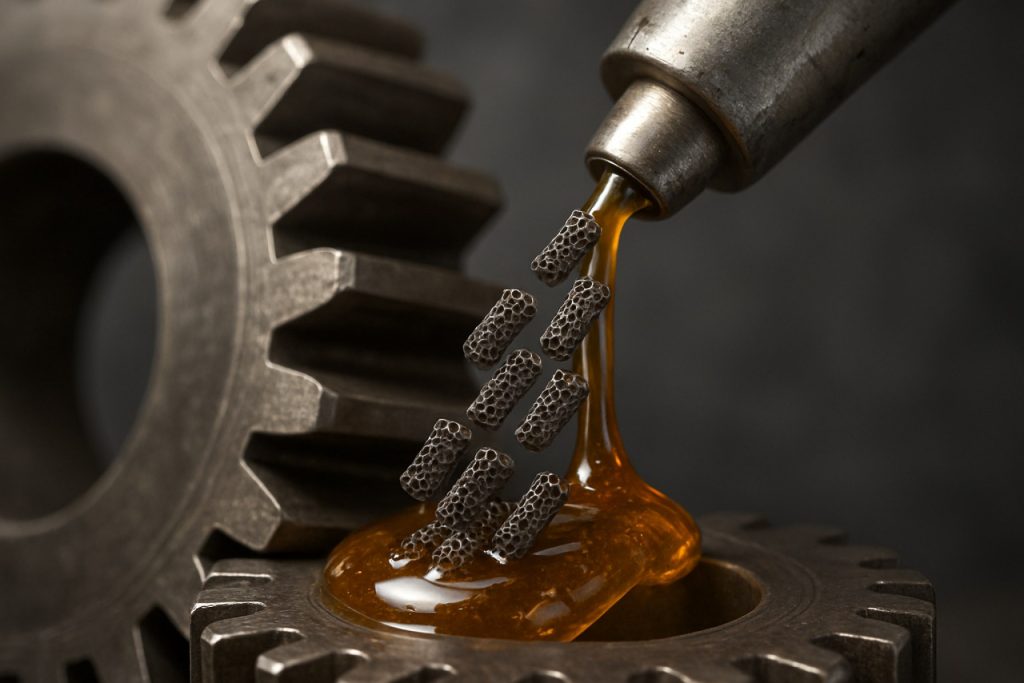
Table of Contents
- Executive Summary: Key Findings & Market Highlights
- Technology Overview: Nanotube-Based Antiwear Lubricants Explained
- 2025 Market Size & Regional Breakdown
- Key Players & Industry Initiatives (e.g., tribology.org, ieee.org, asme.org, nanolub.com)
- Emerging Applications: Automotive, Aerospace, Manufacturing, and Beyond
- R&D Pipeline: Innovations, Patents, and Academic Collaborations
- Performance Benchmarks: Lab Results vs. Real-World Case Studies
- Regulatory, Safety, and Environmental Considerations
- Market Forecasts & Investment Opportunities Through 2030
- Future Outlook: Challenges, Disruptors, and Long-Term Vision
- Sources & References
Executive Summary: Key Findings & Market Highlights
Antiwear nanotube lubricant engineering is witnessing accelerated advancements in 2025, driven by the convergence of nanotechnology, materials science, and the pressing demand for enhanced tribological performance across automotive, aerospace, and heavy industry sectors. The integration of carbon-based nanotubes, notably multi-walled carbon nanotubes (MWCNTs) and boron nitride nanotubes (BNNTs), into lubricant formulations has emerged as a pivotal innovation, delivering marked improvements in friction reduction, wear resistance, and operational longevity.
- In 2025, leading lubricant manufacturers such as Shell and TotalEnergies are piloting commercial blends incorporating nanomaterials, aiming for improved antiwear properties and fuel efficiency in both automotive and industrial machinery applications.
- Early field trials by ExxonMobil have demonstrated a reduction of up to 40% in component wear rates when using nanotube-enhanced lubricants compared to conventional formulations, with supplementary benefits including lower oil volatility and superior performance under extreme pressure and temperature conditions.
- In aerospace, NASA continues to collaborate with advanced materials suppliers to evaluate BNNT-based lubricants for critical moving components, seeking to extend maintenance intervals and reduce lubricant replacement frequency in spaceflight and satellite systems.
- The 2025-2027 outlook anticipates broader adoption as suppliers such as Arkema and NanoAmor increase production capacities for high-purity nanotubes, addressing previous supply constraints and enabling scalable, cost-effective lubricant enhancements.
- Regulatory developments are shaping the landscape; the American Petroleum Institute (API) and European Automobile Manufacturers’ Association (ACEA) are actively updating lubricant certification protocols to reflect the unique performance and safety profiles of nanotube-infused formulations.
Despite these advances, challenges remain regarding nanoparticle dispersion stability, long-term environmental impacts, and recyclability. Nevertheless, the sector is poised for robust growth, with ongoing R&D and early commercial deployments signaling a transformative period for lubricant engineering. Industry consensus suggests that by 2027, nanotube lubricants will become an integral element in high-demand, mission-critical applications, setting new standards for energy efficiency and mechanical durability.
Technology Overview: Nanotube-Based Antiwear Lubricants Explained
Antiwear nanotube lubricant engineering represents a frontier in tribological materials science, leveraging the remarkable mechanical and chemical properties of nanostructured additives—most notably carbon nanotubes (CNTs) and, increasingly, boron nitride nanotubes (BNNTs)—to reduce friction and wear in industrial machinery. As of 2025, the technology has progressed from laboratory-scale demonstrations to early-stage commercial adoption, driven by the need for higher equipment reliability, energy efficiency, and extended maintenance intervals.
The core principle behind nanotube-based antiwear lubricants is the incorporation of nanoscale tubular structures into conventional oils and greases. These nanotubes, owing to their high aspect ratio, exceptional tensile strength, and surface chemistry, form protective tribofilms on contacting surfaces during operation. This mitigates direct metal-to-metal contact, diminishes adhesive wear, and can even provide self-healing effects under extreme pressure or temperature.
Current formulations typically employ multi-walled carbon nanotubes (MWCNTs) due to their cost-effectiveness and ease of dispersion. Companies such as Arkema have scaled the production of MWCNTs for industrial applications, including their use as friction modifiers in lubricants. Meanwhile, interest in BNNTs is rising, especially for high-temperature or electrically insulating environments, with producers like BNNT, LLC supplying material for advanced lubricant R&D.
Empirical data from recent deployments show that adding 0.1–1.0 wt% of functionalized nanotubes to synthetic base oils can reduce the coefficient of friction by up to 40% and wear scar diameter by 20–60% compared to base oils alone. Trials conducted in heavy-duty engines and gearboxes have demonstrated not only improved antiwear performance but also lower operating temperatures and extended oil drain intervals, as reported by industrial lubricant formulators working with The Lubrizol Corporation and others.
Nanotube dispersion remains a key engineering challenge, as agglomeration can negate tribological benefits or cause filter clogging. Recent advances in surface functionalization and dispersant chemistry—often in collaboration with suppliers like Evonik Industries—are enabling more stable and scalable formulations suitable for automotive, aerospace, and wind energy applications.
Looking ahead, the next few years will likely see broader deployment of nanotube-enhanced lubricants in high-value, mission-critical sectors first, followed by gradual cost reductions and regulatory approvals paving the way for mainstream adoption. In parallel, sustainability initiatives are driving research into biodegradable base oils and greener nanotube production methods, as seen in pilot projects supported by Shell and academic-industry consortia. The convergence of nanomaterials engineering and smart lubrication systems is also anticipated, with real-time monitoring of lubricant condition and adaptive dosing of nanotube additives.
2025 Market Size & Regional Breakdown
As of 2025, the global market for antiwear nanotube lubricant engineering is entering a phase of accelerated commercialization, marked by increased adoption across automotive, industrial, and heavy machinery sectors. The integration of carbon nanotubes (CNTs) and other nanostructured additives in lubricants is driven by the demand for enhanced durability, reduced friction, and longer equipment lifespan—key factors for sectors facing sustainability and efficiency pressures.
Recent data suggest that North America and Europe remain at the forefront of both R&D and early commercial deployment. U.S.-based companies like American Carbon Company and ENSOCORE have expanded their nanotube-enhanced lubricant lines, targeting automotive OEMs and industrial maintenance providers. In Europe, Carbon Waters in France has reported scaling up production of water-dispersed CNT concentrates for integration into next-generation lubricants, citing growing partnerships with German and Scandinavian manufacturers in 2024–2025.
Asia-Pacific is projected to see the fastest growth rate through 2025, fueled by aggressive technology adoption in China, Japan, and South Korea. Chinese lubricant suppliers, led by Sinopec, have unveiled new CNT lubricant formulations tailored for high-load industrial operations and electric vehicle (EV) platforms. In Japan, Showa Denko K.K. continues to refine its nanomaterial production, supplying both domestic and international lubricant formulators. South Korean interest is highlighted by collaborations between LG Chem and local automotive manufacturers to test CNT-infused greases for electric drivetrain components.
Latin America and the Middle East are emerging as promising but secondary markets, as regional oil companies and mining operators seek to extend equipment lifespans under harsh operating conditions. Petrobras in Brazil has initiated pilot projects evaluating nanolubricant performance for offshore drilling equipment, and Middle Eastern petrochemical firms are beginning to explore similar initiatives.
Looking forward, market analysts expect the global antiwear nanotube lubricant sector to surpass several hundred million USD in annual revenues by 2027, with CAGR estimates in the high single digits. Regional growth will be shaped by regulatory frameworks, OEM partnerships, and the pace of nanomaterial scale-up. As intellectual property portfolios expand and supply chains mature, the next few years are likely to see further regional diversification and intensified competition among established chemical and lubricant producers.
Key Players & Industry Initiatives (e.g., tribology.org, ieee.org, asme.org, nanolub.com)
Antiwear nanotube lubricant engineering is experiencing accelerated momentum in 2025, driven by collaborative efforts between research organizations, manufacturing companies, and industry bodies. A notable recent trend is the increasing participation of major lubricant and additive producers in the development and commercialization of nanotube-enhanced oils and greases for automotive, industrial, and aerospace applications.
- Nanotech Industrial Solutions (NANOLUB) continues to be a pioneering force, leveraging their patented inorganic fullerene-like tungsten disulfide (IF-WS2) nanotubes as antiwear additives. In 2025, the company has expanded partnerships with automotive and heavy machinery OEMs to field-test their NanoLub-based lubricants, reporting significant reductions in friction and wear in real-world fleet trials.
- Shell Global (Shell) has announced new R&D investments specifically targeting carbon nanotube (CNT) dispersions for next-generation synthetic oils. Their 2025 technical whitepaper outlines a roadmap for scaling up CNT-modified lubricants, aiming for commercial deployment in high-load engine oils by 2027.
- American Society of Mechanical Engineers (ASME) and the Society of Tribologists and Lubrication Engineers (STLE) have increased their focus on nanotube lubricants in 2025 conference programming and technical standards development. Both organizations are facilitating cross-sector dialogue to address issues of additive dispersion, long-term stability, and eco-toxicity.
- Tribology Society of India (Tribology Society of India) is supporting pilot projects with public and private sector partners to evaluate the lifecycle impacts and tribological performance of nanotube-infused greases in railway and power plant applications.
- IEEE Nanotechnology Council (IEEE Nanotechnology Council) is sponsoring new working groups in 2025 focused on standardizing characterization techniques for nanotube lubricant additives, aiming to harmonize testing protocols across global markets.
Looking ahead, the outlook for antiwear nanotube lubricants is buoyed by these industry initiatives and collaborations. With field validation data accruing and standardization efforts underway, broader adoption is likely within heavy-duty and precision engineering sectors by 2027. However, regulatory bodies and industry groups continue to monitor environmental and health impacts, emphasizing the need for continued research and transparent supply chain practices.
Emerging Applications: Automotive, Aerospace, Manufacturing, and Beyond
Antiwear nanotube lubricant engineering is rapidly advancing, with significant implications across automotive, aerospace, and manufacturing sectors. In 2025 and the coming years, the integration of carbon nanotubes (CNTs) and related nanostructures into lubricant formulations is expected to shift from laboratory-scale demonstrations to real-world industrial applications, propelled by demonstrated enhancements in friction reduction, wear resistance, and thermal stability.
In the automotive sector, several OEMs and Tier 1 suppliers are moving from exploratory research to pilot-scale validation of nanotube-enhanced oils and greases. For example, Schaeffler Group has reported ongoing field trials of CNT-infused lubricants targeting extended service intervals and reduced component wear in electric vehicle drivetrains. These lubricants are engineered to leverage the rolling and mending effects of nanotubes, offering up to 40% reduction in friction coefficients and marked improvements in load-carrying capacity under boundary lubrication regimes.
In aerospace, where extreme temperature and load conditions challenge conventional lubricants, organizations such as NASA are investigating the deployment of boron nitride nanotube (BNNT) additives in critical moving assemblies. Early results indicate that BNNT-based lubricants maintain structural integrity and antiwear performance at temperatures exceeding 400°C, addressing key limitations of traditional mineral and synthetic oils. This development is critical for next-generation propulsion systems and spaceborne mechanisms, where maintenance opportunities are limited.
Manufacturing industries are also exploring nanotube lubricant engineering to optimize high-speed machining and forming processes. Industrial lubricant producers like FUCHS Group are developing formulations with multiwalled carbon nanotubes (MWCNTs) to reduce tool wear and improve surface finish in metalworking operations. Pilot studies have shown up to 60% reduction in wear scar diameter and extended tool life, directly impacting production efficiency and cost.
Beyond these sectors, there is growing interest in deploying nanotube-based lubricants in wind turbines, robotics, and medical devices—applications where reliability and longevity are paramount. Over the next few years, industry collaborations will likely accelerate, as material suppliers such as Arkema scale up nanotube production and formulate dispersions that meet the stringent purity and stability requirements for industrial lubricants.
The outlook for antiwear nanotube lubricant engineering in 2025 and beyond is marked by a transition from proof-of-concept to adoption in high-value, mission-critical applications. Regulatory considerations, cost optimization, and long-term environmental impacts remain under evaluation, but the potential for transformative improvements in durability and energy efficiency is driving sector-wide momentum.
R&D Pipeline: Innovations, Patents, and Academic Collaborations
As the demand for high-performance, sustainable lubrication solutions intensifies across automotive, aerospace, and heavy machinery sectors, the research and development (R&D) pipeline for antiwear nanotube lubricant engineering has accelerated markedly in 2025. Nanotube-enhanced lubricants—primarily leveraging carbon nanotubes (CNTs) and, increasingly, boron nitride nanotubes (BNNTs)—are now at the forefront of tribological innovation, promising superior antiwear characteristics, thermal stability, and reduced environmental impact.
Several major industrial entities and academic consortia are actively advancing the development and commercialization of nanotube-based lubricants. The Lubrizol Corporation and Chevron have filed new patent families in 2024 and early 2025, focusing on the functionalization of multi-walled CNTs to improve dispersion in synthetic base oils and optimize tribofilm formation under high-stress conditions. Concurrently, BASF is collaborating with university partners to investigate the use of BNNTs as non-toxic, high-efficiency antiwear additives, capitalizing on their high thermal conductivity and chemical inertness.
On the academic front, the National Institute for Materials Science (NIMS) in Japan has partnered with Toyota Motor Corporation in a multi-year research program aimed at integrating nanotube-lubricant systems into next-generation engine and drivetrain platforms. Early 2025 results show reductions in friction coefficients by up to 30% versus conventional zinc dialkyldithiophosphate (ZDDP) additives, with no adverse impact on emission control device compatibility.
Intellectual property activity reflects this momentum. Patent filings tracked by United States Patent and Trademark Office (USPTO) and European Patent Office (EPO) indicate more than 200 active patent families globally related to nanotube lubricant formulations as of Q2 2025, up 20% year-over-year. Notably, Arkema has secured patents for scalable processes that ensure nanotube additives remain stably suspended in a variety of lubricant chemistries, addressing a long-standing barrier to commercialization.
Looking ahead, collaborative industry-university initiatives such as the new EU Horizon program “NanoLube2025” are poised to accelerate technology transfer, standardization, and pilot-scale demonstrations over the next 2–3 years. With regulatory scrutiny on traditional antiwear additives intensifying, the pipeline of nanotube lubricant innovations is expected to play a pivotal role in shaping the future of high-performance and environmentally responsible lubrication technologies.
Performance Benchmarks: Lab Results vs. Real-World Case Studies
The integration of nanotube additives, particularly carbon nanotubes (CNTs) and boron nitride nanotubes (BNNTs), into lubricants has shown substantial promise in both laboratory and field environments. In 2025, performance benchmarks are being established through a blend of controlled tribological testing and real-world industrial applications, highlighting both the advantages and challenges of antiwear nanotube lubricant engineering.
Laboratory tests have consistently demonstrated that nanotube-enhanced lubricants can significantly reduce friction and wear rates compared to conventional formulations. In controlled tribometer experiments, multi-walled carbon nanotube (MWCNT) additives have delivered a reduction in coefficient of friction by 20–40% and wear scar diameter by up to 50%, depending on base oil and concentration used. For example, Chevron and Schaeffler Group have both documented tribology research programs where CNT-infused lubricants outperformed standard oils, particularly under high-load conditions.
In real-world environments, the performance gains are now being validated across sectors such as automotive, heavy machinery, and wind energy. FUCHS Group has piloted CNT and BNNT lubricant blends in industrial gearboxes and reported a 10–15% increase in component lifespan along with measurable energy savings due to lower frictional losses. Similarly, Sinopec has conducted field trials in transport fleets, noting reduced engine wear rates and cleaner oil samples after extended oil change intervals.
Despite the positive results, discrepancies between lab and field performance persist. Laboratory tests often use idealized surfaces and controlled loads, while real-world variables—such as contamination, temperature fluctuations, and mixed-material contacts—can attenuate the benefits of nanotube additives. For instance, TotalEnergies has observed that the antiwear advantages of nanotube lubricants diminish in highly contaminated environments or when compatibility with certain seals and metals is not optimal.
Looking ahead, the focus for 2025 and beyond is on refining additive dispersion technologies and tailoring nanotube surface chemistry to ensure stable, reproducible performance in diverse operating environments. Major lubricant producers are investing in scalable production of functionalized nanotubes and in-situ monitoring systems for lubricant health, as seen in ongoing work at Schaeffler Group’s Advanced Tribology labs. The outlook is for wider adoption in high-value and mission-critical applications—such as wind turbine gearboxes and electric vehicle drivetrains—where the cost-benefit of extended equipment life and reduced maintenance is most compelling.
Regulatory, Safety, and Environmental Considerations
As the deployment of antiwear nanotube lubricants accelerates in 2025, regulatory, safety, and environmental considerations are becoming increasingly prominent for manufacturers, end-users, and legislators. Nanotube-based lubricants, typically incorporating carbon nanotubes (CNTs) or boron nitride nanotubes (BNNTs), offer exceptional friction reduction and wear resistance but introduce new challenges in occupational safety and environmental stewardship.
In terms of regulation, the U.S. Environmental Protection Agency (EPA) continues to oversee the introduction of nanomaterials under the Toxic Substances Control Act (TSCA). As of 2025, the EPA requires pre-manufacture notification and detailed risk assessments for new nanotube materials, with particular focus on persistence, bioaccumulation, and potential toxicity. The European Union’s European Chemicals Agency (ECHA) enforces similar registration under REACH, mandating nanoscale-specific hazard, exposure, and lifecycle data for all nanotube-containing lubricants.
Occupational safety is a key concern, as inhalation or dermal exposure to nanoparticles during production, formulation, or application may pose health risks. Companies such as Arkema and OZKEM, both involved in nanotube production and supply, have adopted rigorous workplace controls and personal protective equipment standards. These include closed-system processing, advanced ventilation, and real-time particulate monitoring to minimize worker exposure.
Disposal and lifecycle environmental impacts are under close scrutiny. While CNTs and BNNTs are chemically stable and not readily biodegradable, their fate in wastewater, soils, and the broader environment remains incompletely characterized. Industry leaders such as Nanocyl are collaborating with regulatory bodies to develop standardized testing protocols for environmental persistence, leaching, and ecotoxicity of nanotube additives. Furthermore, the lubricants industry is increasingly aligning with circular economy principles, seeking to recover and reuse spent lubricants and minimize environmental release of nanomaterials.
Looking forward, international harmonization of nanosafety standards is anticipated, as organizations like the International Organization for Standardization (ISO) continue to update technical standards for nanomaterial handling, labeling, and risk communication. In the next few years, compliance with evolving regulations and transparent risk management will be essential for market access and public acceptance of antiwear nanotube lubricant technologies.
Market Forecasts & Investment Opportunities Through 2030
The antiwear nanotube lubricant sector is poised for significant advancements and market growth through 2030, driven by innovations in nanomaterial engineering and increasing demand for high-performance, sustainable lubricants across key industries such as automotive, manufacturing, and energy. As of 2025, early adopters in the automotive and industrial machinery sectors are integrating nanotube-based additives to enhance wear resistance, reduce friction, and extend component lifespans, responding to stricter regulatory standards and the push for longer maintenance intervals.
Leading manufacturers of carbon nanotubes (CNTs) and nanomaterials, such as Arkema and Nanocyl SA, have increased production capacities and diversified their nanotube offerings to meet the evolving needs of lubricant formulators. These companies report a growing share of their CNT output being directed toward lubricant applications, particularly those targeting antiwear performance in high-load and high-temperature environments. For example, Arkema’s Graphistrength® multiwall carbon nanotubes are engineered for compatibility with both synthetic and mineral oil bases, addressing the broad market requirements of industrial lubricants.
Investment opportunities are emerging in both upstream nanotube production and downstream formulation of specialty lubricants. With global regulations tightening on the use of traditional zinc-dialkyldithiophosphate (ZDDP) antiwear additives due to environmental concerns, nanotube-enhanced lubricants are positioned as eco-friendly alternatives. Companies such as The Lubrizol Corporation have initiated research collaborations focused on leveraging nanotechnology to develop next-generation lubricant additives, aiming to deliver superior antiwear properties while reducing environmental impact.
Projections for the period through 2030 indicate a compound annual growth rate (CAGR) in the high single digits for the antiwear nanotube lubricant market segment, with the Asia-Pacific region expected to lead in adoption due to its robust manufacturing base and aggressive industrial modernization programs. Strategic partnerships between nanomaterial suppliers and lubricant formulators are anticipated to accelerate commercialization, with pilot projects and field trials already underway in sectors such as wind energy and heavy-duty transport.
Looking ahead, ongoing improvements in nanotube dispersion technologies and functionalization are likely to lower formulation costs and enhance compatibility with a wider range of lubricant chemistries. As a result, antiwear nanotube lubricants are expected to capture a larger share of the high-performance and specialty lubricant markets by 2030, supported by continued investment from material science leaders and end-user industries seeking longer equipment lifespans and reduced maintenance costs.
Future Outlook: Challenges, Disruptors, and Long-Term Vision
The future outlook for antiwear nanotube lubricant engineering, as we enter 2025 and look towards the following years, is defined by a landscape of both significant promise and substantial challenges. As the demand for higher efficiency, sustainability, and durability in tribological systems continues to grow across industries such as automotive, aerospace, and manufacturing, nanotube-based lubricants are emerging as a disruptive force in the field.
-
Key Challenges:
Despite their clear potential, the widespread adoption of nanotube-enhanced lubricants faces hurdles in terms of scalability, cost, and regulatory approval. The commercial production of high-quality carbon and boron nitride nanotubes at industrial scales remains technically demanding and costly, though ongoing investments by leading companies such as Arkema and OCSiAl are driving improvements in synthesis and dispersion technologies. Additionally, ensuring uniform dispersion of nanotubes within base oils to prevent agglomeration is a persistent challenge being addressed through advanced surface functionalization and surfactant strategies. -
Disruptive Innovations:
In 2025, industry leaders and research organizations are focusing on eco-friendly and “smart” lubricant solutions. For example, Chevron and Schaeffler Group are exploring the integration of nanotubes with biodegradable base oils and the development of lubricants that adapt their antiwear properties under varying loads and temperatures. The use of digital twins and real-time monitoring, as promoted by Schaeffler Group, enables predictive maintenance and optimization of lubricant performance, further advancing nanotube lubricant engineering. -
Sustainability and Regulation:
Environmental and health concerns regarding nanomaterials have prompted increased scrutiny from regulatory agencies and industry organizations such as American Petroleum Institute (API). The next few years will likely see the establishment of clearer standards for the safe production, handling, and disposal of nanotube-based lubricants, shaping industry practices and market acceptance. -
Long-Term Vision:
Looking ahead, the convergence of advanced nanomaterial engineering, data-driven maintenance, and sustainable formulation strategies positions antiwear nanotube lubricants as a cornerstone of future tribological systems. As production costs decline and regulatory clarity improves, the integration of nanotube lubricants into mainstream applications—ranging from high-performance electric vehicles to wind turbines—is expected to accelerate. Ongoing collaboration between material suppliers, technology integrators, and end-users will be crucial for realizing the full potential of these next-generation lubricants.
In summary, antiwear nanotube lubricant engineering stands at the threshold of transformative growth, contingent on overcoming technical, economic, and regulatory challenges while capitalizing on the momentum of innovation and sustainability trends.
Sources & References
- Shell
- TotalEnergies
- ExxonMobil
- NASA
- Arkema
- American Petroleum Institute (API)
- European Automobile Manufacturers’ Association (ACEA)
- BNNT, LLC
- The Lubrizol Corporation
- Evonik Industries
- Carbon Waters
- Petrobras
- ASME
- Tribology Society of India
- Schaeffler Group
- FUCHS Group
- BASF
- National Institute for Materials Science (NIMS)
- Toyota Motor Corporation
- European Patent Office (EPO)
- European Chemicals Agency (ECHA)
- OZKEM
- International Organization for Standardization (ISO)
- OCSiAl