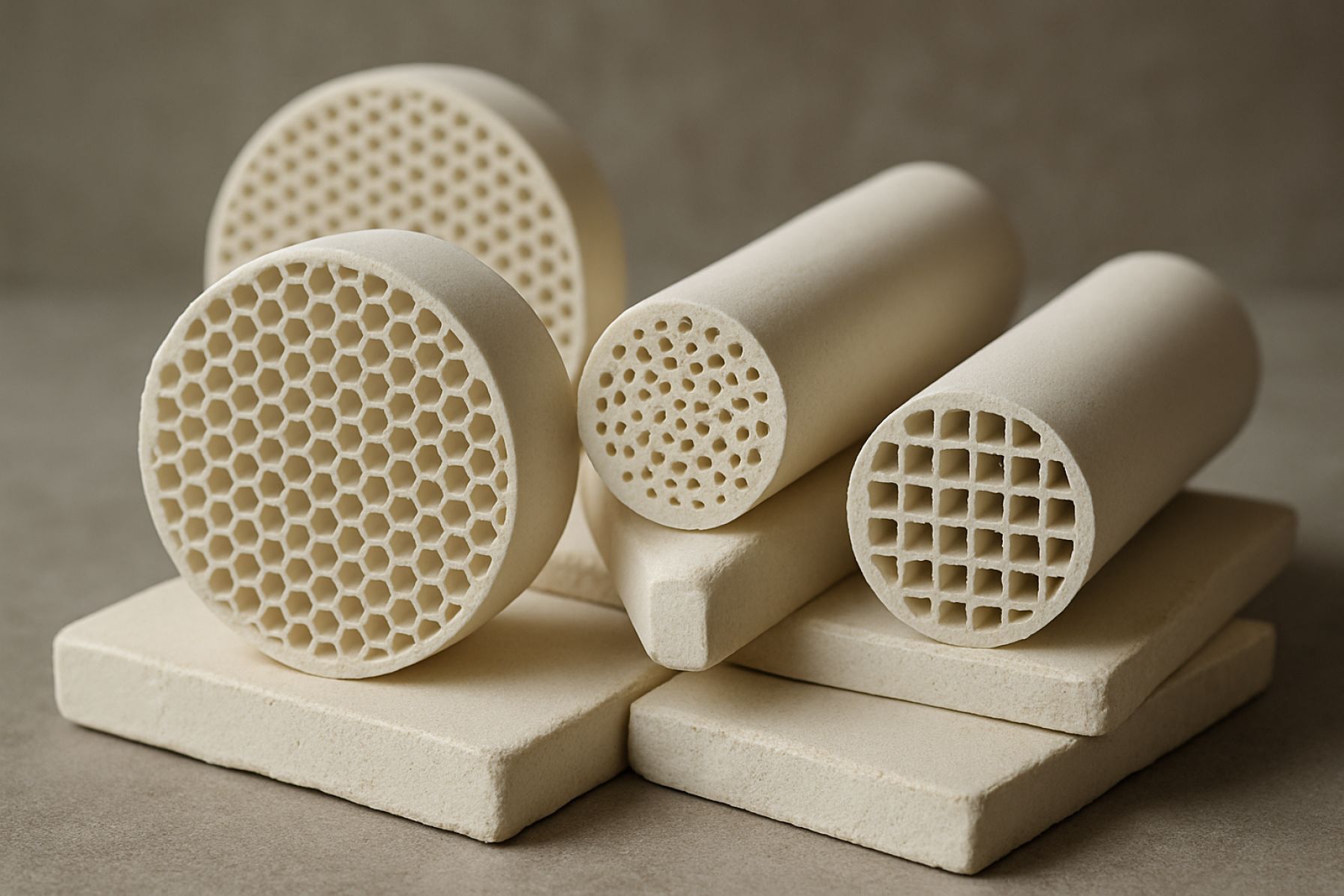
Table of Contents
- Executive Summary: 2025 Outlook for Kaolinite Ceramic Membranes
- Core Technology Advances: Materials, Design, and Manufacturing
- Key Players and Industry Initiatives (Official Company Profiles)
- Current and Emerging Applications in Water, Gas, and Chemical Processing
- Market Size, Regional Dynamics, and 2025–2030 Growth Forecasts
- Cost Analysis: Production, Scalability, and Economic Impact
- Sustainability, Environmental Benefits, and Regulatory Trends
- Strategic Partnerships and R&D Collaborations (Industry Sources Only)
- Competitive Landscape: Barriers, Opportunities, and Threats
- Future Outlook: Disruptive Innovations and Strategic Recommendations
- Sources & References
Executive Summary: 2025 Outlook for Kaolinite Ceramic Membranes
The global engineering landscape for kaolinite-based ceramic membranes is poised for significant evolution in 2025, driven by escalating demand for robust, cost-effective filtration technologies across water treatment, chemical processing, and biopharmaceutical sectors. Kaolinite, a naturally abundant clay mineral, offers a unique combination of affordability, chemical stability, and mechanical strength, making it a preferred material for ceramic membrane fabrication. As of early 2025, advancements in membrane engineering are focusing on optimizing pore structure, enhancing permeability, and lowering sintering temperatures to further reduce manufacturing costs and environmental impact.
Several industry leaders are actively investing in the scale-up and commercialization of kaolinite-based ceramic membranes. Membrana Filtration Systems and TIANKE Water Treatment Technologies have both announced new pilot projects utilizing kaolinite-derived tubular and flat-sheet membranes for municipal and industrial wastewater applications. These projects leverage improved slip casting and extrusion techniques, enabling the production of membranes with controlled pore sizes (in the microfiltration and ultrafiltration ranges) and superior fouling resistance.
Data from NGK INSULATORS, LTD. and CTI Ceramic Technology Inc. indicate that membrane lifetimes are now exceeding five years in continuous operation, even under aggressive chemical exposure, with flux rates surpassing 200 L/m2h for water filtration applications. These performance benchmarks are supported by ongoing material innovations, such as the introduction of composite structures where kaolinite is blended with alumina or titania to enhance membrane selectivity and durability.
Looking forward, the sector is expected to benefit from significant R&D investments in membrane functionalization and module design. Pall Corporation and Cerafiltec have both outlined strategies for 2025–2027 that include the integration of advanced surface modification techniques—such as sol-gel coatings and nanoparticle impregnation—aimed at further mitigating fouling and expanding chemical compatibility. Furthermore, digital monitoring and predictive maintenance solutions are anticipated to become standard in large-scale installations, boosting operational reliability.
Overall, the outlook for kaolinite-based ceramic membrane engineering in 2025 and beyond is robust. Continued collaboration between established ceramic manufacturers and emerging membrane specialists is expected to drive down costs, broaden application fields, and accelerate global adoption—particularly in regions facing acute water scarcity and stringent discharge regulations.
Core Technology Advances: Materials, Design, and Manufacturing
Kaolinite-based ceramic membrane engineering continues to gain momentum in 2025, driven by the need for cost-effective, high-performance materials in water treatment, gas separation, and industrial filtration. Kaolinite, a naturally abundant clay mineral, is prized for its high thermal stability, chemical inertness, and fine particle size, making it an attractive base material for ceramic membrane fabrication.
Recent advances focus on optimizing both material composition and membrane architecture. Companies such as Ceramic Membrane Systems BV and Mantec Filtration have developed proprietary formulations and sintering techniques, enabling the production of membranes with tailored pore sizes and enhanced mechanical strength. These improvements facilitate the creation of asymmetric multilayer structures, in which a thin, dense kaolinite-based selective layer is supported by a robust, porous substrate. This design significantly improves permeate flux and selectivity while reducing operational costs.
2025 sees increased adoption of eco-friendly manufacturing processes, such as low-temperature sintering and the use of recycled kaolinite sources. NGK INSULATORS, LTD. has reported success in scaling up energy-efficient production lines for ceramic membranes, integrating advanced thermal management and waste minimization strategies to lower environmental impact. Additionally, the incorporation of green binders and pore-forming agents is being pursued to further reduce the carbon footprint of membrane fabrication.
New surface engineering techniques, such as atomic layer deposition and sol-gel coatings, are being integrated to enhance fouling resistance and chemical durability. For instance, LiqTech International, Inc. is leveraging nano-coating methods to impart hydrophilic or hydrophobic properties according to application needs, expanding the operational envelope of kaolinite-based membranes across diverse industrial sectors.
Digital manufacturing and quality control are also advancing, with real-time process monitoring and automated defect detection now standard at leading facilities. This ensures higher product consistency and enables rapid customization to meet specific client requirements.
Looking ahead, ongoing collaborations between industrial players and academic institutions are expected to yield further innovations in membrane design and hybrid materials. The next few years will likely see the commercial introduction of kaolinite-based membranes with enhanced multifunctional properties—such as catalytic or antimicrobial capabilities—positioning this technology as a key enabler in both traditional and emerging separation markets.
Key Players and Industry Initiatives (Official Company Profiles)
The global landscape of kaolinite-based ceramic membrane engineering in 2025 is characterized by both established industry leaders and emerging innovators. These key players are driving advancements in membrane fabrication, application development, and process optimization, targeting sectors such as water treatment, food and beverage processing, and industrial effluent management.
- Pall Corporation is a prominent manufacturer with a significant footprint in ceramic membrane technology. In recent years, Pall has leveraged kaolinite-based membranes for enhanced durability and chemical resistance, particularly in water and wastewater treatment. Their modular systems have been adopted in municipal and industrial applications globally, supporting sustainability targets and regulatory compliance.
- Mott Corporation specializes in porous metal and ceramic filtration solutions, including kaolinite-derived membranes. Mott’s ongoing R&D focuses on optimizing pore structure and membrane robustness to serve sectors requiring high flux rates and long operational lifespans. The company’s custom-engineered modules are being deployed in pilot and commercial-scale projects across the US, Europe, and Asia.
- CERAFILTEC is recognized for its flat-sheet ceramic membrane modules, which incorporate kaolinite blends for improved fouling resistance. In 2024, CERAFILTEC announced several new installations in the Middle East and Southeast Asia, supporting desalination and brackish water reclamation. Their technology roadmap through 2027 emphasizes further improvements in energy efficiency and lifecycle cost reduction.
- Membrane Solutions LLC continues to invest in low-cost kaolinite-based ceramic membranes tailored for decentralized water treatment. Their 2025 portfolio includes scalable pilot units for remote and rural deployment, with a focus on accessibility and low maintenance.
- KeraNor AS and Kerafol Keramische Folien GmbH are expanding their reach in the European market with advanced ceramic membranes manufactured from high-purity kaolinite. Both companies are collaborating with universities and water utilities to demonstrate next-generation modules with enhanced selectivity and mechanical strength.
Looking ahead, leading players are expected to deepen collaboration with end-users and research institutions to accelerate the commercialization of kaolinite-based membranes. The focus will be on scaling up production, testing new application domains (e.g., pharmaceutical, bioprocessing), and meeting increasingly stringent environmental regulations. This dynamic ecosystem, backed by strong industrial engagement, is poised to shape the evolution of ceramic membrane engineering over the next several years.
Current and Emerging Applications in Water, Gas, and Chemical Processing
Kaolinite-based ceramic membranes are gaining increasing attention in water, gas, and chemical processing applications due to their favorable combination of mechanical strength, chemical resistance, and relative affordability. As of 2025, manufacturers and technology developers are leveraging advances in membrane fabrication—such as tape casting, extrusion, and 3D printing—to optimize pore structure, permeability, and selectivity for target applications.
In water treatment, kaolinite ceramic membranes are being adopted for microfiltration and ultrafiltration tasks, notably in municipal and industrial wastewater recovery. For instance, Membranes International Inc. highlights the use of ceramic membranes for removing particulates, bacteria, and organic contaminants, with kaolinite-based variants offering competitive cost-performance ratios compared to alumina or zirconia alternatives. The durability and fouling resistance of these membranes make them attractive for pre-treatment in desalination and for treating high-solid-content effluents.
Within the chemical industry, kaolinite-based membranes are increasingly used for solvent recovery and the separation of acids, bases, or other corrosive chemicals, thanks to their inherent stability. Pall Corporation reports ongoing implementation of ceramic membranes for aggressive process streams, noting that kaolinite-clay compositions can enable cost-effective solutions for medium-duty chemical separations.
Gas separation represents an emerging field for kaolinite membranes, as developers seek alternatives to polymeric or zeolite-based technologies. Companies such as KERAFOL Keramische Folien GmbH are exploring kaolinite-based composite membranes for carbon dioxide capture, biogas upgrading, and hydrogen purification, focusing on engineered microstructure to tune selectivity and flux.
Looking ahead, the next several years are expected to see continued refinement of kaolinite membrane engineering. Advances in additive manufacturing and surface functionalization are forecast to improve membrane performance and lower production costs, expanding their competitiveness. As regulatory pressure grows for sustainable water reuse and reduced emissions, demand for robust, long-lifetime membrane technologies is likely to rise. Strategic partnerships between ceramic producers—such as Mantec Filtration—and end-users in utilities and chemical processing are anticipated to accelerate commercial deployment and innovation.
- Kaolinite-based ceramic membranes are already serving in water filtration, chemical process separation, and early-stage gas purification.
- Technological advances in fabrication and surface modification are expected to enhance performance and broaden the application landscape by 2030.
- Cost-effective, sustainable, and resilient membrane solutions are increasingly prioritized by water utilities and industrial processors alike.
Market Size, Regional Dynamics, and 2025–2030 Growth Forecasts
The global market for kaolinite-based ceramic membrane engineering is poised for notable expansion between 2025 and 2030, underpinned by the growing demand for robust, chemically resistant, and energy-efficient filtration solutions in water treatment, chemical processing, and environmental remediation sectors. The unique properties of kaolinite—abundant availability, low cost, and favorable sintering behavior—have positioned it as a preferred raw material for ceramic membrane fabrication, especially in regions with rich kaolin deposits such as China, India, and Brazil.
In 2025, Asia-Pacific is expected to maintain its lead in both production and application, driven by rapid industrialization and stringent environmental regulations that necessitate advanced wastewater treatment technologies. Chinese manufacturers, including Kerui Refractory and Jiuwu Hi-Tech, have significantly scaled up their membrane production capacities, with emphasis on low-cost, high-throughput ceramic membranes for industrial and municipal water treatment. India is also witnessing increased R&D activity and the establishment of new manufacturing units, supported by local kaolin reserves and government initiatives to modernize the water infrastructure (Imerys).
Europe’s market is characterized by a strong focus on innovation and sustainability, with companies such as ITN Nanovation AG and LiqTech International pioneering new kaolinite-based composite membranes that offer enhanced selectivity and fouling resistance for industrial effluent treatment and bioprocessing. The region’s strict regulatory frameworks for discharge water quality continue to drive investment in advanced membrane technologies.
The Middle East and North Africa (MENA) region is emerging as a promising market for kaolinite-based ceramic membranes, particularly in desalination and oil & gas applications. Local collaborations with international technology providers are underway to address water scarcity and compliance with environmental standards (Alfa Laval).
Looking ahead to 2030, the global kaolinite-based ceramic membrane market is projected to experience a compound annual growth rate (CAGR) in the high single digits, with the strongest growth anticipated in Asia and the Middle East. Key drivers include ongoing investments in water and wastewater infrastructure, stricter environmental controls, and continuous advances in ceramic membrane engineering—such as the development of asymmetric and composite structures for improved performance and cost-efficiency. The market outlook remains positive, bolstered by the expanding adoption of ceramic membranes in emerging sectors such as pharmaceuticals, food and beverage, and resource recovery (Pall Corporation).
Cost Analysis: Production, Scalability, and Economic Impact
The economic viability of kaolinite-based ceramic membrane engineering is shaped by production costs, scalability potential, and broader industry trends, especially as the sector enters 2025. Kaolinite, a naturally occurring clay mineral, continues to be a preferred raw material for ceramic membranes due to its abundance, low cost, and favorable sintering characteristics. Leading manufacturers, such as Kerafol – Keramische Folien GmbH, utilize kaolinite in their membrane products, leveraging its cost-effectiveness and accessibility.
Production costs for kaolinite-based ceramic membranes are primarily influenced by raw material procurement, processing (including calcination and sintering), shaping, and finishing. The widespread availability of kaolinite enables membrane producers to establish large-scale supply chains, reducing material input costs. For instance, Imerys, a global supplier of industrial minerals, maintains mining and processing operations dedicated to high-purity kaolin, ensuring reliable and cost-effective sourcing for the ceramics industry.
Manufacturing advancements are further enhancing scalability and economic efficiency. Continuous improvements in extrusion and tape casting technologies have increased production throughput and uniformity, lowering per-unit costs for ceramic membranes. Companies such as Ceramic Technology, Inc. offer scalable solutions for producing tubular and flat-sheet membranes, reflecting the industry’s shift towards modular, high-volume manufacturing.
The adoption of energy-efficient sintering processes is another driver of cost reduction. Lower sintering temperatures and shorter furnace cycles, enabled by optimized kaolinite formulations, reduce energy consumption and operational expenses. Morgan Advanced Materials highlights ongoing research into alternative sintering methods and binder systems, which could further decrease energy requirements in the near future.
From an economic impact perspective, the scalability of kaolinite-based ceramic membranes is significant, especially for water treatment, gas separation, and industrial filtration. Modular membrane configurations and standardized fabrication methods are lowering barriers to entry for new market participants and enabling cost-effective expansions. For example, Pall Corporation is expanding its ceramic membrane offerings to address large-scale water reuse and industrial wastewater treatment, capitalizing on the favorable economics of kaolinite-based materials.
Looking ahead, the next several years are likely to see further reductions in production costs through supply chain optimization, energy-saving process innovations, and market-driven scaling. The robust supply of kaolinite, combined with ongoing technological advancements, is expected to cement the material’s position as a cornerstone of affordable, high-performance ceramic membrane engineering.
Sustainability, Environmental Benefits, and Regulatory Trends
Kaolinite-based ceramic membranes are gaining significant traction in 2025 as industries and regulators intensify their focus on sustainability, environmental protection, and resource efficiency. The inherent advantages of kaolinite, such as its natural abundance, low cost, and minimal environmental footprint during extraction and processing, position it as a preferred raw material for next-generation ceramic membranes. Compared to synthetic or high-purity materials, kaolinite’s accessibility reduces both the embodied energy and carbon emissions associated with membrane production, aligning well with global decarbonization goals.
Leading membrane manufacturers highlight the environmental benefits of kaolinite-based ceramics, including their long operational life, chemical stability, and resistance to fouling. These attributes not only minimize the frequency of membrane replacement but also lower the volume of solid waste generated over time. For example, LiqTech International reports that their ceramic membrane systems, which can utilize kaolinite compositions, deliver superior lifecycle efficiencies and enable water reuse processes that substantially reduce industrial wastewater discharge.
From a regulatory perspective, 2025 is witnessing accelerated policy action in the US, EU, and Asia to mandate stricter effluent standards, promote circular economy practices, and incentivize green technology adoption. The European Union’s updated Urban Waste Water Treatment Directive, coming into effect in 2025, emphasizes advanced treatment methods to minimize micropollutants and promote water reuse—trends that favor the adoption of robust ceramic membrane solutions (European Union). Likewise, China’s focus on industrial water reuse and zero-liquid-discharge (ZLD) systems under its 14th Five-Year Plan encourages investments in sustainable membrane technologies, including those based on kaolinite (Ministry of Ecology and Environment of the People’s Republic of China).
Industry organizations such as the American Ceramic Society are actively supporting research and standardization efforts to ensure that ceramic membranes adhere to rigorous environmental and safety criteria. These collaborative initiatives are expected to accelerate the commercialization of kaolinite-based membranes designed for resource efficiency, waste minimization, and compliance with evolving regulatory frameworks.
Looking ahead, as manufacturers scale up production and regulatory bodies tighten sustainability requirements, the deployment of kaolinite-based ceramic membranes will likely expand across sectors including municipal water treatment, food and beverage, and pharmaceuticals. This trajectory underscores not only the environmental benefits of kaolinite-derived ceramics, but also their strategic importance in meeting 2025 and near-future regulatory and sustainability expectations.
Strategic Partnerships and R&D Collaborations (Industry Sources Only)
Strategic partnerships and R&D collaborations are playing a critical role in advancing kaolinite-based ceramic membrane engineering as the sector matures in 2025. Companies are increasingly recognizing the need for technical alliances to address cost, scalability, and performance challenges, while also responding to tightening regulatory standards and heightened sustainability expectations in water, chemical, and industrial process applications.
One notable trend is the strengthening of industry-academic partnerships to accelerate material innovations. For instance, KERAFOL, a leading German ceramic membrane manufacturer, has been actively working with technical universities to optimize kaolin-derived supports, targeting improved pore uniformity and mechanical stability for micro- and ultrafiltration modules. Such collaborations have resulted in new pilot-scale membrane lines with increased permeability and reduced fouling, enabling broader adoption in industrial wastewater treatment.
Global manufacturers are also forming cross-sector consortia to exploit regional kaolinite resources and develop value-added membrane products. CTI Ceramic Technologies in France is collaborating with local mining companies and downstream users in the food and beverage sector to create customized membranes with tailored selectivity. This partnership model leverages raw material supply, application expertise, and process engineering to deliver solutions that meet sector-specific requirements for durability and performance.
Meanwhile, in Asia, CeraMem (a division of KERAMIC Membrane in South Korea) has established joint R&D initiatives with municipal water authorities to demonstrate the cost-effectiveness of kaolinite-based membranes in large-scale drinking water plants. These projects are generating data to support regulatory approval and commercialization, with the aim of replacing polymeric membranes in select applications by 2027.
Industry alliances are also focusing on sustainability and circular economy objectives. SUEZ has partnered with advanced ceramics start-ups to develop recyclable kaolinite membrane modules and to streamline end-of-life recovery processes. This aligns with European Union directives on waste reduction and resource efficiency, and is expected to set new standards for membrane lifecycle management.
Looking ahead, such strategic partnerships and R&D collaborations are anticipated to intensify through 2025 and beyond, driven by the need for accelerated scale-up, market expansion, and compliance with stricter environmental frameworks. The sector’s collaborative model, uniting manufacturers, raw material suppliers, end-users, and regulatory bodies, is likely to be a key enabler for rapid technological and commercial progress in kaolinite-based ceramic membrane engineering.
Competitive Landscape: Barriers, Opportunities, and Threats
The competitive landscape for kaolinite-based ceramic membrane engineering is evolving rapidly in 2025, driven by the demand for robust, cost-effective separation technologies in water treatment, food processing, and chemical industries. Several key factors shape the sector’s barriers, opportunities, and threats.
- Barriers: One significant barrier remains the challenge of achieving consistent membrane quality at scale, given raw material variability and the technical complexity of controlling pore size and distribution. Companies like Mantec Filtration emphasize the importance of proprietary formulation and firing techniques to ensure repeatable performance. Additionally, the necessity for high-temperature sintering facilities and advanced shaping equipment creates a capital-intensive entry point, limiting the number of new market entrants.
- Opportunities: The 2025 market is buoyed by tightening global regulations on industrial effluent and potable water, which fuel demand for reliable, long-life filtration solutions. Kaolinite-based membranes, with their inherent chemical resistance and cost advantage, are increasingly adopted in decentralized and rural water treatment projects, particularly in Asia and Africa. KERAFOL and LiqTech International have expanded their portfolios, introducing modular systems that simplify integration into existing infrastructure. The growing drive toward sustainability, with a focus on materials sourced from abundant and low-cost clays, opens doors for regional suppliers to enter the value chain. Furthermore, research into hybrid membrane technologies—combining kaolinite with functional additives—shows promise for improved selectivity and fouling resistance, as noted by NGK Insulators.
- Threats: Competitive pressures stem from alternative materials, such as alumina, zirconia, and polymer-based membranes, which continue to advance in performance and price competitiveness. For instance, Pall Corporation and SUEZ Water Technologies & Solutions are investing heavily in polymeric ultrafiltration, targeting markets traditionally served by ceramics. Additionally, supply chain disruptions—stemming from geopolitical uncertainties or energy cost volatility—pose a risk to the kaolinite supply and membrane production. Intellectual property protection remains a challenge, with several regional manufacturers in emerging economies replicating designs from established players, potentially eroding market share and pricing power.
Looking ahead, the next few years will likely see intensified competition as established ceramic membrane producers innovate to reduce costs and enhance performance, while startups leverage local kaolin resources to address niche applications. Strategic partnerships between technology developers and end-users are expected to accelerate technology adoption, particularly in water-stressed regions. However, sustained R&D and investment in advanced manufacturing will be critical for kaolinite-based membrane technologies to capture a larger share of the global filtration market.
Future Outlook: Disruptive Innovations and Strategic Recommendations
As we enter 2025, the future of kaolinite-based ceramic membrane engineering is poised for significant transformation, driven by advances in material science, sustainability imperatives, and process optimization. Kaolinite, a naturally abundant clay mineral, continues to attract interest due to its cost-effectiveness, chemical stability, and compatibility with scalable fabrication techniques for membrane applications.
Key industry players are intensifying research into the modification of kaolinite membranes to improve permeability, mechanical strength, and fouling resistance. For instance, KERAFOL Keramische Folien GmbH & Co. KG is advancing the use of composite kaolinite membranes by incorporating functional additives such as alumina and zirconia, targeting improved filtration efficiency in both water treatment and industrial effluent management. Similarly, Mantec Filtration is exploring hybrid kaolinite membranes with hierarchical pore structures, aiming for enhanced selectivity and durability in harsh chemical environments.
On the sustainability front, circular economy principles are influencing membrane engineering. Companies are evaluating the use of recycled kaolinite sourced from industrial waste streams, reducing both raw material costs and environmental impact. Pall Corporation is piloting kaolinite-based filtration modules for decentralized water reuse systems, aligning with global water scarcity mitigation goals.
Digitalization and smart manufacturing are set to further disrupt the sector. Process automation, real-time monitoring, and AI-driven design optimization are being integrated into production lines, resulting in finer control over membrane microstructure and reproducibility. Sibelco, a major supplier of industrial minerals including kaolinite, is investing in digital supply chain management and quality assurance systems to ensure consistency and traceability in membrane-grade kaolinite supplies.
Looking ahead, the next few years are expected to see:
- Widespread adoption of low-energy sintering techniques to minimize carbon footprint during membrane fabrication.
- Increased market penetration of kaolinite membranes in decentralized and modular filtration systems, particularly in regions facing acute water stress.
- Collaborations between membrane manufacturers, mineral suppliers, and end-users to develop application-specific solutions—especially for pharmaceutical, food & beverage, and advanced wastewater treatment sectors.
To remain competitive, stakeholders should prioritize R&D in functionalization strategies, partner with digital technology providers, and commit to sustainable sourcing of kaolinite. The convergence of materials innovation, digitalization, and eco-conscious engineering will shape the disruptive trajectory of kaolinite-based ceramic membrane engineering through 2025 and beyond.
Sources & References
- NGK INSULATORS, LTD.
- Pall Corporation
- Cerafiltec
- Mantec Filtration
- LiqTech International, Inc.
- Membrane Solutions LLC
- KeraNor AS
- Membranes International Inc.
- Imerys
- Alfa Laval
- Imerys
- Ceramic Technology, Inc.
- Morgan Advanced Materials
- European Union
- Ministry of Ecology and Environment of the People’s Republic of China
- SUEZ
- Sibelco