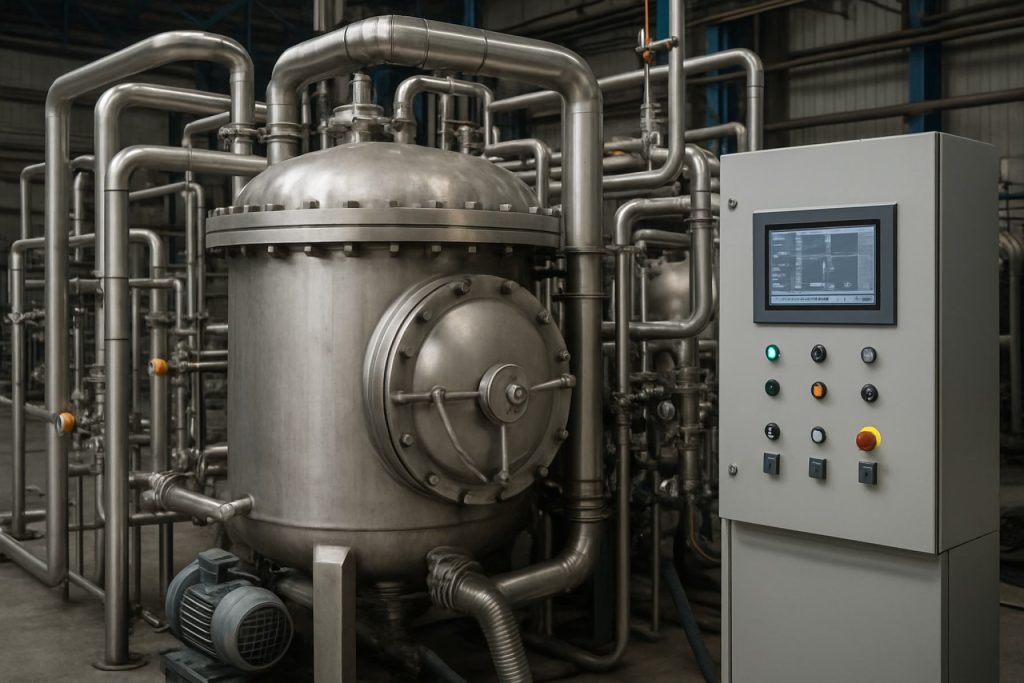
Indice
- Riepilogo Esecutivo: Dinamiche di Mercato e Principali Considerazioni per il 2025–2029
- Panoramica del Settore: L’Evoluzione e i Fondamenti dell’Ingegneria dei Sistemi di Indurimento a Gas
- Ultimi Progressi Tecnologici che Modellano il Settore
- Principali Fabbricanti e Collaborazioni Strategiche (citando fonti come secowarwick.com, ipsenusa.com e linde.com)
- Dimensione del Mercato, Traiettorie di Crescita e Previsioni a 5 Anni
- Analisi delle Applicazioni: Automotive, Aerospaziale, Utensili e Oltre
- Sostenibilità, Efficienza Energetica e Sviluppi Normativi
- Controlli Intelligenti Emergenti, Automazione e Trend di Monitoraggio Digitale
- Panorama Competitivo e Innovazione: Chi Sta Spingendo il Cambiamento?
- Prospettive Future: Opportunità, Rischi e Raccomandazioni Strategiche per gli Stakeholder
- Fonti e Riferimenti
Riepilogo Esecutivo: Dinamiche di Mercato e Principali Considerazioni per il 2025–2029
Il settore globale dell’ingegneria dei sistemi di indurimento a gas sta vivendo una crescita robusta mentre le industrie cercano un maggiore controllo, efficienza e sostenibilità nelle tecnologie di trattamento termico. Nel 2025, la domanda di soluzioni avanzate di indurimento a gas è spinta dai settori automobilistico, aerospaziale e della produzione di utensili, che richiedono proprietà metallurgiche precise e minima deformazione nei componenti trattati termicamente. La transizione dai tradizionali processi di indurimento a olio a sistemi a gas—particolarmente quelli che utilizzano azoto ed elio—riflette sia le preoccupazioni ambientali sia la necessità di un miglior controllo del processo.
I principali motori del mercato nel 2025 includono la restrizione delle normative ambientali, la ricerca di operazioni a emissioni di carbonio neutre, e i continui progressi nelle tecnologie di forno e circolazione del gas. Ad esempio, grandi produttori come ALD Vacuum Technologies e Bodycote hanno ampliato le loro offerte con forni a vuoto all’avanguardia dotati di indurimento a gas ad alta pressione, sostenendo sia l’efficienza energetica che la qualità del prodotto. Queste tecnologie affrontano direttamente le sfide dell’industria come la deformazione delle parti, l’ossidazione superficiale e la generazione di rifiuti pericolosi, posizionando l’indurimento a gas come un’alternativa preferita nelle applicazioni ad alta specifica.
Il mercato sta anche assistendo a un aumento della domanda di sistemi di indurimento a gas personalizzati e chiavi in mano che integrano software di controllo avanzati, monitoraggio dei processi in tempo reale e funzionalità di manutenzione predittiva. Aziende come SECO/WARWICK stanno guidando questa tendenza, offrendo piattaforme modulari che possono essere adattate alle esigenze in evoluzione dei produttori, inclusi quelli in transizione verso ambienti di produzione conformi a Industry 4.0. Parallelamente, fornitori come Air Liquide stanno investendo in soluzioni efficienti per la fornitura di gas e il riciclo, riducendo i costi operativi mentre si allineano con gli obiettivi di sostenibilità.
A livello regionale, il mercato Asia-Pacifico continua a espandersi rapidamente a causa della continua industrializzazione e a un passaggio verso una produzione di maggiore valore. Nel frattempo, il Nord America e l’Europa rimangono hub di innovazione, trainati da forti settori automobilistico e aerospaziale e da un focus sulla decarbonizzazione. I principali OEM stanno specificando sempre di più l’indurimento a gas nelle loro catene di approvvigionamento, accelerando l’adozione e stimolando ulteriori investimenti in ricerca e sviluppo da parte dei produttori di sistemi.
- I sistemi di indurimento a gas vedranno un tasso di crescita annuale composto (CAGR) nel range medio-alto a singolo cifra fino al 2029, supportato da fattori normativi, tecnici ed economici.
- I sistemi di nuova generazione enfatizzeranno l’integrazione digitale, l’efficienza energetica e la configurabilità flessibile per soddisfare le diverse esigenze industriali.
- Le collaborazioni strategiche tra costruttori di forni, fornitori di gas e specialisti dell’automazione sono attese per guidare l’innovazione e garantire vantaggi competitivi.
In conclusione, le prospettive per il settore dei sistemi di indurimento a gas nel 2025–2029 sono definite da progressi tecnologici, imperativi di sostenibilità e requisiti in espansione da parte degli utenti finali, posizionando il settore per una crescita e trasformazione continue.
Panoramica del Settore: L’Evoluzione e i Fondamenti dell’Ingegneria dei Sistemi di Indurimento a Gas
L’ingegneria dei sistemi di indurimento a gas ha subito una significativa trasformazione, riflettendo sia i progressi tecnologici che la crescente domanda industriale di trattamenti termici precisi ed energeticamente efficienti. L’indurimento a gas, che utilizza gas inerti o attivi ad alta pressione—come azoto, idrogeno o elio—per raffreddare rapidamente i metalli trattati termicamente, è diventato fondamentale per la metallurgia moderna, l’aerospaziale e la produzione automobilistica. Storicamente, l’indurimento a olio dominava il settore, ma il passaggio ai sistemi a gas nell’ultimo decennio è stato spinto da normative ambientali più severe, imperativi di sicurezza e dalla ricerca di un miglior controllo del processo e della qualità dei componenti.
Nel 2025, i principali attori del settore stanno sfruttando tecnologie avanzate di circolazione del gas, controllo della pressione e scambiatori di calore per ottimizzare l’uniformità dell’indurimento e minimizzare la deformazione in componenti critici. Ad esempio, ALD Vacuum Technologies e Bodycote hanno progettato sistemi capaci di indurimento a gas ad alta pressione (HPGQ) fino a 20 bar, fornendo tassi di raffreddamento superiori per leghe complesse mantenendo l’integrità superficiale. Tali sistemi sono sempre più integrati con piattaforme di automazione e monitoraggio digitale, consentendo aggiustamenti in tempo reale del flusso di gas, della pressione e della temperatura per una ripetibilità e tracciabilità migliorate.
I dati del settore provenienti dalle installazioni correnti evidenziano una tendenza pronunciata verso camere di indurimento più grandi e flessibili progettate per lotti e geometrie variabili. Aziende come Ipsen hanno introdotto progetti di forni modulari che consentono scalabilità e compatibilità con linee di trattamento esistenti. Inoltre, il consumo energetico rimane un punto focale ingegneristico: utilizzando il recupero di calore e progetti di ventilatori ottimizzati, i produttori stanno riducendo i costi operativi e l’impatto ambientale.
In termini di selezione del gas, l’idrogeno sta guadagnando terreno grazie alla sua superiore conduttività termica, nonostante le sfide legate alla sicurezza e all’infrastruttura. Tenova ha riferito di successi nella distribuzione dell’indurimento a base di idrogeno per trattamenti di leghe di grado aerospaziale, segnando un possibile cambiamento nei mezzi di indurimento preferiti nei prossimi anni. Nel frattempo, l’azoto rimane prevalente per applicazioni di uso generale, mentre l’elio è riservato per leghe speciali dove l’indurimento ultra-rapido è critico.
Guardando al futuro, le prospettive per l’ingegneria dei sistemi di indurimento a gas sono formulate dall’incontro dei concetti di Industry 4.0 e degli imperativi di sostenibilità. Nei prossimi tre-cinque anni, si prevede che continueranno ad essere adottate analisi predittive, diagnosi remoti e controlli di processo a ciclo chiuso. I principali OEM e i fornitori di servizi di trattamento termico sono attesi a investire ulteriormente in sistemi più verdi e adattabili—in allineamento con i requisiti di qualità dei clienti e le normative ambientali sempre più stringenti. Man mano che il settore evolve, la ricerca collaborativa tra i produttori di attrezzature e gli utenti finali sarà vitale per affrontare le sfide delle specifiche dei materiali sempre più sofisticate e degli obiettivi di efficienza operativa.
Ultimi Progressi Tecnologici che Modellano il Settore
L’ingegneria dei sistemi di indurimento a gas sta vivendo significativi avanzamenti nel 2025, spinta dall’imperativo di efficienza energetica, controllo del processo e sostenibilità nel settore del trattamento termico. Un’importante innovazione è l’integrazione di tecnologie sensoriali avanzate e monitoraggio dei processi in tempo reale, consentendo un controllo senza precedenti sul flusso di gas di indurimento, temperatura e pressione. Aziende come ALINEA hanno introdotto sistemi di controllo intelligenti che utilizzano algoritmi di machine learning per ottimizzare l’uso del gas e dei tassi di raffreddamento, riducendo il consumo energetico e migliorando la coerenza delle parti.
Un altro grande sviluppo è l’adozione diffusa di gas di indurimento ad alte prestazioni, come miscele di elio e azoto, che offrono caratteristiche di trasferimento di calore migliorate rispetto ai tradizionali sistemi a base di azoto puro o olio. Linde ha commercializzato soluzioni di fornitura gas modulari che consentono di passare senza problemi tra tipi di gas e adattare le prestazioni di indurimento ai requisiti specifici delle leghe, supportando i settori automobilistico e aerospaziale nel raggiungimento di rigorosi standard metallurgici.
I produttori di forni a vuoto stanno spingendo i limiti. SECO/WARWICK ha recentemente lanciato nuovi sistemi di indurimento a gas a vuoto dotati di riscaldamento a convezione diretta e flusso di gas multidirezionale, riducendo significativamente i tempi di ciclo mantenendo un indurimento uniforme. Questi sistemi sono sempre più dotati di connettività di Industry 4.0, consentendo manutenzione predittiva e diagnosi remote, che minimizzano i tempi di inattività e migliorano l’affidabilità operativa.
Il settore sta assistendo all’integrazione della manifattura additiva (AM) con l’indurimento a gas, in particolare per componenti complessi che richiedono profili termici personalizzati. Bodycote, un fornitore leader di servizi di trattamento termico, sta ampliando la sua capacità di indurimento a gas di precisione su parti AM, garantendo proprietà microstrutturali mirate e controllo della deformazione.
Guardando avanti, le prospettive per l’ingegneria dei sistemi di indurimento a gas sono definite da una maggiore automazione e digitalizzazione. Con continui investimenti in fabbriche intelligenti, analisi incorporate e circuiti di riciclo del gas ecologici, il settore è pronto per continui miglioramenti in efficienza e impatto ambientale. Man mano che le pressioni normative sulle emissioni e la sicurezza sul lavoro aumentano a livello globale, ci si aspetta che i produttori accelerino l’adozione di sistemi a ciclo chiuso e miscele di gas a basso potenziale di riscaldamento globale, posizionando l’industria per un’era di trasformazione nel 2025 e oltre.
Principali Fabbricanti e Collaborazioni Strategiche (citando fonti come secowarwick.com, ipsenusa.com e linde.com)
Il panorama globale dell’ingegneria dei sistemi di indurimento a gas nel 2025 è modellato dalle attività e collaborazioni di diversi produttori leader, le cui innovazioni e alleanze strategiche stanno influenzando direttamente l’adozione della tecnologia e gli standard del settore. Attori chiave come SECO/WARWICK, Ipsen e Linde sono in prima linea, ognuno sfruttando la propria esperienza per affrontare le esigenze in evoluzione nei settori automobilistico, aerospaziale e della produzione di utensili.
SECO/WARWICK ha continuato ad espandere la sua presenza sul mercato nel 2025, con un forte accento sui sistemi di indurimento a gas modulari progettati per processi di trattamento termico flessibili ed efficienti. Il focus strategico dell’azienda include il potenziamento dei propri forni a indurimento a gas ad alta pressione (HPGQ), integrando sistemi di controllo intelligenti per l’ottimizzazione energetica e la ripetibilità del processo. Gli annunci recenti di partnership sottolineano l’approccio di innovazione collaborativa di SECO/WARWICK, come progetti di sviluppo congiunto con OEM automobilistici e istituti di ricerca per soddisfare i crescenti requisiti di qualità delle parti e produttività (SECO/WARWICK).
Ipsen rimane un attore centrale nel 2025, in particolare nella tecnologia avanzata dei forni a vuoto combinata con indurimento a gas ad alta pressione. Gli investimenti continui di Ipsen nella digitalizzazione—attraverso la loro piattaforma di manutenzione predittiva PdMetrics® e sistemi pronti per l’automazione—dimostrano il loro impegno per l’integrazione di Industry 4.0. Alleanze strategiche con produttori globali, comprese le intese di fornitura multi-sito e trasferimenti di tecnologia in Asia e Europa, hanno ampliato la portata di Ipsen e rafforzato la sua rete di servizi. Inoltre, il focus di Ipsen su soluzioni ecologicamente sostenibili, come il raffreddamento a base di azoto, si allinea con le normative sulle emissioni sempre più restrittive e gli obiettivi di sostenibilità dei clienti (Ipsen).
Linde, un leader mondiale nei gas industriali, continua a influenzare l’ingegneria dei sistemi di indurimento a gas attraverso la fornitura di gas di processo ad alta purezza e le sue collaborazioni sull’ottimizzazione dei processi. Nel 2025, Linde sta avanzando nel suo lavoro con i principali produttori di forni per sviluppare tecnologie di miscelazione e fornitura di gas di nuova generazione che migliorano l’uniformità e l’efficienza nei cicli di indurimento. Le partnership strategiche di Linde spesso coinvolgono iniziative di R&D congiunte mirate a ridurre i tempi di ciclo e migliorare i risultati metallurgici, in particolare per applicazioni esigenti nei settori aerospaziale e automobilistico (Linde).
Guardando avanti, nei prossimi anni si prevede un’ulteriore consolidazione tra i fornitori di attrezzature, una maggiore integrazione delle tecnologie digitali e alleanze intersettoriali ampliate. Queste tendenze probabilmente accelereranno l’adozione di soluzioni di indurimento a gas flessibili, sostenibili e altamente automatizzate, consolidando i ruoli di leadership di SECO/WARWICK, Ipsen e Linde nel settore.
Dimensione del Mercato, Traiettorie di Crescita e Previsioni a 5 Anni
Il mercato globale per l’ingegneria dei sistemi di indurimento a gas è pronto per una crescita sostenuta fino al 2025 e nella seconda metà del decennio, spinto dalla crescente domanda di soluzioni avanzate di trattamento termico nei settori automobilistico, aerospaziale e della produzione ad alte prestazioni. L’indurimento a gas, un processo in cui vengono utilizzati gas inerti (comunemente azoto, argon o elio) per raffreddare rapidamente i metalli, è favorito per la sua capacità di raggiungere proprietà metallurgiche precise e di ridurre al minimo la deformazione rispetto all’indurimento a olio tradizionale. Man mano che i processi di produzione diventano più sofisticati e le normative ambientali si stringono, l’adozione dei sistemi di indurimento a gas è prevista in accelerazione.
Nel 2025, i principali produttori come ALDO UNION, Bodycote e Ipsen stanno segnalando un aumento nell’implementazione di forni per indurimento a gas—sia come sistemi autonomi che come moduli integrati all’interno di linee di trattamento termico automatizzate. Ad esempio, Ipsen segnala un’ulteriore crescita degli ordini per forni a vuoto dotati di capacità di indurimento a gas ad alta pressione (HPGQ), particolarmente tra i fornitori automobilistici di livello 1 che cercano di soddisfare rigorosi requisiti di qualità delle parti e produttività.
L’espansione del mercato è ulteriormente supportata da investimenti continua in R&D e dall’adozione di controlli digitali per ottimizzare l’uso del gas, l’efficienza energetica e la ripetibilità dei processi. Bodycote evidenzia la tendenza verso lotti di dimensioni maggiori e configurazioni di sistema ibride, che consentono di lavorare materiali diversi con minima contaminazione incrociata e massimizzazione dell’utilizzo del forno.
Da una prospettiva regionale, si prevede che l’Asia-Pacifico rappresenti il segmento in più rapida crescita, spinta dai centri di produzione automobilistica in Cina, India e Sud-Est asiatico, mentre Europa e Nord America continuano a modernizzare le infrastrutture di trattamento termico esistenti. Tenova ha recentemente annunciato nuove installazioni di sistemi di indurimento a gas su larga scala sia in Germania che negli Stati Uniti, dimostrando il momentum cross-regionale negli aggiornamenti dei sistemi.
- Entro il 2025, si prevede che il parco installato globale di sistemi industriali di indurimento a gas aumenterà del 7-9% anno dopo anno, con entrate da nuove attrezzature, retrofit e contratti di servizio che supereranno i livelli pre-pandemia.
- Nei prossimi cinque anni, la digitalizzazione (ad es., controlli abilitati per l’IoT, manutenzione predittiva) è destinata a diventare standard nelle nuove consegne di sistemi, aumentando il tempo di attivazione e la produttività per gli utenti finali (Ipsen).
- Considerazioni ambientali—specialmente la riduzione degli oli di indurimento e delle emissioni di VOC—accelera ulteriormente la transizione verso l’indurimento a gas nelle industrie regolamentate.
Guardando al futuro, le prospettive di mercato per l’ingegneria dei sistemi di indurimento a gas rimangono robuste, con innovazione concentrata su risparmi energetici, automazione dei processi e capacità di gestire geometrie di componenti sempre più complesse. Collaborazioni strategiche tra produttori di forni, fornitori di gas industriali e utenti finali probabilmente modeleranno il panorama competitivo fino al 2030.
Analisi delle Applicazioni: Automotive, Aerospaziale, Utensili e Oltre
L’ingegneria dei sistemi di indurimento a gas continua a giocare un ruolo fondamentale nel migliorare le prestazioni e l’efficienza dei componenti in settori chiave come automobilistico, aerospaziale e utensili, con applicazioni in rapido espansione in nuovi settori a partire dal 2025. L’adozione di tecnologie avanzate di indurimento a gas è guidata dalla necessità di un trattamento termico preciso, qualità del prodotto migliorata e conformità con stringenti standard ambientali e di sicurezza.
Nel settore automobilistico, la transizione verso veicoli elettrici e componenti leggeri ha stimolato la domanda di parti ad alta resistenza e senza deformazioni. L’indurimento a gas, in particolare utilizzando azoto ed elio, è sempre più preferito rispetto all’indurimento a olio tradizionale per la sua capacità di ridurre al minimo la deformazione delle parti e la contaminazione. I principali produttori di forni come ALDO UNION S.p.A. e Bodycote evidenziano l’implementazione di forni a vuoto con indurimento a gas ad alta pressione per trattare ingranaggi, alberi e componenti critici del sistema di trasmissione. Questa tecnologia supporta la produzione di parti di precisione per trasmissioni elettriche e sistemi di trasmissione, una tendenza che si prevede intensificherà con le inziative di elettrificazione per il 2027.
I produttori aerospaziali dipendono ugualmente dai sistemi di indurimento a gas per soddisfare specifiche rigorose per pale di turbina, carrelli di atterraggio e parti strutturali. La richiesta del settore per una superiore resistenza alla fatica e stabilità dimensionale ha portato all’uso diffuso di indurimento a gas ad alta pressione. Aziende come SECO/WARWICK e Ipsen offrono forni a vuoto ad alta pressione progettati per leghe aerospaziali, con continui innovazioni in sistemi multi-camera e ibridi per aumentare produttività e flessibilità. Le prospettive per il 2025-2028 indicano un’adozione accelerata, soprattutto poiché nuovi progetti di aerei richiedono tolleranze più rigide e materiali leggeri e ad alte prestazioni.
Nel settore degli utensili, dove precisione e resistenza all’usura sono fondamentali, l’indurimento a gas permette l’indurimento di stampi, modelli e utensili di taglio complessi con rischio minimo di rottura o cambiamento dimensionale. Park Thermal International e EcoFurnace forniscono sistemi ottimizzati per cicli di indurimento rapidi e raffreddamento uniforme, supportando i produttori nel soddisfare le esigenze di consegna just-in-time.
Oltre a questi settori consolidati, i sistemi di indurimento a gas vengono ora integrati in settori come la produzione additiva, la produzione di dispositivi medici e l’elettronica di precisione. Con l’intensificarsi della miniaturizzazione dei componenti e delle esigenze prestazionali, gli integratori di sistemi stanno offrendo soluzioni modulari pronte per l’automazione che consentono processi di trattamento termico scalabili e ripetibili.
Guardando al futuro, la convergenza delle tecnologie di Industry 4.0—comprese il monitoraggio dei processi in tempo reale e l’analisi dei dati—migliorerà ulteriormente il controllo dei processi e l’efficienza energetica nei sistemi di indurimento a gas. Entro il 2028, si prevede una più ampia adozione in entrambe le applicazioni tradizionali ed emergenti, supportata da un’innovazione continua da parte dei leader del settore e dalle esigenze in evoluzione della produzione ad alta precisione.
Sostenibilità, Efficienza Energetica e Sviluppi Normativi
L’ingegneria dei sistemi di indurimento a gas sta attraversando una significativa trasformazione nel 2025, guidata da crescenti richieste di sostenibilità, imperativi di efficienza energetica e l’evoluzione dei quadri normativi. Il settore del trattamento termico dei metalli, storicamente dipendente da processi ad alta intensità energetica e mezzi di indurimento pericolosi, sta passando verso soluzioni di indurimento a gas progettate—principalmente utilizzando gas come azoto, elio e argon—per raggiungere obiettivi tecnici e ambientali.
Un principale fattore di sostenibilità è la riduzione delle emissioni di gas serra e dei rifiuti pericolosi. I sistemi di indurimento a gas eliminano la necessità di indurenti a olio e polimeri, riducendo i rischi di incendio e i sottoprodotti tossici, facilitando operazioni più pulite. I recenti progetti di sistema da parte di aziende come ALD Vacuum Technologies e Bodycote enfatizzano la ricircolazione del gas a ciclo chiuso, il recupero di calore e l’integrazione con fonti di energia rinnovabile. Questi sistemi sono sempre più dotati di analisi in tempo reale e controlli avanzati per ottimizzare il flusso di gas, minimizzare il consumo e ridurre l’impronta di carbonio complessiva.
L’efficienza energetica è un altro punto focale. L’indurimento a gas richiede generalmente un maggiore input energetico iniziale per raggiungere tassi di raffreddamento sufficienti, specialmente con applicazioni ad alta pressione, ma i moderni sistemi compensano questo attraverso compressori ad alta efficienza, scambiatori di calore rigenerativi e azionamenti a velocità variabile. Ad esempio, Ipsen ha introdotto forni di indurimento a gas con raffreddamento adattivo e gestione energetica, portando a risparmi energetici segnalati fino al 20% rispetto ai sistemi legacy. Allo stesso modo, Tenova ha sviluppato linee di indurimento a gas modulari ed efficienti dal punto di vista energetico, destinate a ridurre il consumo di energia per tonnellata trattata.
I sviluppi normativi stanno anche plasmando le priorità ingegneristiche. La Direttiva sulle Emissioni Industriali dell’Unione Europea e il Clean Air Act dell’Agenzia per la Protezione Ambientale degli Stati Uniti mirano sempre di più alle emissioni dai forni industriali, comprese quelle utilizzate nei processi di trattamento termico e indurimento. La conformità ora richiede non solo controlli delle emissioni, ma anche robuste segnalazioni e tracciabilità. Aziende come SECO/WARWICK hanno risposto integrando strumenti di monitoraggio delle emissioni e di conformità digitale nei propri sistemi di indurimento a gas, anticipando standard più severi previsti nell’UE e in Nord America entro il 2027.
Guardando avanti, ci si aspetta ulteriori miglioramenti nell’efficienza del riciclo del gas, nel monitoraggio delle emissioni in tempo reale e nell’ottimizzazione dei processi guidata dall’AI. Collaborazioni tra industria, come quelle tra produttori di forni e fornitori di gas come Air Liquide e Linde, stanno accelerando lo sviluppo di miscele di gas sostenibili e soluzioni circolari per i gas di indurimento. Man mano che le normative si stringono e gli utenti finali richiedono catene di approvvigionamento più ecologiche, nei prossimi anni si prevede una crescente adozione di sistemi di indurimento a gas avanzati, energeticamente efficienti e conformi nelle operazioni globali di trattamento termico.
Controlli Intelligenti Emergenti, Automazione e Trend di Monitoraggio Digitale
Il panorama dell’ingegneria dei sistemi di indurimento a gas sta vivendo una rapida trasformazione, guidata dall’integrazione di controlli intelligenti, automazione avanzata e strumenti di monitoraggio digitale. Poiché industrie come automobilistica, aerospaziale e manifattura di precisione richiedono maggiore affidabilità e controlli di processo più rigorosi, le soluzioni di indurimento a gas nel 2025 sono sempre più caratterizzate da tecnologie intelligenti e connesse.
Una tendenza prominente è l’adozione di piattaforme IIoT (Internet Industriale delle Cose) che consentono il monitoraggio in tempo reale e diagnosi remote dei processi di indurimento. I principali produttori di sistemi stanno integrando reti sensoriali e dispositivi di edge computing direttamente nelle loro attrezzature, facilitando la raccolta di dati dettagliati sul processo—che vanno dai tassi di flusso del gas di indurimento e pressione alle temperature delle camere e ai profili di raffreddamento delle superfici delle parti. Aziende come SECO/WARWICK hanno introdotto sistemi di indurimento a gas con pannelli di controllo digitali, integrazione avanzata di PLC e analisi basate su cloud per manutenzione predittiva e ottimizzazione dei processi.
L’automazione sta anche avanzando, con la movimentazione robotica dei materiali e il caricamento/scaricamento automatizzati diventati standard nelle nuove installazioni. Ad esempio, Bodycote ha implementato linee di indurimento a gas completamente automatizzate in diverse strutture, raggiungendo una maggiore produttività, riducendo l’intervento degli operatori e migliorando la ripetibilità del processo. Questi sistemi sono completati da piattaforme SCADA (Supervisory Control and Data Acquisition) che centralizzano il controllo e il monitoraggio, consentendo agli operatori di gestire più forni e moduli di indurimento da un’interfaccia unificata.
I gemelli digitali—repliche virtuali di sistemi fisici di indurimento—stanno emergendo come uno strumento potente per simulazione, ottimizzazione e risoluzione dei problemi di processo. Le soluzioni offerte da Aldo Union e altri produttori di forni internazionali sfruttano flussi di dati in tempo reale e modellazione avanzata, consentendo agli utenti di prevedere le prestazioni del sistema e apportare aggiustamenti basati sui dati senza interrompere la produzione.
- Assicurazione della qualità migliorata: Sensori integrati e analisi garantiscono coerenza da parte a parte e consentono una rapida identificazione delle deviazioni del processo.
- Efficienza energetica e delle risorse: Controlli intelligenti ottimizzano il consumo di gas e i tempi di ciclo, allineandosi con gli obiettivi di sostenibilità.
- Servizio e supporto remoto: Attraverso piattaforme digitali sicure, gli ingegneri possono diagnosticare e risolvere problemi senza visite in loco—un vantaggio critico nelle operazioni globali.
Guardando ai prossimi anni, il settore è atteso a un ulteriore abbraccio del controllo dei processi guidato dall’AI e a un’integrazione ancora più profonda con i sistemi di produzione aziendale. Mentre le normative e le richieste dei clienti per la tracciabilità e la produzione senza difetti aumentano, il ruolo dei sistemi di indurimento a gas intelligenti, automatizzati e monitorati digitalmente diventerà sempre più centrale nelle operazioni di trattamento termico a livello mondiale.
Panorama Competitivo e Innovazione: Chi Sta Spingendo il Cambiamento?
Il panorama competitivo nell’ingegneria dei sistemi di indurimento a gas sta vivendo una significativa trasformazione nel 2025, spinta da requisiti industriali in evoluzione, imperativi di sostenibilità e rapidi progressi tecnologici. I principali attori stanno investendo attivamente in R&D per ottimizzare l’efficienza dei sistemi, ridurre l’impatto ambientale e migliorare l’automazione. Il mercato è caratterizzato dall’interazione tra produttori affermati di forni, sviluppatori di tecnologie di indurimento specializzati e fornitori di gas industriali, ciascuno contribuendo con innovazioni uniche.
A guidare l’azione ci sono aziende come ALD Vacuum Technologies e Bodycote, che hanno introdotto tecnologie avanzate di forni a vuoto e soluzioni modulari di indurimento a gas progettate per i settori aerospaziale, automobilistico e della ingegneria di precisione. ALD Vacuum Technologies ha recentemente lanciato la sua ultima generazione di sistemi di indurimento a gas ad alta pressione, che sfruttano algoritmi di controllo di processo precisi e moduli di recupero energetico per aumentare i tassi di raffreddamento riducendo al contempo il consumo di gas.
L’automazione e l’integrazione digitale sono motivatori chiave di innovazione. Linde plc è all’avanguardia nell’analisi dei processi inline e nelle soluzioni di monitoraggio remoto, consentendo aggiustamenti in tempo reale del flusso di gas e della pressione per una maggiore ripetibilità e qualità delle parti. Nel frattempo, Air Liquide sta espandendo il suo portafoglio di sistemi di fornitura e gestione del gas, concentrandosi su miscele di azoto ed elio che offrono una superiorità di uniformità di indurimento con una riduzione dell’impronta di carbonio.
Entranti emergenti e specialisti di nicchia stanno anche rimodellando il campo. SECO/WARWICK continua a innovare con sistemi di raffreddamento ibridi che combinano gas e tecniche di convezione, offrendo una maggiore flessibilità per leghe e geometrie complesse. Le collaborazioni tra produttori di forni OEM e aziende di tecnologia digitale, come quelle avviate da Tenova, stanno accelerando l’adozione di strumenti di manutenzione predittiva e ottimizzazione dei processi guidati dall’AI.
Guardando al futuro, nei prossimi anni si prevede un’enfasi crescente sulla sostenibilità, con fornitori principali che si impegnano per operazioni a emissioni zero e circuiti di gas riciclabili. L’implementazione di sistemi compatibili con Industry 4.0 migliorerà ulteriormente la competitività, consentendo agli utenti di ottenere tolleranze di processo più rigide e costi operativi più bassi. Mentre le pressioni normative aumentano e gli utenti finali richiedono maggiore efficienza, si prevede che il pipeline di innovazione rimanga robusto, con una concorrenza dinamica che continua a guidare i progressi nell’ingegneria dei sistemi di indurimento a gas.
Prospettive Future: Opportunità, Rischi e Raccomandazioni Strategiche per gli Stakeholder
Le prospettive future per l’ingegneria dei sistemi di indurimento a gas nel 2025 e negli anni successivi sono influenzate da richieste crescenti di materiali avanzati, quadri normativi in evoluzione e la continua spinta verso l’efficienza energetica e l’automazione. Le opportunità abbondano in diversi settori chiave, in particolare mentre i settori automobilistico, aerospaziale e della produzione di utensili continuano a cercare soluzioni di trattamento termico più veloci, più pulite e più controllabili. Si prevede che gli investimenti strategici si concentreranno sull’integrazione di sistemi di controllo digitali e gas di indurimento ecologici, rispondendo sia agli obiettivi di efficienza operativa sia ai requisiti di normative sempre più stringenti.
- Opportunità: La transizione dall’indurimento a base di olio verso il raffreddamento ad alta pressione con gas (HPGQ) sta accelerando, spinta dalla necessità di minimizzare la deformazione e migliorare le proprietà meccaniche dei componenti critici. Aziende come Air Products and Chemicals, Inc. e Linde plc stanno espandendo attivamente le loro soluzioni per la fornitura di gas e il controllo dei processi per soddisfare la domanda crescente. Inoltre, l’aumento dell’adozione delle tecnologie di Industry 4.0—come l’analisi dei dati in tempo reale, il monitoraggio remoto e la manutenzione predittiva—offre nuove prospettive per integratori di sistemi e OEM. L’automazione dei processi avanzata e il controllo della qualità dovrebbero generare risparmi significativi e affidabilità del processo.
- Rischi: L’industria affronta rischi associati all’investimento di capitale iniziale, in particolare per i piccoli e medi OEM che potrebbero avere difficoltà a giustificare il passaggio dall’indurimento a olio tradizionale. I problemi di sicurezza relativi alla manipolazione di gas ad alta pressione e la necessità di formazione avanzata per gli operatori rimangono anche importanti. Inoltre, la disponibilità e le fluttuazioni dei costi dei gas industriali, in particolare dell’elio e dell’azoto ad alta purezza, potrebbero influenzare i budget operativi. I cambiamenti normativi riguardanti le emissioni di gas serra o la sicurezza sul lavoro potrebbero richiedere un rapido adattamento dei sistemi di gestione della fornitura di gas e degli scarichi.
- Raccomandazioni Strategiche: Si consiglia agli stakeholder di investire in sistemi di indurimento a gas flessibili e modulari in grado di gestire una varietà di dimensioni e leghe delle parti, come esemplificato dalle recenti linee di prodotti di Bodycote plc e Ipsen. Collaborare con fornitori di gas industriali per soluzioni di consegna e recupero personalizzate può mitigare i rischi di fornitura e ridurre i costi operativi. È fondamentale anche sviluppare le competenze della forza lavoro, assicurando che gli operatori siano formati sia sulla sicurezza che sulla gestione dei processi digitali. Infine, un monitoraggio costante degli standard internazionali in evoluzione e delle normative locali sarà cruciale per la conformità a lungo termine e l’accesso al mercato globale.
Poiché la sostenibilità e la trasformazione digitale continuano a plasmare il panorama industriale, l’ingegneria dei sistemi di indurimento a gas è pronta per una significativa evoluzione, offrendo sia sfide sia notevoli ricompense per gli stakeholder proattivi nei prossimi anni.
Fonti e Riferimenti
- Air Liquide
- ALD Vacuum Technologies
- Ipsen
- Tenova
- ALINEA
- Linde
- SECO/WARWICK
- Park Thermal International
- ALD Vacuum Technologies