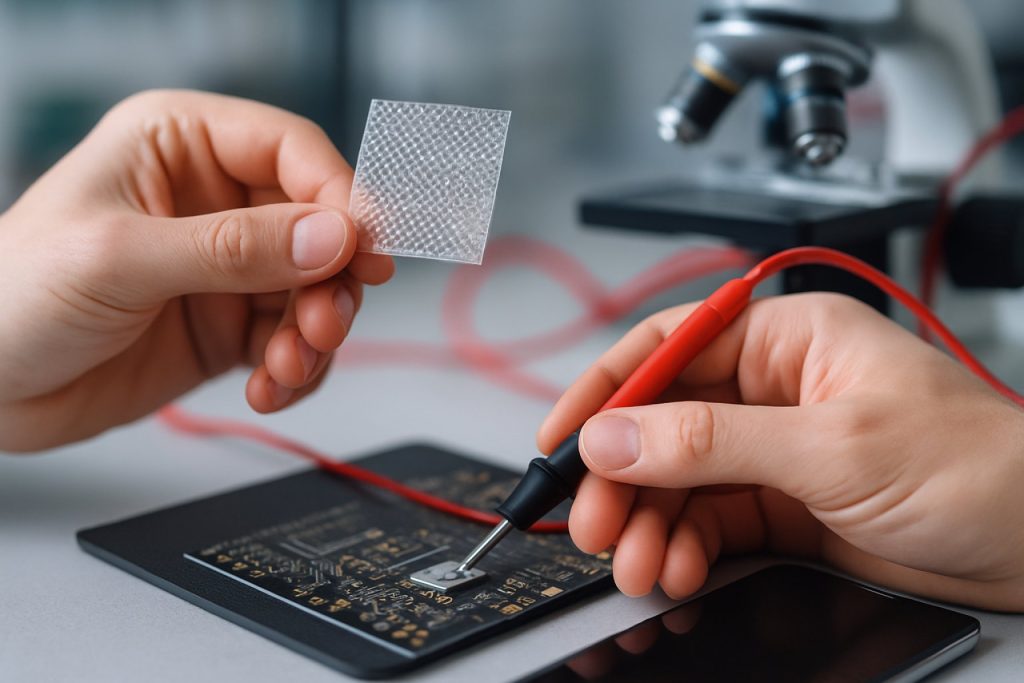
Piezoelectric Nanomaterials Engineering in 2025: Unleashing Ultra-Efficient Energy Harvesting and Sensing for a Smarter, Greener Future. Explore the Breakthroughs, Market Dynamics, and Strategic Opportunities Shaping the Next Five Years.
- Executive Summary: Key Trends and Market Outlook (2025–2030)
- Technology Landscape: Innovations in Piezoelectric Nanomaterials
- Market Size and Growth Forecasts Through 2030
- Leading Players and Strategic Partnerships (e.g., piezomaterials.com, ieee.org)
- Emerging Applications: IoT, Wearables, and Medical Devices
- Manufacturing Advances and Scalability Challenges
- Regulatory Environment and Industry Standards (e.g., ieee.org, asme.org)
- Sustainability and Environmental Impact
- Investment, Funding, and M&A Activity
- Future Outlook: Disruptive Opportunities and Roadmap to 2030
- Sources & References
Executive Summary: Key Trends and Market Outlook (2025–2030)
The field of piezoelectric nanomaterials engineering is poised for significant advancements between 2025 and 2030, driven by rapid innovation in materials science, miniaturization, and the expanding demand for energy harvesting and sensing technologies. Piezoelectric nanomaterials—such as nanowires, nanoparticles, and thin films—are increasingly being integrated into next-generation devices for applications ranging from medical implants to wearable electronics and industrial sensors.
A key trend is the transition from traditional bulk piezoelectric ceramics, like lead zirconate titanate (PZT), to lead-free and flexible nanomaterials. Companies such as Murata Manufacturing Co., Ltd. and TDK Corporation are at the forefront, investing in the development of advanced piezoelectric films and composites that offer improved biocompatibility, flexibility, and environmental sustainability. These materials are enabling the creation of ultra-thin, conformable sensors and actuators suitable for integration into smart textiles and biomedical devices.
The proliferation of the Internet of Things (IoT) is accelerating demand for self-powered sensors, where piezoelectric nanomaterials play a crucial role in energy harvesting. Piezo Systems, Inc. and Kureha Corporation are actively commercializing nanomaterial-based energy harvesters that convert ambient mechanical vibrations into usable electrical energy, supporting maintenance-free operation of distributed sensor networks.
In the medical sector, piezoelectric nanomaterials are being engineered for high-sensitivity biosensors and implantable devices. Robert Bosch GmbH and STMicroelectronics are developing MEMS (Micro-Electro-Mechanical Systems) platforms that leverage nanostructured piezoelectric films for real-time physiological monitoring and minimally invasive diagnostics.
Looking ahead, the market outlook for piezoelectric nanomaterials engineering is robust. Industry analysts anticipate double-digit annual growth rates through 2030, fueled by ongoing R&D, regulatory support for lead-free materials, and the convergence of nanotechnology with flexible electronics. Strategic partnerships between material suppliers, device manufacturers, and end-users are expected to accelerate commercialization and standardization efforts. As manufacturing processes mature and costs decline, piezoelectric nanomaterials are set to become foundational components in a wide array of smart, sustainable technologies.
Technology Landscape: Innovations in Piezoelectric Nanomaterials
The field of piezoelectric nanomaterials engineering is experiencing rapid innovation in 2025, driven by advances in material synthesis, device integration, and application-specific customization. Piezoelectric nanomaterials—such as nanowires, nanoparticles, and thin films—are being engineered with unprecedented control over their crystalline structure, composition, and surface properties, enabling enhanced electromechanical coupling and miniaturization for next-generation devices.
A significant trend is the shift toward lead-free piezoelectric nanomaterials, motivated by environmental regulations and sustainability goals. Companies like TDK Corporation and Murata Manufacturing Co., Ltd. are actively developing barium titanate (BaTiO3) and potassium sodium niobate (KNN) nanomaterials as alternatives to traditional lead zirconate titanate (PZT). These materials are being tailored at the nanoscale to achieve high piezoelectric coefficients and thermal stability, making them suitable for sensors, actuators, and energy harvesting devices.
In terms of fabrication, scalable bottom-up synthesis methods—such as hydrothermal growth and sol-gel processing—are being refined to produce uniform nanostructures with controlled orientation and aspect ratios. NGK Insulators, Ltd. is leveraging advanced ceramic processing to integrate piezoelectric nanomaterials into multilayer structures for high-performance electronic components. Meanwhile, STMicroelectronics is focusing on the integration of piezoelectric nanofilms with CMOS-compatible processes, enabling the mass production of MEMS and NEMS devices for consumer electronics and industrial applications.
Another area of innovation is the functionalization of piezoelectric nanomaterials for biomedical and wearable technologies. Companies such as Samsung Electronics are exploring flexible piezoelectric nanofiber composites for self-powered sensors and health monitoring patches. These materials are engineered to maintain high sensitivity and mechanical durability under repeated deformation, addressing key challenges in wearable device design.
Looking ahead, the outlook for piezoelectric nanomaterials engineering is robust. The convergence of nanofabrication, materials informatics, and additive manufacturing is expected to accelerate the discovery and deployment of novel piezoelectric nanostructures. Industry leaders are investing in pilot-scale production lines and collaborative R&D initiatives to bring advanced piezoelectric nanomaterials to market, with anticipated breakthroughs in energy harvesting, precision actuation, and next-generation IoT devices over the next few years.
Market Size and Growth Forecasts Through 2030
The global market for piezoelectric nanomaterials engineering is poised for robust growth through 2030, driven by expanding applications in electronics, healthcare, energy harvesting, and advanced sensors. As of 2025, the sector is witnessing increased investment from both established materials manufacturers and innovative startups, reflecting the rising demand for miniaturized, high-performance piezoelectric components.
Key industry players such as Murata Manufacturing Co., Ltd., TDK Corporation, and Piezotech (an Arkema company) are actively scaling up their research and production capacities for advanced piezoelectric materials, including nanostructured ceramics and polymers. These companies are focusing on the development of lead-free and flexible piezoelectric nanomaterials to meet stringent environmental regulations and the evolving needs of wearable electronics and medical devices.
In 2025, the market is characterized by a surge in demand for piezoelectric nanomaterials in energy harvesting applications, particularly for powering wireless sensors and IoT devices. Murata Manufacturing Co., Ltd. has reported increased shipments of piezoelectric components for use in compact energy harvesting modules, while TDK Corporation continues to expand its product portfolio with nanomaterial-based actuators and sensors targeting automotive and industrial automation sectors.
The Asia-Pacific region, led by Japan, South Korea, and China, remains at the forefront of both production and consumption of piezoelectric nanomaterials. Companies such as Murata Manufacturing Co., Ltd. and TDK Corporation are leveraging their established manufacturing infrastructure and R&D capabilities to maintain a competitive edge. Meanwhile, European firms like Piezotech are pioneering the commercialization of piezoelectric polymers for flexible electronics and smart textiles.
Looking ahead to 2030, the market is expected to experience a compound annual growth rate (CAGR) in the high single digits, underpinned by the proliferation of smart devices, advancements in nanofabrication techniques, and the integration of piezoelectric nanomaterials into next-generation biomedical implants and environmental monitoring systems. Strategic collaborations between material suppliers, device manufacturers, and research institutions are anticipated to accelerate innovation and commercialization, further expanding the addressable market for piezoelectric nanomaterials engineering.
Leading Players and Strategic Partnerships (e.g., piezomaterials.com, ieee.org)
The landscape of piezoelectric nanomaterials engineering in 2025 is shaped by a dynamic interplay of established industry leaders, innovative startups, and strategic collaborations across sectors such as electronics, healthcare, and energy harvesting. The field is characterized by rapid advancements in material synthesis, device miniaturization, and integration into next-generation applications.
Among the leading players, PI Ceramic (a division of Physik Instrumente) continues to be a global frontrunner in the development and supply of advanced piezoelectric ceramics and nanomaterials. The company’s ongoing investments in research and manufacturing infrastructure have enabled the production of high-performance lead zirconate titanate (PZT) and lead-free alternatives, catering to the growing demand for environmentally friendly solutions in medical ultrasound, precision actuators, and microelectromechanical systems (MEMS).
Another significant contributor is Murata Manufacturing Co., Ltd., which leverages its expertise in multilayer ceramic technology to engineer piezoelectric nanomaterials for compact sensors and actuators. Murata’s strategic focus on miniaturization and integration has resulted in partnerships with electronics manufacturers and automotive suppliers, aiming to embed piezoelectric functionalities into wearables, IoT devices, and advanced driver-assistance systems (ADAS).
In the United States, Boston Piezo-Optics Inc. specializes in custom piezoelectric crystals and thin films, supporting both commercial and defense applications. Their collaborations with research institutions and OEMs have accelerated the translation of laboratory-scale nanomaterial innovations into scalable, market-ready components.
Strategic partnerships are increasingly pivotal in this sector. For example, alliances between material suppliers and device manufacturers are fostering the co-development of next-generation piezoelectric nanogenerators and flexible energy harvesters. Industry consortia and standards bodies such as the IEEE are also playing a crucial role by establishing interoperability standards and facilitating knowledge exchange through conferences and working groups.
Looking ahead, the next few years are expected to witness intensified collaboration between academia and industry, particularly in the development of lead-free and bio-compatible piezoelectric nanomaterials. Companies are anticipated to expand their intellectual property portfolios and form joint ventures to address emerging markets in biomedical implants, soft robotics, and smart infrastructure. As regulatory and sustainability pressures mount, the sector’s leading players are likely to prioritize green chemistry and lifecycle management in their R&D strategies, ensuring that piezoelectric nanomaterials remain at the forefront of advanced materials engineering.
Emerging Applications: IoT, Wearables, and Medical Devices
Piezoelectric nanomaterials engineering is rapidly advancing the frontiers of Internet of Things (IoT), wearable electronics, and medical devices, with 2025 marking a pivotal year for commercial and research-driven breakthroughs. The unique ability of piezoelectric nanomaterials—such as zinc oxide (ZnO) nanowires, barium titanate (BaTiO3) nanoparticles, and lead zirconate titanate (PZT) nanostructures—to convert mechanical energy into electrical signals at the nanoscale is enabling a new generation of self-powered, miniaturized, and highly sensitive devices.
In the IoT sector, piezoelectric nanomaterials are being integrated into sensor nodes to harvest ambient mechanical energy, reducing or eliminating the need for batteries. Companies like TDK Corporation and Murata Manufacturing Co., Ltd. are actively developing piezoelectric components for wireless sensor networks, focusing on ultra-low-power operation and long-term reliability. These advancements are crucial for smart infrastructure, environmental monitoring, and industrial automation, where maintenance-free operation is a key requirement.
Wearable technology is another area witnessing significant innovation. Flexible and stretchable piezoelectric nanomaterials are being engineered to conform to the human body, enabling continuous health monitoring and motion tracking. Samsung Electronics and LG Electronics are exploring the integration of piezoelectric nanogenerators into smart textiles and skin patches, aiming to power biosensors and communication modules directly from body movements. The focus in 2025 is on improving the durability, biocompatibility, and energy conversion efficiency of these materials to support real-world deployment.
In medical devices, piezoelectric nanomaterials are enabling minimally invasive implants and diagnostic tools. For example, Medtronic and Boston Scientific are investigating piezoelectric nanostructures for powering implantable sensors and stimulators, reducing the need for battery replacements and surgical interventions. Additionally, research collaborations with academic institutions are accelerating the translation of laboratory-scale innovations into clinical applications, such as self-powered pacemakers and smart wound dressings.
Looking ahead, the outlook for piezoelectric nanomaterials engineering in these emerging applications is highly promising. Ongoing efforts to scale up manufacturing, enhance material performance, and ensure regulatory compliance are expected to drive widespread adoption over the next few years. As industry leaders and startups alike invest in R&D and pilot production, the convergence of piezoelectric nanotechnology with IoT, wearables, and medical devices is set to transform the landscape of smart, autonomous, and personalized electronics.
Manufacturing Advances and Scalability Challenges
The engineering of piezoelectric nanomaterials has entered a pivotal phase in 2025, as manufacturers and research institutions strive to bridge the gap between laboratory-scale innovation and industrial-scale production. The demand for high-performance, flexible, and miniaturized piezoelectric devices—spanning applications from wearable electronics to energy harvesting—has intensified the focus on scalable, cost-effective manufacturing processes.
Recent years have seen significant progress in the synthesis of piezoelectric nanomaterials such as lead zirconate titanate (PZT), barium titanate (BaTiO3), and zinc oxide (ZnO) nanostructures. Companies like Murata Manufacturing Co., Ltd. and TDK Corporation have been at the forefront, leveraging advanced thin-film deposition techniques and sol-gel processes to produce high-quality piezoelectric films and nanostructures. These firms have invested heavily in refining sputtering, chemical vapor deposition (CVD), and atomic layer deposition (ALD) methods to achieve uniformity and reproducibility at scale, which are critical for device reliability and performance.
However, scalability remains a formidable challenge. The transition from batch-based laboratory synthesis to continuous, high-throughput manufacturing is hindered by issues such as material homogeneity, defect control, and integration with flexible substrates. For instance, the fabrication of aligned nanowire arrays—essential for maximizing piezoelectric output—requires precise control over growth parameters, which is difficult to maintain in large-scale reactors. Piezotech, a subsidiary of Arkema, has made notable strides in printable piezoelectric polymers, enabling roll-to-roll processing for flexible electronics, but the consistency of nanomaterial properties across large areas is still under active development.
Another key concern is the environmental and regulatory pressure to reduce or eliminate lead-based materials. This has spurred research and pilot-scale production of lead-free alternatives, such as potassium sodium niobate (KNN) and bismuth ferrite (BiFeO3), with companies like Noritake Co., Limited exploring scalable routes for these materials. Yet, matching the performance and processability of traditional lead-based ceramics remains a technical hurdle.
Looking ahead, the next few years are expected to witness the emergence of hybrid manufacturing approaches that combine top-down lithography with bottom-up self-assembly, as well as the integration of machine learning for process optimization. Industry collaborations and consortia, often involving major players such as Murata Manufacturing Co., Ltd. and TDK Corporation, are likely to accelerate the standardization of scalable processes. As these advances mature, the piezoelectric nanomaterials sector is poised for broader commercialization, particularly in the fields of IoT sensors, biomedical devices, and next-generation energy harvesters.
Regulatory Environment and Industry Standards (e.g., ieee.org, asme.org)
The regulatory environment and industry standards for piezoelectric nanomaterials engineering are rapidly evolving in 2025, reflecting the sector’s growing commercial relevance and the need for harmonized safety, performance, and interoperability benchmarks. As piezoelectric nanomaterials find increasing application in sensors, energy harvesting, medical devices, and microelectromechanical systems (MEMS), regulatory bodies and standards organizations are intensifying their focus on this field.
The Institute of Electrical and Electronics Engineers (IEEE) continues to play a pivotal role in standardizing testing protocols and performance metrics for piezoelectric materials, including those at the nanoscale. The IEEE 176 standard, which defines piezoelectric constants, is under review to incorporate new measurement techniques suitable for nanostructured materials. In parallel, the American Society of Mechanical Engineers (ASME) is updating its standards for the mechanical characterization of nanomaterials, with working groups focusing on the unique challenges posed by piezoelectric nanostructures, such as size-dependent properties and surface effects.
On the international front, the International Organization for Standardization (ISO) and the International Electrotechnical Commission (IEC) are collaborating on the development of standards for nanotechnology-enabled devices, including those utilizing piezoelectric nanomaterials. ISO/TC 229 (Nanotechnologies) and IEC/TC 113 (Nanotechnology for electrotechnical products and systems) are actively soliciting input from industry stakeholders to ensure that new standards address both safety and performance, particularly in biomedical and consumer electronics applications.
Regulatory agencies are also increasing oversight. The U.S. Food and Drug Administration (FDA) is updating its guidance for medical devices incorporating nanomaterials, with a focus on biocompatibility and long-term stability of piezoelectric nanostructures. In the European Union, the European Commission is reviewing the Registration, Evaluation, Authorisation and Restriction of Chemicals (REACH) regulation to better address the unique risks associated with engineered nanomaterials, including those with piezoelectric properties.
Looking ahead, the next few years are expected to bring further harmonization of standards, driven by the need for global supply chain integration and cross-border product certification. Industry consortia, such as the Semiconductor Industry Association, are advocating for clear, internationally recognized standards to accelerate commercialization and ensure safety. As piezoelectric nanomaterials move from laboratory to market, robust regulatory frameworks and consensus standards will be critical to fostering innovation while protecting public health and the environment.
Sustainability and Environmental Impact
Piezoelectric nanomaterials engineering is increasingly recognized for its potential to advance sustainability and reduce environmental impact across multiple sectors. As of 2025, the focus has shifted toward developing lead-free and environmentally benign piezoelectric materials, addressing concerns over the toxicity of traditional lead-based compounds such as lead zirconate titanate (PZT). Companies and research institutions are prioritizing the synthesis and scaling of alternatives like barium titanate, potassium sodium niobate, and zinc oxide nanostructures, which offer comparable piezoelectric performance without hazardous elements.
Major manufacturers, including Murata Manufacturing Co., Ltd. and TDK Corporation, have announced ongoing efforts to commercialize lead-free piezoelectric ceramics and nanomaterials, aiming to meet both regulatory requirements and growing customer demand for sustainable components. These companies are investing in advanced fabrication techniques, such as hydrothermal synthesis and sol-gel processing, to minimize energy consumption and waste during production. Additionally, Piezotech, a subsidiary of Arkema, is actively developing piezoelectric polymers and composites that are both flexible and recyclable, targeting applications in wearable electronics and energy harvesting.
The environmental benefits of piezoelectric nanomaterials extend beyond material composition. Their integration into energy harvesting devices enables the conversion of ambient mechanical energy—such as vibrations, pressure, or motion—into usable electrical power. This technology is being deployed in self-powered sensors for smart infrastructure, reducing reliance on batteries and lowering electronic waste. For example, Murata Manufacturing Co., Ltd. has introduced piezoelectric energy harvesting modules designed for wireless sensor networks, supporting the development of energy-autonomous systems in industrial and building automation.
Looking ahead, the next few years are expected to see further advancements in the eco-design of piezoelectric nanomaterials, with a focus on lifecycle assessment, recyclability, and the use of renewable feedstocks. Industry collaborations and standardization efforts, led by organizations such as the IEEE, are anticipated to accelerate the adoption of sustainable practices and materials. As regulatory pressures mount and end-users demand greener solutions, the piezoelectric nanomaterials sector is poised to play a pivotal role in the transition to a circular and low-carbon economy.
Investment, Funding, and M&A Activity
Investment and funding activity in the piezoelectric nanomaterials engineering sector has accelerated into 2025, driven by the convergence of advanced materials science, the Internet of Things (IoT), and the growing demand for energy harvesting solutions. The sector is characterized by a mix of established materials companies, deep-tech startups, and strategic corporate investors, all seeking to capitalize on the unique properties of piezoelectric nanomaterials for applications ranging from sensors and actuators to biomedical devices and wearable electronics.
In the past year, several notable funding rounds have been reported. For example, Murata Manufacturing Co., Ltd., a global leader in electronic components and piezoelectric ceramics, has increased its R&D investment in nanomaterials, with a focus on next-generation piezoelectric films and flexible devices. Similarly, TDK Corporation has announced expanded funding for its piezoelectric materials division, targeting innovations in thin-film and nanostructured piezoelectric elements for miniaturized sensors and energy harvesters.
Startups specializing in nanostructured piezoelectric materials have also attracted significant venture capital. In 2024, several early-stage companies in North America and Europe secured Series A and B funding rounds, often led by corporate venture arms of major electronics and materials firms. For instance, Piezotech (a subsidiary of Arkema) continues to receive strategic investment to scale up its piezoelectric polymer nanomaterials for flexible electronics and smart surfaces. Meanwhile, Noliac (a part of CTS Corporation) has reported increased funding for the development of multilayer piezoelectric components with nanoscale precision, aimed at high-performance medical and industrial applications.
Mergers and acquisitions (M&A) activity has also intensified. In late 2024, Murata Manufacturing Co., Ltd. completed the acquisition of a European nanomaterials startup specializing in lead-free piezoelectric nanowires, signaling a trend toward vertical integration and the securing of proprietary technologies. Additionally, TDK Corporation has entered into joint ventures with Asian research institutes to accelerate commercialization of nanostructured piezoelectric films.
Looking ahead to 2025 and beyond, the outlook for investment and M&A in piezoelectric nanomaterials engineering remains robust. The sector is expected to benefit from increased public and private funding, particularly as governments and industry consortia prioritize advanced materials for energy efficiency and next-generation electronics. Strategic partnerships between established manufacturers and innovative startups are likely to proliferate, further accelerating the pace of commercialization and market adoption.
Future Outlook: Disruptive Opportunities and Roadmap to 2030
The field of piezoelectric nanomaterials engineering is poised for significant transformation as we approach 2025 and look toward 2030. The convergence of advanced materials synthesis, scalable manufacturing, and integration with next-generation electronics is expected to unlock disruptive opportunities across multiple sectors. Key drivers include the demand for ultra-sensitive sensors, energy harvesting devices, and flexible electronics, all of which benefit from the unique properties of piezoelectric nanomaterials such as zinc oxide (ZnO) nanowires, lead zirconate titanate (PZT) nanoparticles, and emerging lead-free alternatives.
In 2025, leading manufacturers are accelerating the commercialization of piezoelectric nanomaterials for both niche and mass-market applications. For instance, Murata Manufacturing Co., Ltd.—a global leader in electronic components—continues to expand its portfolio of piezoelectric ceramics and is investing in miniaturized, high-performance devices for medical, automotive, and IoT applications. Similarly, TDK Corporation is advancing the integration of piezoelectric thin films into MEMS (Micro-Electro-Mechanical Systems), targeting high-volume markets such as mobile devices and wearables.
The next few years will likely see breakthroughs in scalable synthesis methods, such as low-temperature hydrothermal growth and atomic layer deposition, enabling cost-effective production of nanostructured piezoelectric materials. Companies like Piezotech (a subsidiary of Arkema) are pioneering printable piezoelectric polymers, which are expected to play a crucial role in flexible and stretchable electronics. These advances are supported by ongoing collaborations with research institutions and industry consortia focused on standardization and reliability testing.
A major disruptive opportunity lies in the integration of piezoelectric nanomaterials with energy harvesting systems. As the Internet of Things (IoT) ecosystem expands, self-powered sensors and devices are becoming increasingly attractive. Murata Manufacturing Co., Ltd. and TDK Corporation are both actively developing piezoelectric energy harvesters capable of converting ambient mechanical vibrations into usable electrical energy, with pilot deployments in smart infrastructure and industrial monitoring.
Looking toward 2030, the roadmap for piezoelectric nanomaterials engineering includes the development of lead-free, environmentally benign materials, improved device integration, and the scaling of manufacturing processes to meet global demand. Industry bodies such as the IEEE are expected to play a pivotal role in establishing standards and fostering cross-sector collaboration. As these innovations mature, piezoelectric nanomaterials are set to become foundational components in next-generation electronics, sustainable energy systems, and advanced healthcare technologies.
Sources & References
- Murata Manufacturing Co., Ltd.
- Kureha Corporation
- Robert Bosch GmbH
- STMicroelectronics
- NGK Insulators, Ltd.
- Piezotech
- Boston Piezo-Optics Inc.
- IEEE
- LG Electronics
- Medtronic
- Boston Scientific
- Noritake Co., Limited
- American Society of Mechanical Engineers (ASME)
- International Organization for Standardization (ISO)
- European Commission
- Semiconductor Industry Association
- Piezotech