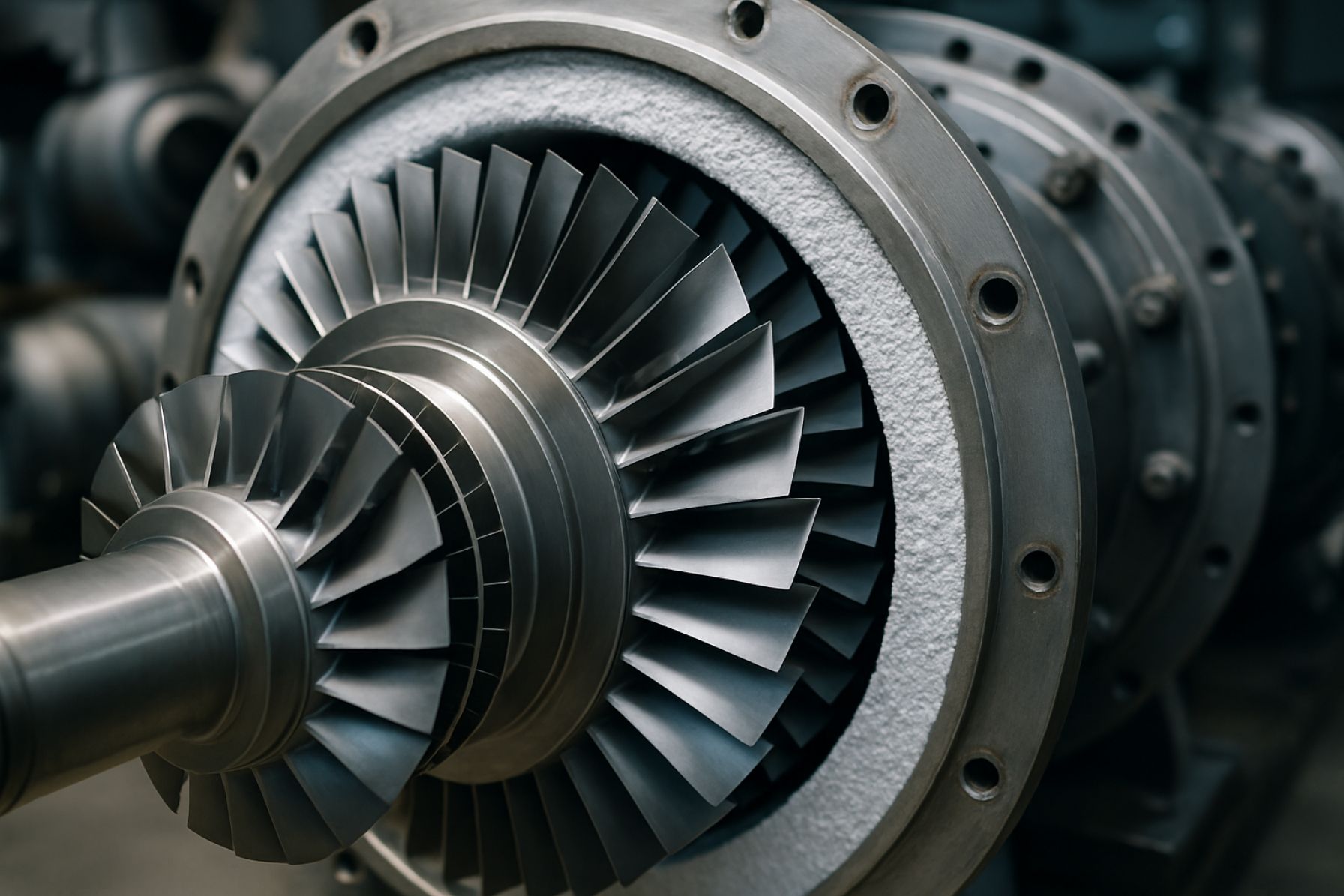
Abradable Coatings for Turbomachinery: 2025’s Game-Changer and Multi-Billion Dollar Growth Opportunity Revealed!
Table of Contents
- Executive Summary: 2025 Snapshot & Strategic Insights
- Market Size, Growth Forecasts, and Key Global Regions (2025–2030)
- Technology Overview: Abradable Coating Types and Material Innovations
- Emerging Application Trends in Gas Turbines, Compressors, and Jet Engines
- Competitive Landscape: Leading Players and Recent Partnerships
- Regulatory, Environmental, and Efficiency Standards Impacting Adoption
- Breakthrough R&D: Nanocoatings, Additive Manufacturing, and Smart Materials
- Supply Chain Dynamics: Raw Materials, Manufacturing, and Integration Challenges
- Customer Perspectives: OEM and MRO Requirements, and Case Studies
- Future Outlook: Disruptive Technologies, Sustainability, and Next-Gen Opportunities
- Sources & References
Executive Summary: 2025 Snapshot & Strategic Insights
In 2025, abradable coatings for turbomachinery are positioned as a critical enabling technology for efficiency, reliability, and emissions reduction in aerospace and industrial gas turbines. These specialized coatings are applied to compressor and turbine casings, providing a sacrificial, low-damage interface that allows rotating blades to run with minimal clearance, directly improving performance parameters such as fuel efficiency and power output. Driven by stringent regulatory demands and the relentless push for higher turbine efficiency, adoption of advanced abradable coatings is accelerating across the sector.
Major OEMs and material suppliers have intensified R&D and commercialization efforts. For example, GE Aerospace continues to develop and implement next-generation abradable coatings, such as thermally sprayed ceramics and metal composites, which support their latest engine platforms. Safran has highlighted the integration of abradable solutions in its LEAP engine program, enabling tighter clearances and contributing to double-digit improvements in fuel burn and reduced lifecycle maintenance. Similarly, Pratt & Whitney emphasizes abradable sealing systems in its geared turbofan and military engine lines, targeting enhanced durability and reduced environmental impact.
Suppliers such as H.C. Starck Solutions and Oerlikon are expanding production capacities and portfolios. Oerlikon’s Surface Solutions division reports increased demand for tailor-made abradable coatings, including metallic, ceramic, and composite formulations, to address both legacy engine upgrades and new-build programs. Advanced manufacturing processes—such as plasma spraying, high-velocity oxy-fuel (HVOF), and cold spray—are being leveraged for precise, repeatable application, resulting in coatings with optimized erosion resistance and controlled ablation characteristics.
Looking ahead, the outlook for abradable coatings remains robust. The global push for net-zero aviation, exemplified by initiatives from Rolls-Royce and Safran, will maintain premium on sealing technologies that enable higher pressure ratios and lower specific fuel consumption. Electrification trends and hybrid propulsion concepts, while disruptive, are expected to further diversify demand for abradable solutions in smaller, faster-rotating turbomachinery. Regulatory compliance, such as stricter NOx and CO2 standards, will also sustain investment in coatings that permit aggressive engine architectures.
- Key 2025 priorities include materials innovation (e.g., nanostructured ceramics, self-lubricating matrices), accelerated qualification cycles, and digital twin integration for predictive coating performance.
- Strategic partnerships between OEMs, suppliers, and research institutions are expected to intensify, supporting rapid prototyping and shortening time-to-market for new coating systems.
In summary, abradable coatings are a strategic pillar for next-generation turbomachinery, with 2025 marking a phase of scaling adoption, advanced materials integration, and alignment with industry-wide sustainability and efficiency targets.
Market Size, Growth Forecasts, and Key Global Regions (2025–2030)
The market for abradable coatings in turbomachinery is anticipated to experience robust growth from 2025 through 2030, driven by ongoing advancements in gas turbine efficiency, stricter emissions regulations, and the increasing global demand for both commercial and military aviation, as well as energy generation. Abradable coatings, which are engineered sacrificial layers applied to the inner casings or blade tips of turbines and compressors, enable tighter clearances, reduce leakage, and thereby improve overall engine performance and fuel efficiency.
Leading manufacturers, such as GE Power, Safran, and Sulzer, continue to invest in the development and deployment of abradable coating technologies for both new engines and the aftermarket. For instance, GE Power integrates advanced abradable coatings in its gas turbines to achieve higher operational efficiency and lower lifecycle costs. Similarly, Safran employs proprietary abradable seal coatings across its civil and military engine platforms to support the next generation of propulsion systems.
Geographically, the demand for abradable coatings is most pronounced in North America, Europe, and Asia-Pacific. The United States remains a key market due to the presence of major aerospace OEMs and a large installed base of gas turbines for both aviation and power generation. Europe, with its focus on sustainability and high-performance aerospace engineering, also presents significant opportunities, particularly with engine manufacturers such as Rolls-Royce and MTU Aero Engines incorporating advanced abradable materials in their new product lines. In Asia-Pacific, rapid growth in air travel and energy infrastructure, especially in China and India, is expected to drive increased adoption of high-performance abradable coatings by regional players such as IAE International Aero Engines and Mitsubishi Heavy Industries.
Looking ahead, the market outlook for 2025–2030 remains positive, with double-digit annual growth rates expected in certain segments, particularly those related to next-generation, fuel-efficient gas turbines and sustainable aviation. The continued push for decarbonization, alongside the need for maintenance optimization and operational reliability, will likely ensure sustained demand for abradable coatings globally. The emergence of new materials such as ceramic-based and environmental barrier abradable coatings is expected to further expand application areas and performance thresholds in the coming years.
Technology Overview: Abradable Coating Types and Material Innovations
Abradable coatings are a critical technology for enhancing the efficiency and reliability of turbomachinery, including gas turbines, compressors, and jet engines. These coatings are engineered to be sacrificial, allowing rotating components to cut into the coating during operation, thereby minimizing clearance gaps and leakage losses. As of 2025, industry development is focused on advancing the performance, durability, and application methods of abradable coatings, with significant innovations in both material composition and deposition technologies.
The primary types of abradable coatings in current use include metallic, ceramic, and polymer-based systems. Metallic abradables, typically aluminum- or nickel-based alloys, are favored in lower temperature compressor sections. For example, Oerlikon Metco offers a portfolio of nickel-graphite and aluminum-silicon based abradable coatings designed for gas turbine compressor applications. These materials are engineered to maintain structural integrity while providing the necessary abradability for blade tip rubbing.
At higher temperatures, such as in turbine sections, ceramic-based abradable coatings are increasingly prevalent. These coatings, often composed of yttria-stabilized zirconia or other complex oxides, are valued for their thermal stability and ability to withstand aggressive operating environments. Praxair Surface Technologies (now part of Linde) has developed advanced ceramic abradable systems that offer improved erosion resistance and longer service life, addressing a key industry demand for reduced maintenance intervals.
Polymer-based abradables, though less common in high-temperature zones, are still used in specific low-temperature compressor and auxiliary applications. Material innovation in this segment is focused on developing composites that offer improved wear resistance while maintaining the desired abradability and low density. H.C. Starck Solutions provides polymer-metal composite abradables for specialized turbomachinery requirements.
A major trend shaping the outlook for 2025 and beyond is the integration of additive manufacturing (AM) and advanced thermal spray techniques to deposit abradable coatings with greater precision and tailored microstructures. Companies such as Bodycote are investing in next-generation plasma spray and high-velocity oxy-fuel (HVOF) processes to enable coatings with enhanced porosity control and customized performance characteristics.
Looking ahead, the industry is expected to see increased adoption of multi-layer and functionally graded abradable coatings, which combine different material phases to optimize performance across a range of operating conditions. The ongoing transition to higher-efficiency, lower-emission turbomachinery is driving demand for coatings that can withstand more extreme environments, pushing material science innovation and collaboration between OEMs and coating suppliers. The outlook for 2025 and the next several years is robust, with continued advances in both materials and deposition technologies set to further enhance the role of abradable coatings in turbomachinery performance and reliability.
Emerging Application Trends in Gas Turbines, Compressors, and Jet Engines
Abradable coatings play a critical role in advancing the efficiency and reliability of turbomachinery, particularly in gas turbines, compressors, and jet engines. In 2025, these coatings are increasingly being adopted as integral design elements to minimize tip clearances, enhance sealing, and accommodate tighter manufacturing tolerances. The ongoing demand for higher efficiency and lower emissions in both aerospace and power generation sectors continues to drive innovation and application of abradable coatings.
A notable trend is the shift towards next-generation abradable coating materials that can withstand higher operating temperatures and more aggressive environments, matching the advancements in turbine engine materials and designs. For instance, GE Aerospace and Rolls-Royce are incorporating advanced ceramic-based abradable coatings in their latest engine platforms to support higher turbine inlet temperatures and extended service intervals, crucial for modern fuel-efficient engines. These coatings enable tighter tip clearances, directly contributing to improved engine efficiency and reduced fuel consumption.
On the industrial gas turbine front, companies like Siemens Energy are deploying abradable coatings in both new and retrofit applications, focusing on optimizing compressor and turbine sealing. The company’s recent projects have highlighted the role of plasma-sprayed abradable coatings in enhancing component lifespan and reliability, especially in high-duty cycles. Similarly, Sulzer offers advanced thermal spray and abradable seal solutions for turbomachinery, reporting increased adoption in maintenance, repair, and overhaul (MRO) activities due to the coatings’ ability to restore and protect critical surfaces.
Another trend is the integration of abradable coatings with digital twin and sensor technologies. These smart coatings, developed in collaboration with organizations like Safran, are being evaluated for their ability to provide real-time feedback on wear and clearance, enabling predictive maintenance and further reducing unplanned downtime. Early field data from ongoing demonstrator programs suggest improved operational availability and lifecycle cost savings.
Looking ahead to the next few years, the trajectory points toward broader adoption of environmentally optimized abradable coatings, including those with reduced volatile organic compounds (VOC) and improved recyclability. With stricter regulatory and sustainability requirements emerging, coating manufacturers such as Oerlikon Metco are investing in new compositions and application methods to meet these goals.
Overall, the increasing adoption of abradable coatings in turbomachinery is expected to accelerate through 2025 and beyond, driven by efficiency mandates, sustainability targets, and the digitalization of maintenance and operation practices.
Competitive Landscape: Leading Players and Recent Partnerships
The competitive landscape for abradable coatings in turbomachinery is defined by a handful of established global players, several of whom have expanded their portfolios and partnerships in the run-up to 2025. These coatings, vital for improving compressor and turbine efficiency by controlling clearances and minimizing wear, are seeing growing demand due to stricter efficiency and emissions regulations in both aerospace and energy sectors.
Key manufacturers such as GE Aerospace, Safran, Pratt & Whitney, and Rolls-Royce remain dominant, leveraging in-house coating technologies for their own engine programs. In recent years, these OEMs have focused on further integration of advanced abradable coatings, such as ceramic and metallic matrix composites, to support next-generation engine efficiency targets.
Specialized coating suppliers also play a crucial role. Oerlikon, through its Surface Solutions division, continues to invest in thermal spray and physical vapor deposition (PVD) technologies tailored for abradable applications in both aerospace and industrial gas turbines. The company’s 2023 expansion of its coating center network in North America underlines ongoing demand and customer proximity goals.
Bodycote is another leading provider, offering a range of abradable coatings for compressor and turbine parts. In 2024, Bodycote announced a collaboration with Siemens Energy to develop next-generation turbine coatings aiming for enhanced thermal stability and erosion resistance, with plans for pilot deployment in 2025.
On the materials side, H.C. Starck Solutions and Oerlikon Metco continue to innovate in powder feedstock, supporting the customization of abradable coatings for specific engine requirements. Their collaboration with major OEMs and repair shops ensures a steady technology transfer from material science to applied turbomachinery solutions.
As demand for sustainable aviation and power generation grows, partnerships between OEMs, coating specialists, and material suppliers are expected to deepen. Strategic alliances, like the Safran-Airbus initiative on sustainable propulsion, often include joint development of new abradable materials to support higher operating temperatures and fuel efficiency. The outlook for 2025 and beyond suggests increasing consolidation and cross-sector collaboration to accelerate the adoption of next-generation abradable coatings in turbomachinery.
Regulatory, Environmental, and Efficiency Standards Impacting Adoption
The adoption of abradable coatings in turbomachinery is increasingly shaped by evolving regulatory, environmental, and efficiency standards. As of 2025, global and regional emissions regulations—such as the International Civil Aviation Organization’s (ICAO) CAEP standards for aircraft engines and the European Union’s Industrial Emissions Directive—are placing pressure on engine manufacturers to reduce fuel consumption and emissions. Abradable coatings, which enable tighter clearances between rotating and stationary components, play a crucial role in achieving these objectives by minimizing leakage and improving efficiency.
In the aerospace sector, stricter efficiency mandates and carbon reduction targets have accelerated the integration of advanced abradable coatings in both new engines and retrofits. For example, GE Aerospace and Rolls-Royce have highlighted the role of advanced sealing systems—including abradable coatings—in their next-generation engine programs to help meet regulatory-driven efficiency standards. The U.S. Environmental Protection Agency (EPA) has also aligned its aircraft engine emission standards with ICAO requirements, reinforcing the demand for high-performance sealing solutions.
Environmental considerations are also influencing the selection of coating materials and application processes. There is a notable shift away from traditional materials that contain hazardous elements, such as hexavalent chromium, toward environmentally benign alternatives. Companies like Oerlikon Metco and H.C. Starck Solutions are actively developing and commercializing coatings that comply with evolving REACH and OSHA regulations, focusing on sustainability and occupational safety.
Standardization efforts are intensifying, with organizations such as the SAE International and ASME updating technical guidelines for turbomachinery coatings to account for new regulatory and performance demands. These updates provide clearer frameworks for manufacturers and operators, supporting more rapid and consistent adoption of advanced abradable technologies.
Looking ahead to the next few years, the convergence of regulatory, environmental, and efficiency drivers is expected to spur further innovation in abradable coating formulations and application techniques. The industry anticipates broader use of digital twin technologies and lifecycle monitoring to validate coating performance against increasingly stringent standards. In summary, regulatory and sustainability imperatives will remain primary forces accelerating the adoption and evolution of abradable coatings across turbomachinery segments in the near future.
Breakthrough R&D: Nanocoatings, Additive Manufacturing, and Smart Materials
The landscape of abradable coatings for turbomachinery is undergoing significant transformation in 2025, marked by advances in nanocoatings, additive manufacturing, and smart materials. These technologies are being leveraged to address the increasingly stringent requirements for efficiency, durability, and environmental compliance in gas turbines and aeroengines.
Nanostructured coatings are at the forefront of current R&D, offering enhanced control over porosity, hardness, and abradability. In 2024, Oerlikon Metco announced developments in its Metco™ abradable product line, utilizing engineered microstructures to optimize thermal stability and minimize wear on both rotating blades and stationary shrouds. These coatings employ precisely selected metallic and ceramic materials at the nanoscale to deliver tailored erosion and ablation characteristics, critical for modern high-pressure compressors and turbines.
Additive manufacturing (AM) is also influencing how abradable coatings are designed and applied. GE Additive has continued investment in powder bed fusion and directed energy deposition techniques, enabling the integration of abradable segments directly into metallic components. This approach reduces lead times and enhances the repairability of turbine hardware, while allowing for customized coating architectures that are difficult to achieve with conventional plasma spraying. Notably, AM enables rapid prototyping of new abradable compositions, expediting the iterative development cycle.
Smart materials are another area of active research, with self-healing or condition-responsive abradable coatings gaining traction. Safran has reported progress in embedding sensing elements into abradable coatings to monitor real-time wear and blade tip clearance. These smart coatings are expected to offer predictive maintenance data, reducing unplanned downtime and extending intervals between overhauls.
The next few years are expected to see further industrialization of these R&D breakthroughs. OEMs such as Rolls-Royce and Pratt & Whitney are actively collaborating with coating suppliers to qualify new nanostructured and additively manufactured abradable materials for forthcoming engine platforms, targeting both civil aviation and energy sectors. These efforts are aligned with broader goals to improve fuel efficiency and reduce lifecycle emissions.
- Nanocoatings are enhancing abradability and durability in critical turbomachinery components (Oerlikon Metco).
- Additive manufacturing is enabling integrated, custom abradable segments and speeding up new material qualification (GE Additive).
- Smart abradable coatings with embedded sensors are being field-tested for predictive maintenance (Safran).
Overall, these breakthrough R&D initiatives promise to set new benchmarks for turbine reliability, efficiency, and operational intelligence as they enter mainstream adoption by 2026 and beyond.
Supply Chain Dynamics: Raw Materials, Manufacturing, and Integration Challenges
The supply chain for abradable coatings in turbomachinery is undergoing significant transformation as the industry adapts to new material demands, manufacturing advances, and integration challenges—particularly as engine efficiency and emissions requirements tighten for aerospace and energy applications in 2025 and beyond. The market is characterized by a consolidation of suppliers of critical raw materials, a push for advanced manufacturing techniques, and heightened collaboration between OEMs and coating specialists to ensure durability and performance.
- Raw Materials: Key ingredients for abradable coatings—such as nickel-graphite composites, ceramic matrices, and polymeric binders—are sourced from a limited number of specialized suppliers. Volatility in the supply of high-purity nickel and rare ceramics has led to increased scrutiny around sourcing strategies. For example, H.C. Starck Solutions and Höganäs AB are leading suppliers of metal powders tailored for aerospace coatings, highlighting the importance of robust supplier relationships and contingency planning as demand fluctuates.
- Manufacturing Advances: The transition from traditional air plasma spray (APS) to more precise processes such as high-velocity oxy-fuel (HVOF) and suspension plasma spray (SPS) is accelerating. These methods offer improved microstructure control, enhancing the abradability and lifespan of coatings. Oerlikon Balzers and Bodycote are investing in new equipment and digital process monitoring to increase throughput and consistency, responding to OEM requests for higher reproducibility and faster turnaround.
- Integration Challenges: Customizing coatings to specific engine designs remains a bottleneck, requiring close engineering collaboration and extensive validation. The integration of abradable coatings into newer turbine architectures, such as those with tighter clearances and higher operating temperatures, is particularly challenging. Companies like Praxair Surface Technologies are working with OEMs to develop proprietary blends that withstand harsher environments while balancing machinability and abradability. The rollout of next-generation engines by Rolls-Royce and GE Aerospace is driving demand for coatings with precisely engineered properties and rigorous qualification cycles.
Looking ahead, heightened sustainability requirements and ongoing geopolitical uncertainties may further impact raw material sourcing and cost structures. The industry’s response—manifesting in new supplier partnerships, the adoption of digital quality assurance, and localized manufacturing—will define the agility and competitiveness of abradable coating supply chains through 2025 and the following years.
Customer Perspectives: OEM and MRO Requirements, and Case Studies
In 2025, customer perspectives on abradable coatings for turbomachinery are shaped by evolving Original Equipment Manufacturer (OEM) and Maintenance, Repair, and Overhaul (MRO) requirements, as well as operational feedback from recent deployments. OEMs increasingly demand coatings that not only enable tighter tip clearances for improved efficiency but also withstand aggressive operating environments and facilitate easier maintenance. For example, GE Aerospace has emphasized the importance of advanced abradable coatings in the next generation of jet engines, focusing on enhanced durability, erosion resistance, and compatibility with digital inspection technologies. These requirements are underscored by the need to reduce fuel consumption and emissions, aligning with broader industry sustainability goals.
MRO providers, such as Lufthansa Technik, report that modern abradable coatings must balance ease of application and repair with longevity in service. The shift toward more thermally sprayed and plasma-applied coatings—such as those based on nickel-graphite or ceramic matrix composites—reflects customer demand for reduced downtime and lower life-cycle costs. Recent case studies from Safran Aircraft Engines document successful field trials using newly formulated abradable coatings on high-pressure compressors, resulting in measurable improvements in engine performance and reduced maintenance frequency over the course of several thousand flight cycles.
OEMs and MROs are also responding to increased digitalization in engine health monitoring. Rolls-Royce has piloted sensor-enabled coatings in select turbofan fleets, providing real-time data on coating wear and tip clearance evolution. This approach allows predictive maintenance, extending component life and minimizing unscheduled removals, a key customer requirement looking forward. The feedback loop from these digital tools directly informs both coating design and MRO processes, promoting continuous improvement.
- Customers consistently request coatings with proven compatibility across multiple engine models and generations, as highlighted by Pratt & Whitney in their 2025 supplier guidelines.
- Energy sector clients, such as those operating industrial gas turbines, increasingly prioritize abradable coatings that perform reliably in harsh, particulate-laden environments, according to field reports by Siemens Energy.
Looking ahead, customer case studies and requirements signal a continued emphasis on multifunctional abradable coatings—those that not only optimize performance but also enable advanced monitoring, simplified repair, and cross-platform adaptability. The integration of such coatings into both new production and retrofit programs is set to accelerate, driven by direct customer feedback and the ongoing evolution of OEM and MRO service models.
Future Outlook: Disruptive Technologies, Sustainability, and Next-Gen Opportunities
The outlook for abradable coatings in turbomachinery from 2025 onward is shaped by accelerating innovation, sustainability imperatives, and the pursuit of next-generation performance. Several disruptive technologies are poised to redefine the sector, while industry leaders are setting ambitious targets for efficiency and environmental responsibility.
A primary area of focus is the development and commercial introduction of advanced ceramic matrix composites (CMCs) and metal matrix composites (MMCs) as abradable coatings. These materials promise greater temperature resistance and durability, supporting the trend toward higher operating temperatures in gas turbines for both aviation and energy generation. Companies such as GE Aerospace and Rolls-Royce are actively investing in coating compositions and manufacturing processes that will enable higher engine efficiencies, lower maintenance requirements, and extended component lifespans.
Digitalization is another disruptive force: the use of in-situ sensors and real-time monitoring is enabling predictive maintenance and optimized coating lifespan. Safran is exploring digital twins and sensor integration to monitor abradable coating wear, aiming to minimize downtime and improve reliability. This trend is expected to accelerate as the industry shifts toward data-driven asset management, with coatings engineered for both performance and “intelligent” maintenance.
Sustainability is now a central driver in new product development. The industry is moving toward coatings with reduced environmental impact in both production and lifecycle. Oerlikon Metco is pioneering low-VOC (volatile organic compound) slurry coatings and recyclable materials, while Haynes International is advancing alloy chemistries that minimize the use of critical raw materials and hazardous elements. Furthermore, the push for more sustainable aviation fuels and electrified propulsion concepts is prompting research into coatings compatible with hybrid and hydrogen-based engine cycles.
Looking ahead, the next few years will see increased collaboration between OEMs, coating suppliers, and academic partners to accelerate the qualification of novel abradable systems. Standardization efforts are also underway, led by organizations such as SAE International, to ensure coatings meet new regulatory and performance benchmarks for both civil and military applications.
- Adoption of advanced composite and nanostructured coatings for extreme environments.
- Integration of smart monitoring for predictive maintenance and optimized replacement cycles.
- Continued reduction of environmental footprint across the coating supply chain.
- Alignment with emerging propulsion technologies, including hydrogen and hybrid-electric engines.
In summary, the abradable coatings landscape for turbomachinery is poised for transformative change in the second half of the 2020s, with disruptive technologies, sustainability, and digitalization at the forefront of innovation and opportunity.