, and digital monitoring tools. As industries such as automotive, aerospace, and precision manufacturing demand higher reliability and tighter process control, gas quenching solutions in 2025 are increasingly characterized by connected, intelligent technologies.
A prominent trend is the adoption of IIoT (Industrial Internet of Things) platforms that enable real-time monitoring and remote diagnostics of quenching processes. Major system manufacturers are embedding sensor networks and edge computing devices directly into their equipment, facilitating the collection of detailed process data—ranging from quench gas flow rates and pressure to chamber temperatures and part surface cooling profiles. Companies such as SECO/WARWICK have introduced gas quenching systems with digital control panels, advanced PLC integration, and cloud-based analytics for predictive maintenance and process optimization.
Automation is also advancing, with robotic material handling and automated loading/unloading now standard in new installations. For example, Bodycote has deployed fully automated gas quenching lines in several facilities, achieving higher throughput, reduced operator intervention, and improved process repeatability. These systems are complemented by SCADA (Supervisory Control and Data Acquisition) platforms that centralize control and monitoring, allowing operators to manage multiple furnaces and quenching modules from a unified interface.
Digital twins—virtual replicas of physical quenching systems—are emerging as a powerful tool for process simulation, optimization, and troubleshooting. Solutions offered by Aldo Union and other international furnace manufacturers leverage real-time data feeds and advanced modeling, enabling users to forecast system performance and make data-driven adjustments without interrupting production.
- Enhanced quality assurance: Integrated sensors and analytics ensure part-to-part consistency and allow for rapid identification of process deviations.
- Energy and resource efficiency: Smart controls optimize gas consumption and cycle times, aligning with sustainability targets.
- Remote service and support: Through secure digital platforms, engineers can diagnose and resolve issues without on-site visits—a critical advantage in global operations.
Looking toward the next few years, the sector is expected to further embrace AI-driven process control and even deeper integration with enterprise manufacturing systems. As regulatory and customer demands for traceability and zero-defect manufacturing intensify, the role of smart, automated, and digitally monitored gas quenching systems will become increasingly central to heat treatment operations worldwide.
Competitive Landscape and Innovation Pipeline: Who’s Driving Change?
The competitive landscape in gas quenching systems engineering is experiencing significant transformation in 2025, propelled by evolving industrial requirements, sustainability imperatives, and rapid technological advancements. Key players are actively investing in R&D to optimize system efficiency, reduce environmental impact, and enhance automation. The market is characterized by the interplay of established furnace manufacturers, specialist quenching technology developers, and industrial gas suppliers, each contributing unique innovations.
Leading the charge are companies like ALD Vacuum Technologies and Bodycote, who have introduced advanced vacuum furnace technologies and modular gas quenching solutions tailored for aerospace, automotive, and precision engineering sectors. ALD Vacuum Technologies recently rolled out its latest generation of high-pressure gas quenching systems, which leverage precise process control algorithms and energy recovery modules to boost cooling rates while minimizing gas consumption.
Automation and digital integration are key innovation drivers. Linde plc is pioneering in-line process analytics and remote monitoring solutions, enabling real-time adjustment of gas flow and pressure for improved repeatability and part quality. Meanwhile, Air Liquide is expanding its portfolio of gas supply and management systems, focusing on nitrogen and helium blends that deliver superior quench uniformity with lower carbon footprints.
Emerging entrants and niche specialists are also reshaping the field. SECO/WARWICK continues to innovate with hybrid cooling systems combining gas and convection techniques, offering improved flexibility for complex alloys and geometries. Collaborations between furnace OEMs and digital technology firms, such as those initiated by Tenova, are accelerating the adoption of AI-driven predictive maintenance and process optimization tools.
Looking forward, the next few years will see increased emphasis on sustainability, with major suppliers committing to carbon-neutral operations and recyclable gas loops. The deployment of Industry 4.0-compatible systems will further enhance competitiveness, allowing users to achieve tighter process tolerances and lower operational costs. As regulatory pressures mount and end-users demand higher efficiency, the innovation pipeline is expected to remain robust, with dynamic competition continuing to drive progress in gas quenching systems engineering.
Future Outlook: Opportunities, Risks, and Strategic Recommendations for Stakeholders
The future outlook for gas quenching systems engineering in 2025 and the subsequent years is shaped by increasing demands for advanced materials, evolving regulatory frameworks, and the ongoing drive toward energy efficiency and automation. Opportunities abound in several key areas, particularly as automotive, aerospace, and tool manufacturing sectors continue to seek faster, cleaner, and more controllable heat treatment solutions. Strategic investments are expected to focus on the integration of digital control systems and environmentally friendly quenching gases, responding both to operational efficiency goals and tightening emissions standards.
- Opportunities: The transition away from oil-based quenching toward high-pressure gas quenching (HPGQ) is accelerating, driven by the need to minimize distortion and improve the mechanical properties of critical components. Companies such as Air Products and Chemicals, Inc. and Linde plc are actively expanding their gas supply and process control solutions to meet growing demand. Additionally, the rise in adoption of Industry 4.0 technologies—such as real-time data analytics, remote monitoring, and predictive maintenance—offers new prospects for system integrators and OEMs. Enhanced process automation and quality control are expected to yield substantial cost savings and process reliability.
- Risks: The industry faces risks associated with initial capital investment, particularly for small and mid-sized OEMs that may struggle to justify the shift from traditional oil quenching. Safety concerns related to the handling of high-pressure gases and the need for advanced operator training also remain prominent. Moreover, availability and cost fluctuations of industrial gases, particularly helium and high-purity nitrogen, could impact operational budgets. Regulatory changes around greenhouse gas emissions or workplace safety may require rapid adaptation of gas supply and exhaust management systems.
- Strategic Recommendations: Stakeholders are advised to invest in flexible, modular gas quenching systems capable of handling a variety of part sizes and alloys, as exemplified by recent product lines from Bodycote plc and Ipsen. Collaboration with industrial gas suppliers for customized delivery and recovery solutions can mitigate supply risks and reduce operational costs. Emphasis should also be placed on workforce development, ensuring operators are trained in both safety and digital process management. Finally, close monitoring of evolving international standards and local regulations will be critical for long-term compliance and global market access.
As sustainability and digital transformation continue to shape the industrial landscape, gas quenching system engineering is poised for significant evolution, offering both challenges and substantial rewards for proactive stakeholders over the coming years.